Lanxess launches renewable, biocomposite material
The material combines natural flax fibers with bio-based polylactic acid, which acts as the matrix, for a material that is 100% recyclable.
Share
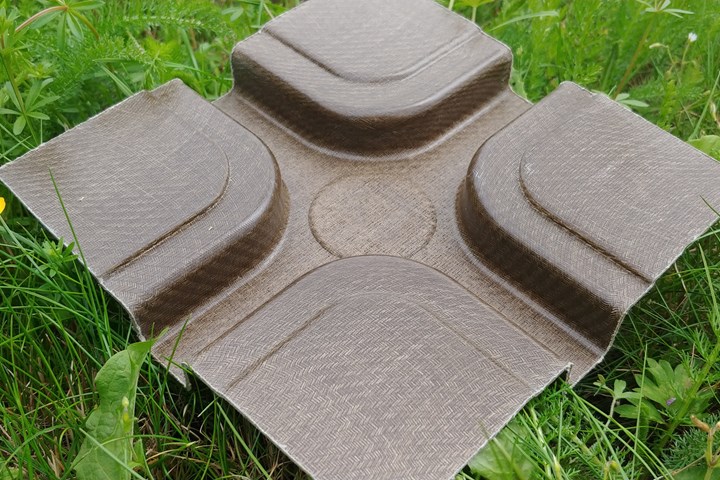
Photo Credit: Lanxess
Lanxess (Cologne, Germany) launches a new, fully biocomposite material in its Tepex range of continuous fiber-reinforced thermoplastic composites, in an effort to remove the reliance of fossil fuels from its own production processes. The material combines natural flax fibers with bio-based polylactic acid, which acts as the matrix, and can be produced on a large scale.
Lanxess’ continuous fiber-reinforced fabrics are said to be lighter in weight than glass fibers — flax fibers have a lower density — and offer mechanical performances typical of Tepex, which is based chiefly on the continuous fibers arranged in particular directions. The weight-specific stiffness of the biocomposite is also comparable to that of glass fiber-reinforced material variants. Further, designing the composite components to suit the expected loads enables most of the force to be transferred via the continuous fibers, ensuring high strength and stiffness.
In addition to sports equipment applications, the new biocomposite can reportedly be used in cars, such as for manufacturing interior parts, or in electronics for the production of housing components.
The material can also be 100% recycled. Lanxess notes that offcuts and production waste can be regranulated and easily injection molded or extruded, either alone or mixed with unreinforced or short fiber-reinforced materials.
In the medium term, Lanxess is planning to use other bio-based thermoplastics such as polyamide 11 and other natural and recycled fibers for the production of Tepex.
Related Content
-
McLaren celebrates 10 years of the McLaren P1 hybrid hypercar
Lightweight carbon fiber construction, Formula 1-inspired aerodynamics and high-performance hybrid powertrain technologies hallmark this hybrid vehicle, serve as a springboard for new race cars.
-
The potential for thermoplastic composite nacelles
Collins Aerospace draws on global team, decades of experience to demonstrate large, curved AFP and welded structures for the next generation of aircraft.
-
Infinite Composites: Type V tanks for space, hydrogen, automotive and more
After a decade of proving its linerless, weight-saving composite tanks with NASA and more than 30 aerospace companies, this CryoSphere pioneer is scaling for growth in commercial space and sustainable transportation on Earth.