AeroFurnace consortium develops composite thermal insulation
According to consortium partners, SGL Carbon, ZAE Bayern and FCT Systeme, up to 40% of the required process energy for high-temperature furnaces can be saved.
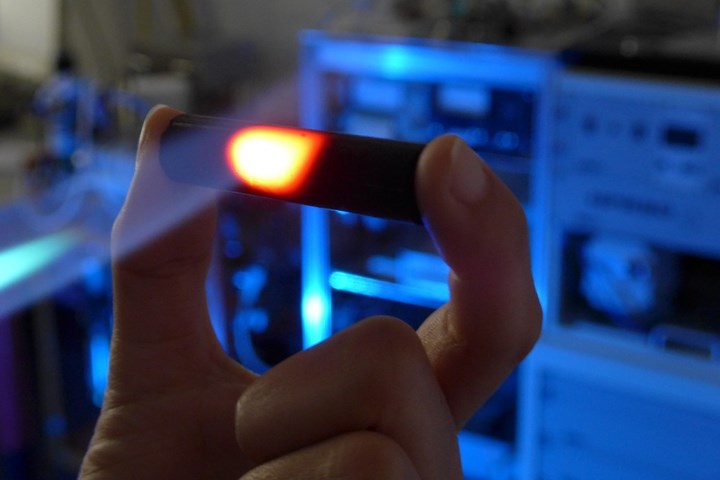
Sample from the development of the nano porous high-temperature thermal insulation material. Source | ZAE Bayern
On August 12, it was reported that consortium partners, SGL Carbon (Wiesbaden, Germany), the Bavarian Center for Applied Energy Research e.V. (ZAE Bayern, Würzburg, Germany) as joint coordinator and the furnace manufacturer FCT Systeme GmbH (Effelder-Rauenstein, Germany), have succeeded in improving the thermal insulation properties of a new composite material by up to 120% compared to commercially-available felt-based carbon materials. The joint project "AeroFurnace," is funded by the German Federal Ministry of Economic Affairs and Energy (BMWi). SGL Carbon notes that this achievement enables the project partners to move into a new quality level of thermal insulation in high-temperature industrial applications and pave the way for more energy efficient thermal insulation.
“In furnace simulations at FCT Systeme, we have already been able to demonstrate what the new material can do,” acknowledges Dr. Thomas Kirschbaum, project manager at SGL Carbon. “Depending on the temperature program, up to 40% of the required process energy can be saved with the thermal insulation material.” SGL notes that this prediction will be reviewed under real conditions in a demonstrator component in the second half of 2020 as part of the ongoing BMWi project.
SGL Carbon notes that the third largest share of energy in Germany is used for heat in industrial processes at 22.6%. Similarly, it is said that in many industries, such as the steel and ceramics industry, energy-intensive high-temperature processes run above 1000°C — these alone are said to require almost 50% of the industrial process heat. Thus, suitable thermal insulation materials can significantly reduce energy demand while maintaining the same usable volume.
It is said that, based on laboratory samples in plate form, the novel composite material is, in principle, scalable, and can be produced using simple processing methods. However, SGL notes that there is still a long way to go before the product is ready for serial production.
“As a manufacturer of industrial vacuum or inert gas high temperature furnaces, the new generation of insulating materials enables us to create furnaces with a more favorable ratio of usable space to external dimensions, thus offering customers improved cost efficiency and productivity,” says Dr. Jürgen Hennicke, project lead and head of R&D at FCT Systeme.
Dr. Gudrun Reichenauer, coordinator of the joint project and head of the work group Nanomaterials at ZAE Bayern, notes that in this project, “we have been able to make the latest findings from the world of nanomaterials accessible to the market through intensive cooperation and thus set new standards in the field of thermal insulation materials."
Related Content
-
PEEK vs. PEKK vs. PAEK and continuous compression molding
Suppliers of thermoplastics and carbon fiber chime in regarding PEEK vs. PEKK, and now PAEK, as well as in-situ consolidation — the supply chain for thermoplastic tape composites continues to evolve.
-
Natural fiber composites: Growing to fit sustainability needs
Led by global and industry-wide sustainability goals, commercial interest in flax and hemp fiber-reinforced composites grows into higher-performance, higher-volume applications.
-
Cryo-compressed hydrogen, the best solution for storage and refueling stations?
Cryomotive’s CRYOGAS solution claims the highest storage density, lowest refueling cost and widest operating range without H2 losses while using one-fifth the carbon fiber required in compressed gas tanks.