DigiProp positions Dowty Propellers and its customers for sustainable, next-generation platforms
AMRC aids R&D program including foam thermoforming, complex braiding, thermoplastics and digital twin/thread for higher performance, lower weight with first applications in process.
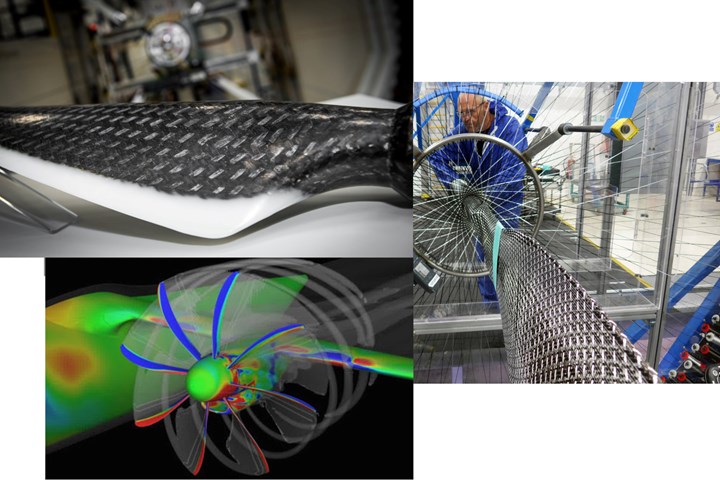
Dowty Propellers worked with the AMRC, MTC and NCC to evolve its composite blade manufacturing processes for lighter weight, higher performance and increased production volumes. Photo credit: Dowty Propellers, AMRC, NCC
Dowty Propellers (Gloucester, U.K.), a global leader in composite propeller systems and part of GE Aviation (Cincinnati, Ohio, U.S.), has announced the successful completion of its largest propeller research and development program: DigiProp. Dowty led the four-year, £20 million “Digital Propulsion” program, seeking to innovate every aspect of the design, manufacture and testing of its propeller systems.
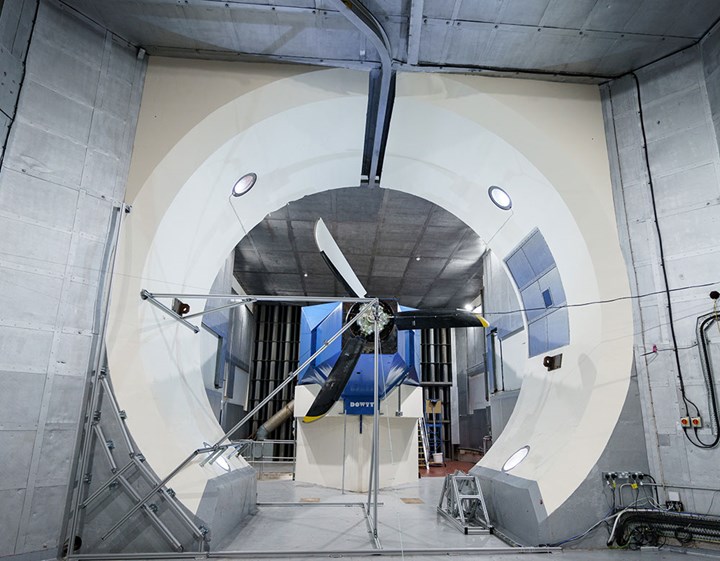
Evolving testing methods to better represent the operating environment has been a focus area in the DigiProp program. Photo credit: Dowty Propellers
DigiProp was funded by the UK government, in collaboration with three of the U.K.’s High Value Manufacturing Catapult centers: The University of Sheffield’s Advanced Manufacturing Research Centre (AMRC, Sheffield), The Manufacturing Technology Centre (MTC, Coventry) and The National Composites Centre (NCC, Bristol). Advances achieved include the scaling up of triaxial braiding for complex geometry structures, development of an automated foam thermoforming process as an alternative to casting or machining and successful use of robotic ultrasonic trimming for carbon fiber preforms. Additional developments include:
- Triaxial braiding was developed to an industrial scale, leveraging the directional properties of advanced composites to deliver performance and strength, while maximizing the benefits of lightweight properties to enable an overall blade weight reduction.
- Thermoplastic composites were developed, enabling recycling, waste reduction and tooling reuse, which supports the drive toward carbon neutrality.
- Introduction of a digital twin during the development of Dowty Propellers’ new factory not only optimized the factory’s footprint but also identified process bottlenecks for reduced manufacturing time and energy consumption, improved first-time yield performance and accelerated time to market for customers.
- Through complex data models, aerodynamic and acoustic performance improvements are now available for Dowty Propellers’ customers and the creation of a digital thread has laid the foundation for the use of big data.
AMRC on foam thermoforming, braiding and ultrasonic trimming
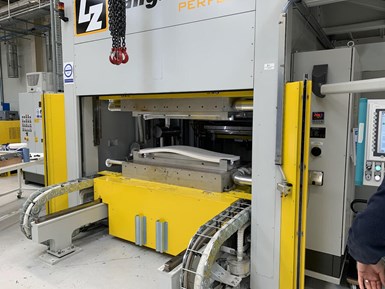
A Langzauner heated press was used with bespoke tooling to thermoform foam into shape. Photo Credit: Dowty Propellers, AMRC
“Through the DigiProp program, the AMRC Composite Centre has been able to push the boundaries of what is capable with composite manufacturing,” says Dr. Matt Smith, technical lead for composites simulation at the AMRC. “With foam thermoforming, this level of complexity isn’t something we’ve done before within the AMRC. Dowty Propellers was really interested and impressed with the results and wanted to continue this work beyond the end of DigiProp.”

AMRC’s KSL robot cell with ultrasonic knife attachment. KukaSim was used to work out the ideal position for the tool for the optimum cutting path. Photo Credit: Dowty Propellers, AMRC
“We’ve also succeeded in developing our triaxial braiding capability,” says Smith, “overcoming the challenges of scaling up manufacture. We began on small-scale trials at the University of Manchester with simple tubular structures and progressed to real-life airfoil geometry with the braid able to conform to the complex shape specified by Dowty Propellers.”
The AMRC Composite Centre team has also proved the feasibility of stitching stacks of material prior to shaping. This is followed by trimming to size using an ultrasonic knife mounted on a robot arm. “The ultrasonic trimming was really successful,” says Smith. “The benefits of this technology are that material stacks are stabilized in an efficient way and the ultrasonic cutting process can handle multiaxial cutting requirements.”
“The parametric propeller systems model we have developed allows us to use vastly more variables than a human mind could ever compute, allowing us to deliver thousands of years’ worth of manual calculation in a matter of weeks,” explains Jonathan Chestney, engineering leader at Dowty Propellers. “This gives our customers a faster design response and higher level of design optimization than ever before.”
AMRC is now looking for future projects in Foam Thermoforming and Ultrasonic Trimming.
NCC on commingled carbon/TP and bladder molding
As part of DigiProp, the NCC team reviewed the blade manufacturing workflow, exploring different technologies and processes to be able to input blade requirements and a set of geometric constraints to create as much flexibility as possible in the design of new blade structures.
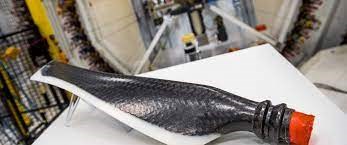
DigiProp prototype thermoplastic composite propeller blade. Photo Credit: Dowty Propellers, NCC
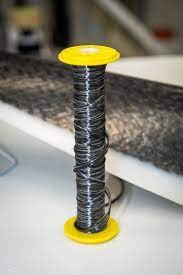
NCC explored using commingled thermoplastic and carbon fiber for DigiProp prototypes. Photo Credit: Dowty Propellers, NCC
NCC then designed and manufactured full-scale prototypes of a turboprop aircraft propeller blade as well as a novel manufacturing process that combines bladder molding with triaxial braiding of commingled thermoplastic and carbon fiber reinforcements. For the bladder system, a wax mold coated with silicone is used as a mandrel for overbraiding.
Various material compositions had to be tested because the blade needed to be durable and free of surface defects. The dry fiber preform also needed to retain its form and not sag, distort or move when being layered around the mandrel. This is to ensure correct positioning and alignment of the fibers to meet blade design intent and performance requirements.
The manufacturing process for the thermoplastic blade required development of a rigid mandrel for braiding that could be easily removed from the mold but have an inflatable silicone bladder remain after preforming. The latter would enable application of internal pressure for consolidation during cure. The silicone-coated wax mold provided a solution, but the thickness of the silicone had to be optimized to prevent failure of the bladder and incomplete consolidation of the composite blade.
By using thermoplastics, NCC reduced the cure cycle to roughly five minutes compared to four hours for typical thermoset epoxy resins. In one iteration, NCC removed foam core from the blade construction, observing a reduction in weight and improvement in both fatigue life and impact resistance. Six prototype propeller blades were developed in total, building on and enhancing design and manufacturing techniques each time.
NCC has reported that working on the DigiProp program was a unique opportunity to develop digital manufacturing technologies for blade designs with wider applications for other hollow 3D structures. Examples include economically recyclable composite components for smaller electric air vehicles. This work has led to a further project, the Novel Composite E-Bike, in which NCC has partnered with Bristol-based mountain bike manufacturer Starling Cycles and Composite Braiding, a leader in thermoplastic composite braiding technology.
Future technology deployed now
“This is the biggest research project we have ever undertaken at Dowty and it couldn’t have been better timed,” says Henry Johnston, President at Dowty Propellers. “We now have an advanced suite of new technologies, leaving us well positioned for the sustainable platform acceleration that is happening post-Covid.”
“This project has delivered innovations in propulsion performance and cost through design and productivity which has helped to transform R&D for propellers,” says Mark Scully, Head of Technology for Advanced Systems & Propulsion at the Aerospace Technology Institute. “With the assistance of the High Value Manufacturing Catapult partners, the manufacturing innovation has been deployed into the new state-of-the-art Dowty facility in Gloucester.”
The step-change in manufacturing capability made by the consortium opens up new opportunities to grow the UK’s aerospace propeller manufacturing base by harnessing composite technology with industrial digitalization to cut production costs and increase the performance of future propulsion systems in Europe’s €200 billion aviation sector.
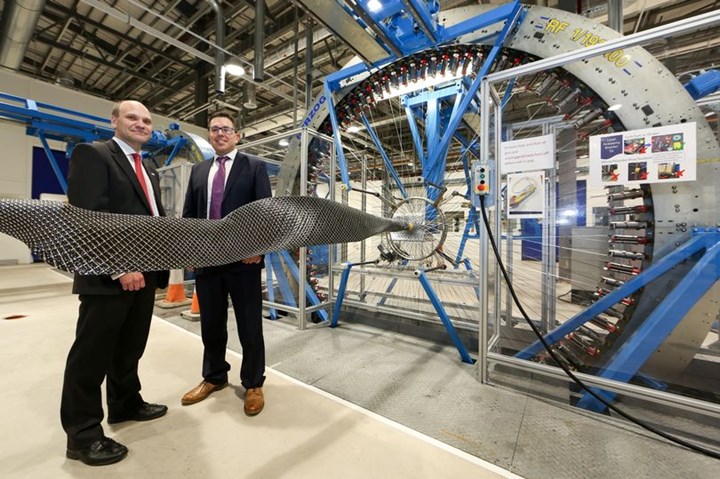
Dowty Propellers’ new manufacturing facility is already deploying DigiProp technologies for evolving aircraft applications and to target next generation platforms. Photo Credit: Anna Lythgoe for GloucesterLive
Dowty Propellers is now beginning to use the technologies realized in DigiProp for evolving aircraft applications and to target next-generation platforms. Potential customers are benefiting from the company’s ability to support trade studies with short turnaround time on performance analysis.
Dowty makes clear that DigiProp would not have been possible without support and funding from the ATI Program, a joint U.K. government and industry investment to maintain and grow the country’s competitive position in civil aerospace design and manufacture. The ATI program, delivered through a partnership between the Aerospace Technology Institute (ATI), Department for Business, Energy & Industrial Strategy (BEIS) and Innovate UK, addresses technology, capability and supply chain challenges.
Related Content
Plant tour: Joby Aviation, Marina, Calif., U.S.
As the advanced air mobility market begins to take shape, market leader Joby Aviation works to industrialize composites manufacturing for its first-generation, composites-intensive, all-electric air taxi.
Read MoreRecycling end-of-life composite parts: New methods, markets
From infrastructure solutions to consumer products, Polish recycler Anmet and Netherlands-based researchers are developing new methods for repurposing wind turbine blades and other composite parts.
Read MoreNatural fiber composites: Growing to fit sustainability needs
Led by global and industry-wide sustainability goals, commercial interest in flax and hemp fiber-reinforced composites grows into higher-performance, higher-volume applications.
Read MorePlant tour: Albany Engineered Composites, Rochester, N.H., U.S.
Efficient, high-quality, well-controlled composites manufacturing at volume is the mantra for this 3D weaving specialist.
Read MoreRead Next
“Structured air” TPS safeguards composite structures
Powered by an 85% air/15% pure polyimide aerogel, Blueshift’s novel material system protects structures during transient thermal events from -200°C to beyond 2400°C for rockets, battery boxes and more.
Read MoreAll-recycled, needle-punched nonwoven CFRP slashes carbon footprint of Formula 2 seat
Dallara and Tenowo collaborate to produce a race-ready Formula 2 seat using recycled carbon fiber, reducing CO2 emissions by 97.5% compared to virgin materials.
Read MoreDeveloping bonded composite repair for ships, offshore units
Bureau Veritas and industry partners issue guidelines and pave the way for certification via StrengthBond Offshore project.
Read More