FACC emphasizes fast-cure prepregs, thermoplastics, bio-based composites for next-gen aerostructure sustainability
The Tier One’s Sept. 2021 BEyond magazine highlights its investments in new factories, materials and technologies for the next generation of cost-effective, sustainable composites for aviation.
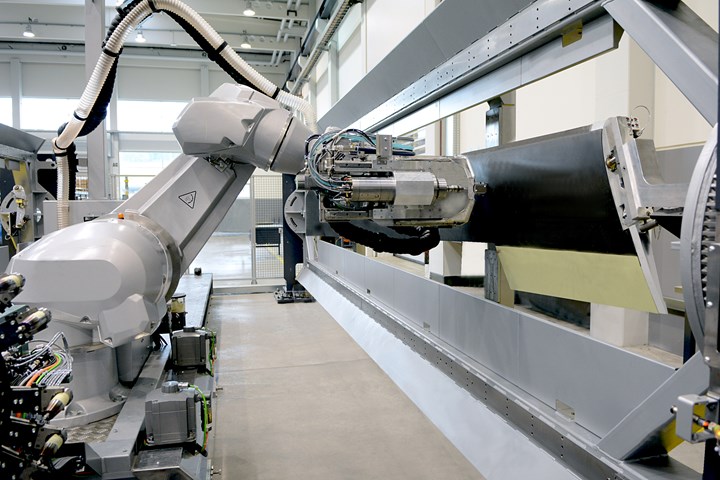
Photo Credit: FACC
FACC (Ried im Innkreis, Austria) is a leading Tier 1 aerospace supplier specializing in the production of lightweight systems for interiors, engines and airframes. In the September 2021 issue of its BEyond magazine, FACC highlights its new factory in Croatia for aircraft cabin components, the COMPETE program for its suppliers which stresses materials of the future and three R&D technologies that focus on composites: induction welding, hybrid injection molding and fast-curing prepregs.
FACC in Croatia
A high-tech plant is currently being built near Zagreb, Croatia. This 10,000-square-meter facility, scheduled to open in 2022, will produce lightweight cabin components for commercial aircraft and business jets using the latest fiber-reinforced composites technology. “This greenfield investment enables us to create a best-in-class plant that brings together cutting-edge technology, automation and 4.0 methods,” explains FACC CEO Robert Machtlinger. He notes the plant is conveniently located near FACC’s sites in Austria as well as the deepwater port of Koper. The plant also integrates former third-party services into its own value chain and establishes a foundation for future capacity increases.
COMPETE partner program
FACC launched the COMPETE partner program in February 2021 to reportedly strengthen its ties to selected partners and sustainably intensify cooperation. FACC suppliers will have the opportunity to generate new orders despite the ups and downs in the aviation market, but they must first successfully compete against other suppliers. FACC is assessing its suppliers according to the following criteria:
- Cost effectiveness
- Operational excellence
- Materials of the future — innovative materials for a step-change in products and production processes
- Partnership and passion
- Efficiency in all processes — including focused digitalization
- Transparency in quotations
- Environmental and social responsibility.
“COMPETE is all about fair competition and strong partnerships with suppliers that consistently perform well and have a particularly high potential,” says Andreas Ockel, COO of FACC. “We are focusing our future purchasing volume on our COMPETE program partners.” Within the next three years, FACC will redistribute €75 million of purchasing, aiming to decrease from 440 to fewer than 400 suppliers.
Giving more detail about materials of the future, Ockel explains that offering innovation in materials is key: “New fiber-reinforced composites materials shape our future! Snap-cure, fast-curing resin systems that drastically reduce production cycle times is an innovation that introduces genuine step changes in manufacturing processes. We are therefore looking to work closely with suppliers who provide this technological competitive edge.”

Photo Credit: FACC
Sustainability, investment and innovation
FACC asserts that it has helped to increase sustainability in the aviation industry through the aircraft parts it makes using lightweight composites and new aerodynamic shapes. To further reduce global CO2 emissions in the future, the company is working hard to develop technologies that make aircraft even lighter, quieter and more efficient.
FACC is currently researching composites using bio-based and/or bio-sourced materials, which it claims, should soon enable aircraft components to be fully recycled. “It’s about developing biological materials and new processes that consume less energy and offer greater performance but are still affordable,” says Machtlinger.
The company itself is becoming more sustainable, as well, aiming for its plants to be self sufficient in terms of energy and its productions processes to be carbon neutral by 2040. For the current decade, FACC’s Roadmap 2030 includes investments in new facilities like Zagreb, as well as new production methods, highlighted next.
Three R&D initiatives
FACC is developing induction welding of thermoplastic composites to replace screws and rivets in aircraft components and assemblies. An induction coil induces an eddy current in carbon fibers, generating heat (see “Welding thermoplastic composites”). The high-performance thermoplastic is then melted and consolidated in the weld area. Homogeneous welded joints of fiber-reinforced thermoplastic composites are used in rudders, elevators and flaps. They can be joined more quickly and efficiently compared to mechanical fastening or adhesive bonding and can be fully automated.
Hybrid injection molding is described as an efficient way to functionalize fiber-reinforced composites. The process consolidates a semi-finished material into a laminate, which is then heated, reshaped and overmolded using an injection molding compound. A major advantage of this process is that it enables recycling; waste can be reprocessed and used in the injection molding compound. It is also possible to integrate stiffening elements and produce complex components such as aircraft interiors or fairings.
Fast-curing prepregs offer enormous potential to reduce composites curing time during production by up to 90%. This enables even parts made with thermoset resins to be produced in a matter of minutes, using a robust and energy-efficient process. FACC reports that fast-curing prepregs are simpler to work with than thermoplastic composite materials. The company also sees these materials as a route to improved sustainability, because the resins needed for interior products, for example, can be made from renewable raw materials based on sugar cane, bamboo or algae.
Related Content
Natural fiber composites: Growing to fit sustainability needs
Led by global and industry-wide sustainability goals, commercial interest in flax and hemp fiber-reinforced composites grows into higher-performance, higher-volume applications.
Read MoreBcomp ampliTex makes appearance in Cupra EV Cup Bucket seats
The entire Cupra Born VZ line-up features all-natural fiber front seats that highlight functionality, aesthetics and reduced CO2 emissions.
Read MoreDITF Denkendorf advances sustainable carbon fibers, oxide fibers for CMC and more
The German Institutes of Textile and Fiber Research are targeting more sustainable carbon fiber via low-pressure stabilization and bio-based precursors, and working with Saint-Gobain to commercialize oxide ceramic fibers for CMC.
Read MoreFlax composites enter serial automotive production via Volvo EX30
The small SUV, which focuses on sustainability and is designed to have the lowest carbon footprint of any model in Volvo Cars’ history, incorporates Bcomp ampliTex fibers in its dashboard and door trim.
Read MoreRead Next
FACC develops and manufactures composite structures for Ariane 6 launch vehicle
Astris kick stage main structure will be characterized by high strength and the use of ultralight carbon fiber material, with first delivery scheduled for October 2022.
Read More“Structured air” TPS safeguards composite structures
Powered by an 85% air/15% pure polyimide aerogel, Blueshift’s novel material system protects structures during transient thermal events from -200°C to beyond 2400°C for rockets, battery boxes and more.
Read MoreDeveloping bonded composite repair for ships, offshore units
Bureau Veritas and industry partners issue guidelines and pave the way for certification via StrengthBond Offshore project.
Read More