FACC receives Airbus "Innovation Award"
The award was presented to FACC for its contribution to composite components for the Airbus Wing of Tomorrow program.
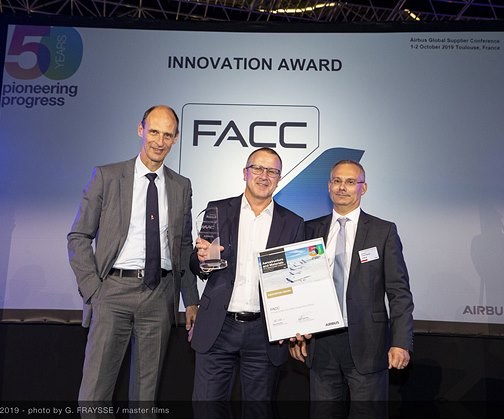
Source | FACC
FACC ((Innkreis, Austria) has announced that it recently received an “Innovation Award” from Airbus for its contributions to the Wing of Tomorrow project. The award was presented to FACC by Dr. Klaus Richter, chief procurement officer at Airbus, during last week’s Airbus Global Supplier Conference.
“I am particularly pleased that our innovative strength has been honored with the Airbus Innovation Award,” says Robert Machtlinger, CEO of FACC. “I owe a lot of gratitude to my dedicated team who, in close cooperation with the Airbus teams, developed a technically sophisticated and high-quality solution as part of the research and development project into new architectures for carbon wings set to improve the overall eco-efficiency and aircraft performance of next generation aircraft, within a very short development period.”
For the Wing of Tomorrow project, FACC contributed to the development of a composite aircraft wing that had the goal of ensuring maximum performance in terms of wing technology while also maximizing manufacturing efficiency. The goal of the collaboration is to develop and integrate new production technologies for the wings of single-aisle aircraft by incorporating new materials and processes that enable automated high-volume series production. The new aircraft components must meet numerous requirements such as a high degree of maturity in production, lower costs and suitability for high-rate production. FACC has developed three demonstrators for the essential parts of a wing box lower cover.
“The Wing of Tomorrow project is of great strategic importance for FACC. It allows us to further expand our research network with Airbus and partner companies,” says Christoph Schöndorfer, head of innovation at FACC.
Andreas Furthmayr, VP of aerostructures, adds: “In the Aerostructures segment, we place great emphasis not only on weight and functionality, but also on cost-efficient and highly automatable component production. The experience we have gained in the development and manufacture of wing box covers will enable us to enter a new product segment and expand our portfolio.”
Related Content
-
The potential for thermoplastic composite nacelles
Collins Aerospace draws on global team, decades of experience to demonstrate large, curved AFP and welded structures for the next generation of aircraft.
-
Plant tour: Middle River Aerostructure Systems, Baltimore, Md., U.S.
The historic Martin Aircraft factory is advancing digitized automation for more sustainable production of composite aerostructures.
-
Combining multifunctional thermoplastic composites, additive manufacturing for next-gen airframe structures
The DOMMINIO project combines AFP with 3D printed gyroid cores, embedded SHM sensors and smart materials for induction-driven disassembly of parts at end of life.