FACC supplies 1,000th composite translating sleeve shipset for Airbus A350
Maximum investment in development and production of the lightweight components supports lower fuel consumption and significant reduction in CO2 emissions for the A350 family.
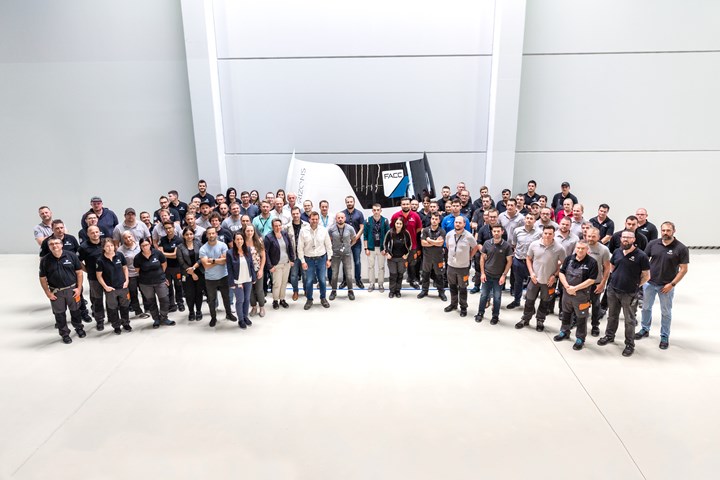
Photo Credit: FACC
With the aircraft industries swift recovery the last six months, FACC (Ried im Innkreis, Austria) has announced demand for new short- and medium-haul aircraft is up by 20% in Q4 2021. With long-haul aircraft, FACC is also celebrating a newly achieved milestone, with the deliverance of its 1,000th shipset of composite translating sleeves for the A350 to its customer, Collins Aerospace (Charlotte, N.C., U.S.).
FACC notes that composite components account for 50% of the Airbus A350’s weight, making it one of the most advanced and efficient aircraft on the market; 25% less fuel is consumed compared to its predecessors, and it’s also reported to be 60% quieter.
“With our years of know-how, we can provide both greater efficiency and lower noise emissions. This is our contribution to making flying more sustainable,” enthuses Robert Machtlinger, CEO of FACC. In order to occupy a strong market position as a pioneer in this field, the international aerospace group relies on cutting-edge technologies and innovative manufacturing concepts. “The first lightweight components for the translating sleeves of the Airbus A350 were delivered in 2010. Eleven years later, we are proud to be able to deliver the 1,000th translating sleeve shipset to our long-standing customer, Collins Aerospace,” he emphasizes.
According to Machtlinger, this success was not achieved overnight. Since the beginning of the project, FACC has invested approximately 50 million euros in the development and production of the components in order to offer Collins Aerospace and Airbus a translating sleeve that is as lightweight and fuel-efficient as possible, while gearing the production line towards maximum efficiency and ergonomics. Around 50 employees are currently working on the program.
“The long-haul segment is developing with a slight lag compared to the short- and medium-haul segment, but we expect the demand for A350 aircraft to continue to rise as the restrictions on transcontinental travel are gradually lifted,” explains Machtlinger.
Translating sleeves for the Airbus A350 family, are the main components of the thrust reverser. In addition to the outer parts of the thrust reverser and the movable blocker doors, they also contain the mechanical connecting elements required to operate these panels. Alongside the wing spoiler and the landing gear brakes, the thrust reverser is the third component in the brake system of modern commercial aircraft.
In this project, FACC says it has tailored the production line of lightweight components at Plant 4 in Reichersberg (Austria) towards maximum efficiency and, together with its customer Collins Aerospace, has incorporated technological innovations into the design of the translating sleeves. The use of newly developed composite materials generates considerable weight savings, which in turn result in lower fuel consumption and a significant reduction in CO2 emissions. At the same time, special acoustic treatment of the components means that significant noise emissions are directed from the engines to the exterior. “This anniversary delivery is a valuable confirmation of the cooperation with Collins Aerospace. I would like to thank our long-standing customer for their trust, and the FACC project team for their commitment and dedication throughout the entire project,” says Machtlinger.
Related Content
The potential for thermoplastic composite nacelles
Collins Aerospace draws on global team, decades of experience to demonstrate large, curved AFP and welded structures for the next generation of aircraft.
Read MoreNext-generation airship design enabled by modern composites
LTA Research’s proof-of-concept Pathfinder 1 modernizes a fully rigid airship design with a largely carbon fiber composite frame. R&D has already begun on higher volume, more automated manufacturing for the future.
Read MoreWelding is not bonding
Discussion of the issues in our understanding of thermoplastic composite welded structures and certification of the latest materials and welding technologies for future airframes.
Read MorePlant tour: Joby Aviation, Marina, Calif., U.S.
As the advanced air mobility market begins to take shape, market leader Joby Aviation works to industrialize composites manufacturing for its first-generation, composites-intensive, all-electric air taxi.
Read MoreRead Next
FACC expands partnership with Airbus
Expanded empennage component production for A220 family positions FACC as an important long-term technology partner to Airbus, supports the company’s growth strategy for the future.
Read MoreVIDEO: High-volume processing for fiberglass components
Cannon Ergos, a company specializing in high-ton presses and equipment for composites fabrication and plastics processing, displayed automotive and industrial components at CAMX 2024.
Read MorePlant tour: Daher Shap’in TechCenter and composites production plant, Saint-Aignan-de-Grandlieu, France
Co-located R&D and production advance OOA thermosets, thermoplastics, welding, recycling and digital technologies for faster processing and certification of lighter, more sustainable composites.
Read More