Ferrari 812 Competizione makes extensive use of carbon fiber
Composite materials enhance performance and minimize mass for a faster vehicle. The limited edition car also offers fully composite wheels, which weigh 42% less than alloy options.
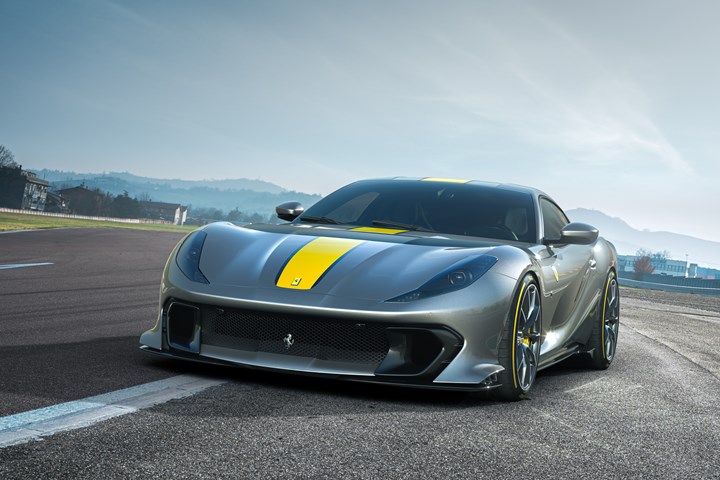
The Ferrari 812 Competizione makes extensive use of carbon fiber components, not only for mass reduction but for air management. All photo credit: Ferrari
Ferrari (Maranello, Italy) has launched a limited edition car, the 812 Competizione, which is available both as a coupe and with a targa top — a carbon fiber targa top. The car is powered by a naturally aspirated 6.5-liter V12 that produces 819 horsepower.
The 812 Competizione is based on the 812 Superfast. Efforts were made to not only enhance the performance of the vehicle, but to minimize mass. The 812 Competizione, at 1,487 kilograms, is 38 kilograms lighter than the Superfast.
This mass reduction effort took place in all aspects of the car, whether it was the use of titanium con rods in the engine, or carbon fiber trim for the cockpit. The body shell is one area where there is extensive use of the composites, including the front and rear bumpers, rear spoiler and air intakes.
One of most the notable features on the front of the car is the transverse groove in the hood into which a carbon fiber blade is fitted. This is for both function and aesthetic. As for the former, it increases the surface area of the vents that provide air to the engine, while the latter makes the hood appear cleaner than would be the case were traditional louvers used.
Cooling the brakes
The car has a top speed in excess of 211 miles per hour and can accelerate from 0 to 100 kilometers per hour in 2.85 seconds. So as can be expected, when the driver gets on the binders, there can be severe brake heating.
As a result, there are two carbon fiber air intakes, square in section, that flank the main grille (below which sits a carbon fiber splitter). The air intakes both provide brake cooling and provide air curtains that work to minimize the turbulence cause by the outer part of the front tires.
Lightening wheels
Weight savings also take the form of all-carbon fiber rims, which are being made available on a Ferrari V12 for what is said to be the first time. Compared to the forged wheels on the 812 Superfast, there is a total mass reduction of 3.7 kilograms.
The carbon fiber wheels are being produced by Carbon Revolution (Geelong, Australia), which has produced wheels for other Ferraris: the F8 Tributo, SF90 and 488 Pista.
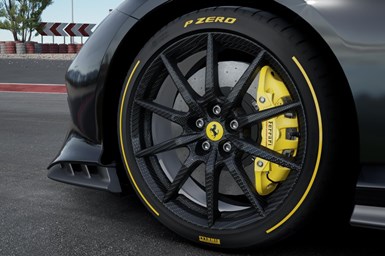
A composite wheel is available for the first time on a Ferrari V12 vehicle. It is produced by Carbon Revolution and is said to be 42% lighter than a comparable forged wheel.
According to Ashley Denmead, engineering and design director/co-founder of Carbon Revolution, the carbon fiber wheel weighs 42% less than a comparable alloy wheel.
When asked about the engineering of the wheel itself, Denmead points out that it is made entirely from carbon fiber, then adds, “There are many other proprietary elements to this wheel, including a plasma applied thermal barrier coating which protects against cases of misuse that may cause brake rotors and discs to overheat. This thermal barrier coating is less than 300 microns in thickness but can reduce thermal transmission by over 100°C.”
Denmead says that the manufacture of the wheel requires highly precise carbon fiber placement combined with high-pressure molding. The manufacturing processes for wheel production were developed in-house.
Denmead says, “Carbon Revolution has not only developed a highly automated manufacturing line, but also extensively uses machine learning and artificial intelligence to optimize production.”
Related Content
ASCEND program update: Designing next-gen, high-rate auto and aerospace composites
GKN Aerospace, McLaren Automotive and U.K.-based partners share goals and progress aiming at high-rate, Industry 4.0-enabled, sustainable materials and processes.
Read MoreCarbon fiber, bionic design achieve peak performance in race-ready production vehicle
Porsche worked with Action Composites to design and manufacture an innovative carbon fiber safety cage option to lightweight one of its series race vehicles, built in a one-shot compression molding process.
Read MoreThermoplastic composites: Cracking the horizontal body panel nut
Versatile sandwich panel technology solves decades-long exterior automotive challenge.
Read MoreComposites end markets: Automotive (2024)
Recent trends in automotive composites include new materials and developments for battery electric vehicles, hydrogen fuel cell technologies, and recycled and bio-based materials.
Read MoreRead Next
All-composite EV wheel moves to next development phase
U.K. consortium partners’ ACRIM II project aims to develop a low-cost, lightweight, all-composite wheel for electric vehicle applications.
Read MoreBercella carbon fiber bodywork meets aesthetics, aerodynamics and performance
The Italy-based company collaborated with Romeo Ferraris on the design and production of the new, all-electric Alfa Romeo Giulia ETCR car to compete in the 2021 Pure ETCR.
Read More“Structured air” TPS safeguards composite structures
Powered by an 85% air/15% pure polyimide aerogel, Blueshift’s novel material system protects structures during transient thermal events from -200°C to beyond 2400°C for rockets, battery boxes and more.
Read More