Full process, quality control brings Diab closer to Composites 4.0
Developed by 2550 Engineering, an automated inline system helps measures 100% of samples in real time, ensuring a complete quality control process.
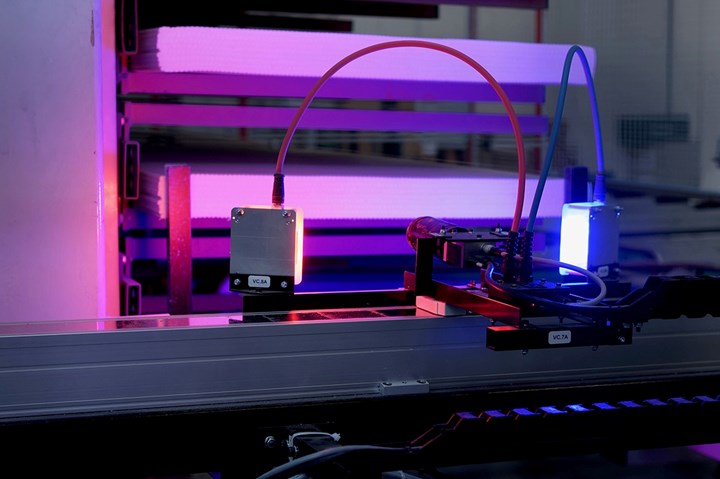
Automated inline process involves a high-resolution vision sensor, colored lights and machine learning. Photo Credit: Diab
Progressive technology consultancy 2550 Engineering (Gothenburg, Sweden), a Qamcom Group company, has collaborated with Diab (Laholm, Sweden), to optimize process and quality control in the production of the company’s sandwich composite solutions used in marine, wind, aerospace and automotive industries.
“Diab came to us with the ambition to perform inline quality control for every sample and provide an individual material property set for each produced sample. This would take Diab from occasionally checking samples manually, to measuring the quality of all material produced. Some would say that it sounds impossible. We said, challenge accepted,” says Magnus Janson, CEO at 2550 Engineering.
With the help of a high-resolution vision sensor, colored lights and machine learning (ML), 2550 Engineering developed an automated inline system that captures the samples’ structure in real time. The result was that Diab moved from measuring one out of 10,000 samples, to all of them.
“We chose 2550 for this complex task because of their can-do attitude, responsiveness and high skills within forefront technology and Industrial AI,” notes Magdalena Sandström, CTO at Diab Group. “It would be an understatement to say that they have delivered value for us. I would go so far as to say that they have helped us to understand how to use new technologies, such as machine learning, to revolutionize our whole quality control process.”
With this new vision system in place, Diab now has access to the quality data needed to optimize its process control, reduce costs and waste and improve product quality in general.
“Throughout the whole process we have had a tight collaboration together with Diab, something that was crucial to create good results fast” says Janson.
Related Content
-
Ultra high-rate composite deposition system trials to surpass layup targets
The NCC, alongside partners Loop Technology, Coriolis and Güdel, are on track to deliver dry fiber deposition rates exceeding 350 kilograms/hour, seven times more than standard aerospace rates.
-
ST Engineering MRAS presents initiatives to drive autoclave efficiency, automation
During a JEC World 2024 panel discussion, the company revealed ways in which it is maximizing throughput and efficiency of its autoclaves and enhancing composites production processes.
-
Com&Sens presents workshop on fiber optic sensing for COPVs
Three-day hands-on workshop from June 11-13 in Leuven, Belgium, will equip participants with a better understanding of fiber optic sensing technology for digital manufacturing of composite tanks.