Heat resistance testing provides insight into preventing carbon fiber-reinforced UHTC degradation
Japan-based researchers use an arc-wind tunnel to better understand carbon fiber-reinforced ultrahigh-temperature ceramic matrix composites oxidation resistance in high-temp, inert atmospheres.
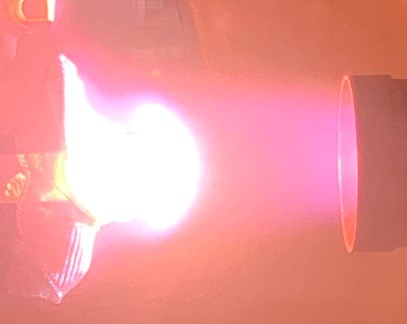
Researchers from the Tokyo University of Science evaluated the utility of C/UHTCMC at temperatures above 2,000ºC using arc-wind tunnel testing (pictured above). These results show degradation of the composite at high temperatures, which is an important result for the manufacture of advanced space shuttle orbiters. Photo Credit: Ryo Inoue from Tokyo University of Science, Japan
Carbon fiber-reinforced ultrahigh-temperature ceramic (UHTC) matrix composites are extensively used in space shuttles and high-speed vehicles. However, these composites suffer from a lack of oxidation resistance. Recently, researchers from Japan tested the heat resistance of UHTC at very high temperatures, providing insight into the modifications needed to prevent UHTC degradation, findings which could potentially have large implications for the manufacture of space shuttle orbiters.
Carbon fiber-reinforced carbon (C/C), for example, is a composite material made of carbon fiber reinforced in a matrix of glassy carbon or graphite. It is best known as the material used in hypersonic vehicles and space shuttle orbiters, which cruise at speeds greater than Mach 5. Since the 1970s, it has also been used in the brake system in Formula One racing cars. Even though C/C has excellent mechanical properties at high temperatures and inert atmospheres, it lacks oxidation resistance in these conditions, making its widespread use limited.
Researchers have found that UHTCs, which include transition metal carbides and diborides, show good oxidation resistance. In previous studies, zirconium-titanium (Zr-Ti) alloy infiltration showed promising results for improving the heat resistance of carbon fiber-reinforced UHTC matrix composites (C/UHTCMCs). However, their use at high temperatures (>2,000ºC) is not known.
Set against this backdrop, a group of researchers from Japan have evaluated the potential utility of Zr-Ti alloy-infiltrated C/UHTCMCs at temperatures above 2,000ºC. Their study, led by junior associate professor Ryo Inoue from Tokyo University of Science (TUS, Japan), was published in the Journal of Materials Science and made available online on Oct. 27, 2022. The research team consisted of Noriatsu Koide and assistant professor Yutaro Arai from TUS, Professor Makoto Hasegawa from Yokohama National University (Japan) and Dr. Toshiyuki Nishimura from the National Institute for Materials Science (NIMS, Tsukuba, Japan).
“The research is an extension of the research and development of ceramics and ceramics-based composite materials,” Prof. Inoue says. “In recent years, we have received inquiries from several manufacturers of heavy industries regarding materials that can be used at temperatures above 2,000°C. We have also started to work with these manufacturers to develop new materials.”
The C/UHTCMC was manufactured using melt infiltration, which is reported to be the most cost-effective way to fabricate these materials. To study the applicability of this material, three types of C/UHTCMCs were fabricated with three different alloy compositions. The three alloy compositions used had varying atomic ratios of Zr:Ti. To characterize the heat resistance, the team used a method called arc-wind tunnel testing. This method involves exposing the material to extremely high enthalpy airflow inside a tunnel, similar to conditions that spacecrafts experience while re-entering the atmosphere.
The team found that the amount of Zr in the alloy had a strong effect on the degradation of the composite for all temperatures. This is owing to the thermodynamic preference for the oxidation of Zr-rich carbides compared to Ti-rich carbides. Further, the Zr and Ti oxides formed on the composite surface prevented further oxidation, and the oxide composition depended on the composition of the infiltrated alloys. Thermodynamic analysis revealed that the oxides formed on the composite surface were composed of ZrO2, ZrTiO4, and TiO2 solid solutions.
At temperatures above 2,000ºC, the thickness and weight of the samples increased with the Zr content of the composites after the arc-wind tunnel tests. The team also observed that the melting point of the surface oxides increased as the Zr content increased. For temperatures above 2,600ºC, the only oxides formed were liquid-phase, requiring a thermodynamic design of the matrix composition to prevent the recession of UHTC composites.
“We have successfully studied the degradation of C/UHTCMC at temperatures above 2,000ºC using thermodynamic analysis,” Prof. Inoue adds. “We have also shown that the matrix design needs modification to prevent the degradation of the composites. Our research has the potential to contribute to the realization of ultrahigh-speed passenger aircraft, re-entry vehicle and other hypersonic vehicles.”
Related Content
Manufacturing the MFFD thermoplastic composite fuselage
Demonstrator’s upper, lower shells and assembly prove materials and new processes for lighter, cheaper and more sustainable high-rate future aircraft.
Read MorePEEK vs. PEKK vs. PAEK and continuous compression molding
Suppliers of thermoplastics and carbon fiber chime in regarding PEEK vs. PEKK, and now PAEK, as well as in-situ consolidation — the supply chain for thermoplastic tape composites continues to evolve.
Read MorePlant tour: Joby Aviation, Marina, Calif., U.S.
As the advanced air mobility market begins to take shape, market leader Joby Aviation works to industrialize composites manufacturing for its first-generation, composites-intensive, all-electric air taxi.
Read MoreASCEND program update: Designing next-gen, high-rate auto and aerospace composites
GKN Aerospace, McLaren Automotive and U.K.-based partners share goals and progress aiming at high-rate, Industry 4.0-enabled, sustainable materials and processes.
Read MoreRead Next
Nanocomposite films boost heat dissipation in thin electronics
Scientists from Japan develop cellulose nanofiber-carbon fiber composite films with high in-plane heat conductivity to assist in heat dissipation in electronic devices.
Read MoreAdvanced Composite Structures Australia invests in ultra-high-temperature composites manufacturing
Funding supports specialized equipment and development of automated processes to manufacture ultra-high-temp composite hypersonic and space vehicle parts.
Read MoreDeveloping bonded composite repair for ships, offshore units
Bureau Veritas and industry partners issue guidelines and pave the way for certification via StrengthBond Offshore project.
Read More