Nordic Bioproducts successfully spins novel plant-based textile fiber
The Finnish startup begins an intensive product development period to scale up its Norratex fiber, which is manufactured without toxic chemicals or expensive solvents.
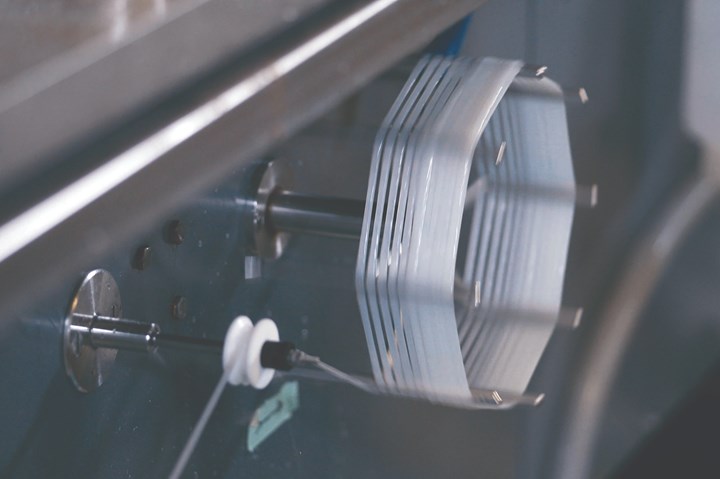
Norratex wet spinning process. Photo Credit, all images: Photino Science, Pentti Pällijeff
Nordic Bioproducts Group (NBG, Espoo, Finland) reports that it has successfully spun a new plant-based textile fiber, Norratex, which is manufactured without any toxic chemicals or expensive solvents. At a recent press conference, the company also revealed its collaboration with CMPC Ventures (Santiago, Chile), the Corporate Venture arm of CMPC S.A, one of the largest producers of pulp in the world.
The Finnish startup company is a spin-off from Aalto University that develops and commercializes smart biotechnologies to redesign cellulose into high-value bioproducts; it is the proprietor of the patented AaltoCell which has opened new markets for microcrystalline cellulose.
According to NBG, new and sustainable alternatives from wood- and plant-based feedstock are required to address the sustainability challenges of the textile industry. The market for sustainable, man-made cellulosic fibers is also expected to grow above 10% within the next decade. The company lists several Finnish innovations in this field that are ramping up textile fibers, from Spinnova Oy (Jyväskylä), Metsä Spring Oy (Espoo), Kuura (Espoo) and Infinited Fibre Co. (Espoo), to Aalto University’s Ioncell fiber.
To produce Norratex, the cellulose is first hydrolyzed in an environmentally friendly, cost-effective manner. The fiber is then processed further into a viscose-like textile fiber. The inventor of the AaltoCell method, Professor Olli Dahl at Aalto University, was convinced from early on that the method, developed by NBG, could be applied in the production of plant-based textile fibers, as the Norratex method can use a wide variety of raw material sources, such as forest industry byproducts, textile waste and ordinary paper pulp; this is said to be a significant advantage over traditional viscose, which is made from dissolving pulp and can have a cost 30% higher than paper pulp.
“It’s great to see when your own ideas lead to new products by the skillful team of engineers in a young company. We are embarking on a new era in developing novel bio-based products,” Dahl says.
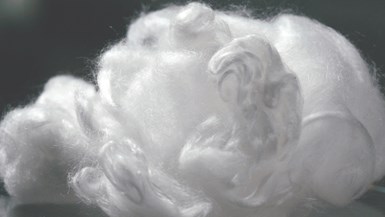
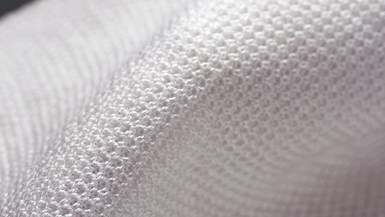
Norratex fiber (above) and sample (below).
In 2020, NBG began to develop a cost-effective and scalable textile fiber manufacturing process in collaboration with the University of Tampere (Finland), based on Dahl’s idea. NBG’s team of chemical and fiber processing engineers were able to find just the right parameters for the dissolution that enables wet spinning of the cellulose dope.
The first wet spinning experiments with NBG’s cellulose dissolution method were performed in June 2021. Six months later, in November 2021, yarn was successfully produced via the Norratex textile fiber at the University of Tampere. Several samples of the yarn were knitted at the Department of Design at Aalto University.
Maija Järventausta, a researcher who carried out wet spinning and yarn production in Tampere, describes the success. “The seventh spinning experiment really surprised me. The dope was excellent and it did not clog the spinneret during wet spinning. At that moment, I suggested that we should try making yarn for the first time. In the next step, the carding was successful, the fiber withstood opening, curled beautifully and no pilling was formed. Fiber-to-fiber friction was optimal. I would never have believed that in such a short period of product development, one could succeed in a functional end product. It was great to see that the yarn was strong enough not to break in the knitting process. The yarn also has a beautiful, subtle gloss, a feature that lasted from wet spinning to the dry yarn.”
Several partners are now involved in the development and commercialization of the new fiber, the most important of which is CMPC Ventures. “Collaboration patterns are central to the success of the project,” says Olli Kähkönen, co-founder and innovation director at Nordic Bioproducts, emphasizing the scale of the project. “We are partnering with CMPC to begin an intensive product development period of approximately one year. After that, if everything goes as planned, we will start producing Norratex textile fiber on a pilot scale.”
Related Content
Cryo-compressed hydrogen, the best solution for storage and refueling stations?
Cryomotive’s CRYOGAS solution claims the highest storage density, lowest refueling cost and widest operating range without H2 losses while using one-fifth the carbon fiber required in compressed gas tanks.
Read MoreTU Munich develops cuboidal conformable tanks using carbon fiber composites for increased hydrogen storage
Flat tank enabling standard platform for BEV and FCEV uses thermoplastic and thermoset composites, overwrapped skeleton design in pursuit of 25% more H2 storage.
Read MoreBio-based acrylonitrile for carbon fiber manufacture
The quest for a sustainable source of acrylonitrile for carbon fiber manufacture has made the leap from the lab to the market.
Read MoreNatural fiber composites: Growing to fit sustainability needs
Led by global and industry-wide sustainability goals, commercial interest in flax and hemp fiber-reinforced composites grows into higher-performance, higher-volume applications.
Read MoreRead Next
Plant tour: Daher Shap’in TechCenter and composites production plant, Saint-Aignan-de-Grandlieu, France
Co-located R&D and production advance OOA thermosets, thermoplastics, welding, recycling and digital technologies for faster processing and certification of lighter, more sustainable composites.
Read MoreVIDEO: High-volume processing for fiberglass components
Cannon Ergos, a company specializing in high-ton presses and equipment for composites fabrication and plastics processing, displayed automotive and industrial components at CAMX 2024.
Read MoreDeveloping bonded composite repair for ships, offshore units
Bureau Veritas and industry partners issue guidelines and pave the way for certification via StrengthBond Offshore project.
Read More