Shanghai Electric launches 11-MW, direct-drive offshore turbine with 102-meter blades using carbon fiber
Able to withstand high temperatures, earthquakes and typhoons, the SEW11.0-208 platform mark another breakthrough, in addition to the launched S120, S89 and S90 composite wind blades.
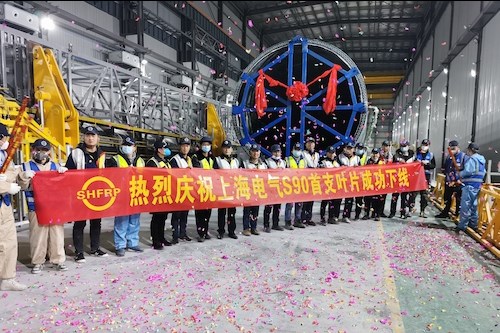
Photo Credit: Shanghai Electric
On Oct. 14, Shanghai Electric (Shanghai, China) announced the release of its latest offshore wind turbine model, Petrel platform SEW11.0-208 boasting 102-meter carbon fiber wind blades, at a forum that invited the leaders in China’s wind power industry to shed light on opportunities to reduce carbon emissions. Another stride forward along its offshore innovation pathway, the Shanghai Electric's flagship direct-drive turbine, of which the company has full proprietary intellectual property, features a nameplate capacity of 11 megawatts (MW) — reported to be the largest of its kind in Asia — marking a breakthrough for China’s homegrown innovation in offshore wind technology.
SEW11.0-208 is the first offshore wind turbine to take full advantage of the prowess of Shanghai Electric’s self-developed Petrel platform that is designed to withstand high temperatures, humidity and salt, as well as changeable and complex marine environments such as earthquakes and typhoons. Against the backdrop of China’s carbon neutrality goals, SEW11.0-208 is an extension of Shanghai Electric’s effort in making wind energy a dominant energy source by launching a highly economical direct-drive wind power product capable of maintaining high power-generation efficiency and a low failure rate in both ordinary and typhoon sea areas.
Adopting full-cycle digital design, production, O&M management, SEW11.0-208 is said to harness Shanghai Electric’s latest LeapX control system to reduce operating load and improve the operating stability of the unit. The fully digitized turbine is supercharged by Shanghai Electric’s Fengyun system, a cloud-based remote management platform, to boost operational efficiency and profitability for developers. Moreover, the turbine’s S102 102-meter carbon fiber blades, which were independently developed and rolled out by the company in September 2021, are suitable for use in Category I typhoon areas on the sea; the blades are reported to be the longest produced in China.
“As a global leader in offshore wind, Shanghai Electric is dedicated to helping China achieve peak carbon and carbon neutrality by leveraging its extensive proven technology in the field of renewable energy,” says Jin Xiaolong, vice president of Shanghai Electric. “The launch of our Petrel platform is a huge achievement for Shanghai Electric, which marks an important leap forward in our journey as we explore better and superior new energy products and solutions that lead the world stepping towards a greener future.”
Shanghai Electric, as one of the innovation powerhouses in China’s wind power industry, says it will continue spearheading the development of renewable technologies to support China’s carbon neutrality goal using big data, cloud computing, Internet of Things (IoT), artificial intelligence and 5G, pioneering technological innovations to establish an advanced zero-carbon power system.
This focus is further established by the company’s three record-breaking wind turbine lengths produced so far. In addition to its S102 blades being used in the SEW11.0-208 offshore wind turbine, and the S89 onshore wind blade for new-generation wind turbine units, Shanghai Electric rolled out its S90 blade, which passed the full-scale static load test, and gained certification by the China Quality Certification Center back in February 2021. The 90-meter glass fiber wind turbine blade is designed for offshore use in areas of medium and low wind speeds in China via Shanghai Electric’s 6.5-MW turbine
Shanghai Electric notes that it is also in pole position to reap the benefit of Shantou Offshore Wind Power Industry Alliance in its push to establish and consolidate the offshore wind power industry chain for the city, establishing a new energy industry ecosystem by synergizing industry players. Built upon Shanghai Electric’s success in building the first zero-carbon factory, it will continue exploring new technologies and business models with the aim of helping China usher in the era of zero-carbon emissions.
Related Content
Microwave heating for more sustainable carbon fiber
Skeptics say it won’t work — Osaka-based Microwave Chemical Co. says it already has — and continues to advance its simulation-based technology to slash energy use and emissions in manufacturing.
Read MoreDawn Aerospace reusable rocket-powered aircraft flies twice in one day
Eighth and ninth flights of composites-intensive Mk-II Aurora reach an altitude of 63,000 feet, demonstrates same-day reusability capability for rocket-powered systems.
Read MoreParis Air Show 2023 highlights
The Paris Air Show, one of the largest aerospace trade shows in the world, returned for the first time since 2019 and proved that the global aviation industry industry is very much alive and kicking.
Read MoreRocket Lab begins installation of large AFP machine for rocket production
The 99-ton AFP machine, custom-designed and built by Electroimpact, is claimed to be the largest of its kind, expecting to save around 150,000 manufacturing hours in the Neutron rocket’s production process.
Read MoreRead Next
GE launches second production line for 107-meter wind turbine blade mold
The Cherbourg, France, facility is to ramp up production to meet offshore wind blade demand, with plans to expand the site with a hall for finishing blades.
Read MorePlant tour: Daher Shap’in TechCenter and composites production plant, Saint-Aignan-de-Grandlieu, France
Co-located R&D and production advance OOA thermosets, thermoplastics, welding, recycling and digital technologies for faster processing and certification of lighter, more sustainable composites.
Read More“Structured air” TPS safeguards composite structures
Powered by an 85% air/15% pure polyimide aerogel, Blueshift’s novel material system protects structures during transient thermal events from -200°C to beyond 2400°C for rockets, battery boxes and more.
Read More