Steelhead Composites doubles manufacturing footprint to meet demand for hydrogen storage
The new facility located in Wheatridge, Colo., will manufacture hundreds of Type IV and Type III composite-overwrapped pressure vessels (COPVs) for compressed hydrogen storage daily.
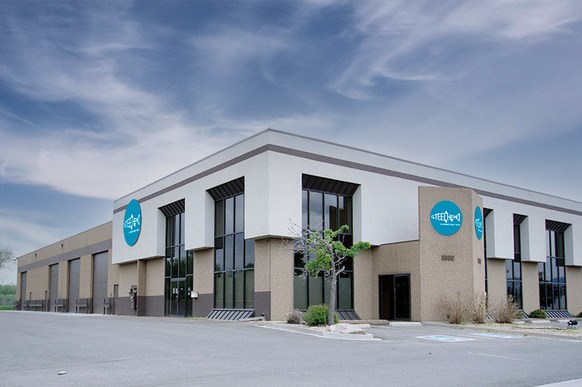
The company’s latest facility addition in Wheatridge, Colo., will double Steelhead Composites’ manufacturing capacity and is a short distance from its headquarters in Golden, Colo. Equipped with state-of-the-art machinery, the company expects to builds hundreds of composite-overwrapped pressure vessels (COPVs) daily. Photo Credit, all images: Steelhead Composites
Steelhead Composites (Golden Colo., U.S.), a provider of hydrogen storage solutions, has announced the expansion to a second facility in Wheatridge, Colo., primarily for manufacturing composite-overwrapped pressure vessels (COPVs) for compressed hydrogen storage. The facility has been approved in the company’s ISO 9001, AS9100 and ISO 14001 quality and environmental management systems
Using advanced, state-of-the-art manufacturing equipment, Steelhead reports that it has doubled annual capacity with new testing, automation, filament winding and plastic molding. The company’s in-house liner manufacturing of both polymeric-lined (Type IV) and metal-lined (Type III) vessels enables customers access to the technology to meet their permeation, robustness, cost, size and weight targets.
“There are intrinsic benefits of both metal-lined and plastic lined pressure vessels based on per-use case,” says Andrew Coors, CEO at Steelhead Composites “Steelhead is unique in having in-house expertise for manufacturing both classes of liner types.”
As hydrogen demand has skyrocketed in response to global efforts to decarbonize, Steelhead invested heavily to provide the most advanced hydrogen storage solutions available.
Steelhead Composites manufactures pressure vessels in a variety of sizes, shapes and pressures to meet customer needs. These lightweight tanks are used in a variety of industries like space, aviation, ground transportation, marine, rail, medical, storage and more. They are extremely durable and hold a variety of compressed gasses including hydrogen, natural gas, oxygen and helium.
“In the last year, we have received over 1,000 hydrogen-related storage inquiries from 36 countries because these companies need storage solutions for their zero-emission technologies,” states Marisa Veni Sundy, director of business development at Steelhead Composites. “This expansion is exciting for me, as it expands Steelhead’s role in the upcoming global energy transaction.”
Steelhead reports that it will continue to offer its pressure vessels and systems for the storage and transport of compressed natural gas (CNG) and other pressurized gases. The company serves a wide variety of industries including automotive, aerospace, aviation, marine and rail.
Related Content
-
Toray announces growth, investment in carbon fiber composite materials
As part of its 2023-2025 management strategy, Toray projects 42% growth for pressure vessels, 30% growth in carbon fiber composite materials revenue and a doubling of capital investment.
-
Cryo-compressed hydrogen, the best solution for storage and refueling stations?
Cryomotive’s CRYOGAS solution claims the highest storage density, lowest refueling cost and widest operating range without H2 losses while using one-fifth the carbon fiber required in compressed gas tanks.
-
Polar Technology develops innovative solutions for hydrogen storage
Conformable “Hydrogen in a Box” prototype for compressed gas storage has been tested to 350 and 700 bar, liquid hydrogen storage is being evaluated.