STELIA Aerospace participates in Dassault Aviation’s high-end business jet development
Ultra-long range business jet will feature four aerostructure sub-assemblies for the aircraft’s central fuselage section and pilot seats provided by STELIA, Rolls Royce engines and carbon fiber wings.
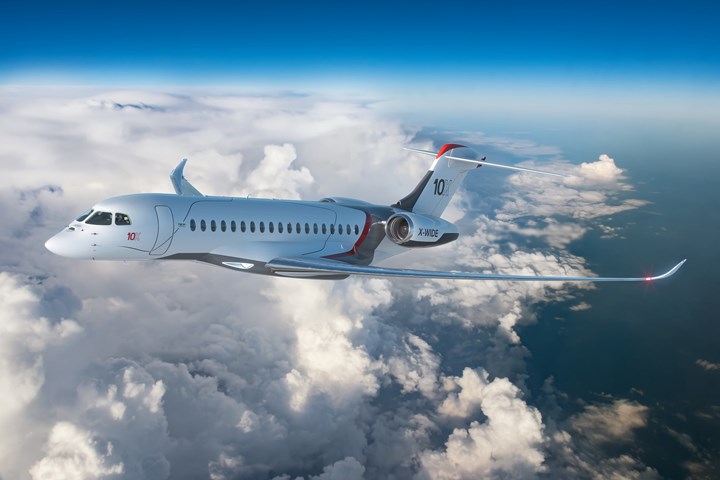
Photo Credit: Dassault Aviation
STELIA Aerospace (Toulouse, France) announced on May 6 that it is collaborating with Dassault Aviation SA (Paris, France) to develop the Falcon 10X business jet, which features a newly designed carbon fiber wing. According to STELIA Aerospace, this new contract confirms the company’s excellency and competitiveness in the field of aerostructures and pilot seats, on the high-end business aviation segment.
Specifically, the company is to focus on two projects regarding the Falcon 10X:
- Developing and providing four aerostructure sub-assemblies for the aircraft’s central fuselage section (lower shell, aft fuel tank, upper fuselage section and emergency exit door). These sub-assemblies will be developed by STELIA Aerospace’s teams following new innovative processes, based on total digital continuity, from design to mass production.
- Developing and manufacturing new generation pilot and co-pilot seats, aimed at improving the comfort and rest of the pilots.
“In the name of STELIA Aerospace and our teams, I am proud to see our company participate in Dassault Aviation’s new business jet program, the Falcon 10X,” says Cédric Gautier, CEO of STELIA Aerospace. “Both projects under our responsibility will be developed in partnership with our customer, building on our international industrial footprint, highlighting the know-how and competitiveness of our plants in France and in Tunisia. This is excellent news, especially in this time when the aeronautical industry is facing an unprecedented crisis.”
Related Content
-
Infinite Composites: Type V tanks for space, hydrogen, automotive and more
After a decade of proving its linerless, weight-saving composite tanks with NASA and more than 30 aerospace companies, this CryoSphere pioneer is scaling for growth in commercial space and sustainable transportation on Earth.
-
Combining multifunctional thermoplastic composites, additive manufacturing for next-gen airframe structures
The DOMMINIO project combines AFP with 3D printed gyroid cores, embedded SHM sensors and smart materials for induction-driven disassembly of parts at end of life.
-
Manufacturing the MFFD thermoplastic composite fuselage
Demonstrator’s upper, lower shells and assembly prove materials and new processes for lighter, cheaper and more sustainable high-rate future aircraft.