University of Limerick seeks to improve composites recycling solutions
VIBES project focuses on recycling technology maturation to develop bio-based, intrinsically recyclable materials for waste elimination, circular economy.
Share
Read Next
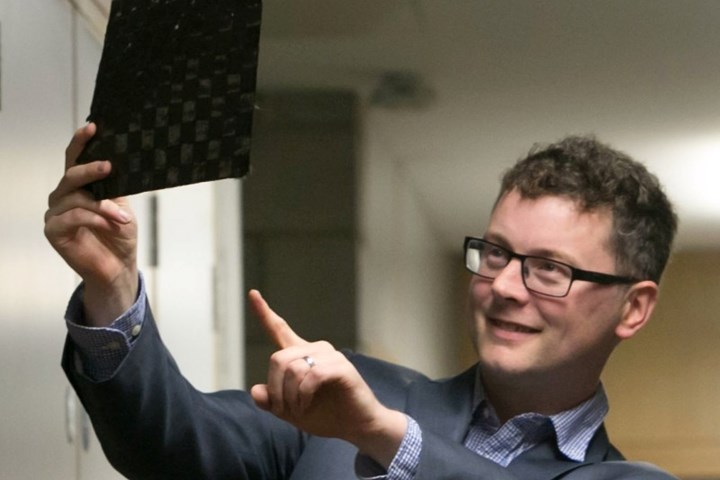
Dr. Maurice N. Collins, project lead at UL and senior lecturer at the School of Engineering, University of Limerick. Photo Credit: Univeristy of Limerick
Researchers at University of Limerick (UL, Ireland) are working on an innovative solution to improve the recyclability of composite materials used in the construction, aerospace and automotive industries through the VIBES project, a pan-European consortium comprised of a host of partners across seven EU member states, plus research and technology organizations, companies, SMEs and public bodies, of which the UL is the only university partner. Importantly, the VIBES consortium aims to achieve better results through collaborative innovation, contributing to competitiveness and helping meet social challenges.
With a budget of almost €5.3 million, the research and innovation (R&I) project seeks to improve the recyclability of composite materials through a greener, cost-efficient and non-toxic recycling technology. It involves scientists at UL’s Bernal Institute, will run a duration of 48 months (four years) and builds on work done at UL that began with LIBRE, a project that aimed to free the composite industry of its reliance on oil-based production.
“The work at University of Limerick specifically addresses the development of sustainable fibers for reinforcement of these next-generation recyclable composite materials,” explains project lead at UL and senior lecturer at the School of Engineering, Dr. Maurice N. Collins. “Researchers at UL will also be involved in the development of the recycling technology and the testing of the new composites for construction, aerospace and naval applications. These new composites could eliminate waste in end-of-life [EOL] composites and create a circular ecosystem for these materials.”
The VIBES approach focuses on the controlled separation and recovery of composite material components, by means of developing customized, bio-based bonding materials. “These new composite materials will be fully bio-based along with the recycling technology itself,” says Dr. Collins. “This will lead to reduced environmental impact by reducing the use of primary materials, harmful chemicals and landfilling.”
He adds that the resulting composite materials with intrinsic recycling properties will be validated for optimum performance and assessed on a cost ratio with applications in three high-performance industrial sectors such as the aeronautical, construction and naval industries.
The VIBES project team believe that the demonstration and training activities of VIBES will also provide new knowledge and skills to researchers, industrial professionals and students in materials science, engineering and chemical fields, to meet the rising demand for technical jobs.
VIBES is funded by Bio-Based Industries Joint Undertaking (BBI – JU) under the European Union’s Framework Program for Research and Innovation, Horizon 2020.
Related Content
-
Materials & Processes: Fabrication methods
There are numerous methods for fabricating composite components. Selection of a method for a particular part, therefore, will depend on the materials, the part design and end-use or application. Here's a guide to selection.
-
9T Labs, Purdue University to advance composites use in structural aerospace applications
Partnership defines new standard of accessibility to produce 3D-printed structural composite parts as easily as metal alternatives via Additive Fusion Technology, workflow tools.
-
Zeiss, Imperial College London summer school enhances materials, sustainability learning
Twenty-four next-generation students attended the Imperial College London this August to advance their scientific knowledge, with workshops, lectures, activities and a composites competition.