Engel launches forming and functionalization of organic sheets
Production cell demonstrates the forming and functionalization of organic sheets and unidirectional tapes in one injection molding step.
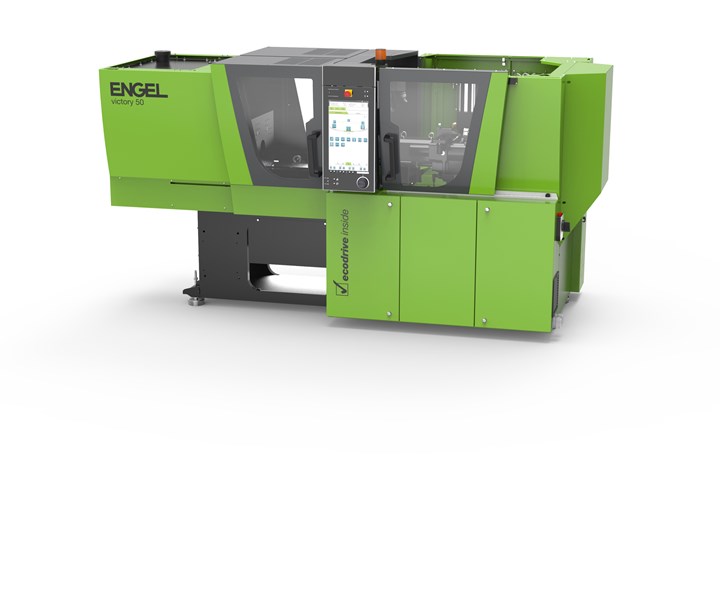
Engel victory injection molding machine. Source | Engel
Editor’s note: CompositesWorld received several new product and technology announcements ahead of JEC World 2020, which had been scheduled for March 3-5. Although that exhibition was postponed to May, CW is now publishing the announcements we received. This is one of them.
Engel (Schwertberg, Austria) is demonstrating the forming and functionalization of organic sheets and unidirectional tapes in one injection molding step. The main component of the production cell, which is producing demonstration components made of continuous fiber-reinforced polyamide (PA), is a tiebarless Engel victory 200/50 injection molding machine equipped with an Engel viper 12 linear robot for handling preforms and finished parts, and a double-sided, vertical Engel IR oven.
The composite blanks are heated in the IR oven, placed in the mold, formed in the mold, and overmolded with PA. Heating the prepregs is one of the process steps that drive the cycle time and quality in the processing of fiber-reinforced preforms with a thermoplastic matrix. The thickness defines the heat-up and cool-down time. Heating the material quickly without damaging it is important, as are short paths for transporting the heated preforms to the mold (hot handling). Engel offers IR ovens from in-house development and production in various designs – both horizontal and vertical – and places them in the production cell in the immediate vicinity of the mold. The ovens and the robots are fully integrated with the machine’s CC300 control unit and can be centrally controlled via the machine’s display.
Engel says the victory machine's biggest advantage in this application is its very fast hot handling. Barrier-free access to the mold area makes it possible to position the IR oven even closer to the mold than is possible for injection molding machines with tiebars. In this way, even very thin preforms can be processed without them cooling too much during transport between the IR oven and the mold.
The thermoplastic composite preforms that Engel is processing live at the show are prepared in the Engel Center for Lightweight Composite Technologies in Austria. In practice, the production of thermoplastic composite blanks can be placed immediately upstream of the manufacturing process and directly next to the processing machine. Engel offers fully integrated systems solutions from a single source, including the processing machine, robots and IR ovens as well as pick-and-place tape stacking units with optical image processing and consolidation units.
Composite parts created using the Engel organomelt process combine light weight with excellent crash safety capabilities. This technology, which is already in series production in the automotive industry, is suitable for organic sheets and unidirectional (UD) glass and/or carbon fiber-reinforced tapes with a thermoplastic matrix. Engel says using a purely thermoplastic material base enables particularly efficient and fully automated manufacturing processes, because reinforcement ribs or assembly elements, for example, can be injected directly after forming in the same process step. At the same time, the organomelt process makes a contribution towards sustainability. "The consistent thermoplastic approach is the precondition for developing recycling strategies for composite parts," says Christian Wolfsberger, Business Development Manager Composite Technologies at ENGEL's headquarters in Schwertberg, Austria. "Tapes make it possible to reinforce individual areas in the part in order to adapt them even more specifically to the load," Wolfsberger continues. "In the future, we will be able to combine organic sheets of different thicknesses, and also organic sheets and tapes, in order to leverage the potential for lightweight design in an even better way."
Related Content
Novel composite technology replaces welded joints in tubular structures
The Tree Composites TC-joint replaces traditional welding in jacket foundations for offshore wind turbine generator applications, advancing the world’s quest for fast, sustainable energy deployment.
Read MoreComposites end markets: Electronics (2024)
Increasingly, prototype and production-ready smart devices featuring thermoplastic composite cases and other components provide lightweight, optimized sustainable alternatives to metal.
Read MoreNatural fiber composites: Growing to fit sustainability needs
Led by global and industry-wide sustainability goals, commercial interest in flax and hemp fiber-reinforced composites grows into higher-performance, higher-volume applications.
Read MoreRecycling hydrogen tanks to produce automotive structural components
Voith Composites and partners develop recycling solutions for hydrogen storage tanks and manufacturing methods to produce automotive parts from the recycled materials.
Read MoreRead Next
“Structured air” TPS safeguards composite structures
Powered by an 85% air/15% pure polyimide aerogel, Blueshift’s novel material system protects structures during transient thermal events from -200°C to beyond 2400°C for rockets, battery boxes and more.
Read MoreDeveloping bonded composite repair for ships, offshore units
Bureau Veritas and industry partners issue guidelines and pave the way for certification via StrengthBond Offshore project.
Read MorePlant tour: Daher Shap’in TechCenter and composites production plant, Saint-Aignan-de-Grandlieu, France
Co-located R&D and production advance OOA thermosets, thermoplastics, welding, recycling and digital technologies for faster processing and certification of lighter, more sustainable composites.
Read More