Royal DSM presents glass-filled polypropylene granules for 3D printing
The glass-filled polypropylene (PP), optimized for fused granulated fabrication (FGF) is suitable for additive manufacturing of structural and demanding applications.
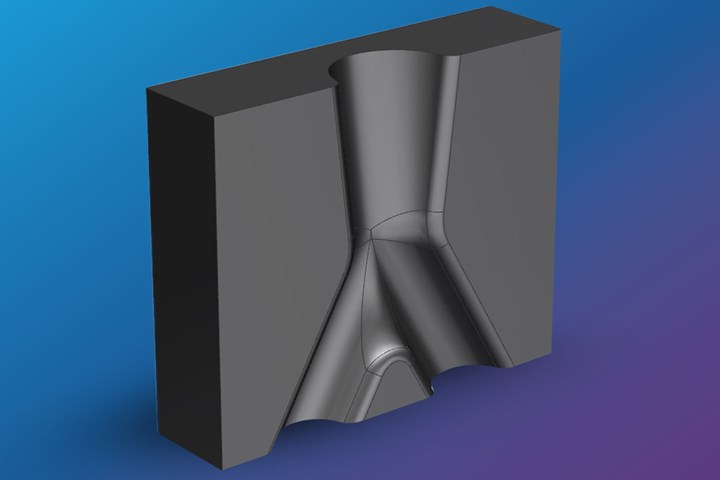
Source | Royal DSM
Royal DSM (Geleen, Netherlands) a global science-based company in nutrition, health and sustainable living, announced on August 13 new glass-filled polypropylene (PP) pellet material which has been developed specifically for 3D printing, enabling easy and consistent production of structural and demanding applications using fused granulate fabrication technology.
Widely used for its mechanical, thermal and chemical performance, DSM notes that PP is the second most frequently used polymer worldwide. Automotive, industrial or infrastructure manufacturers looking to adopt additive manufacturing technology for low volume or decentralized production — where the elimination of tools helps decrease cost — are said to desire to use the same material they are familiar with from traditional manufacturing.
To meet this growing need, DSM has unveiled its glass-filled PP for fused granulate fabrication (FGF), suitable for additive manufacturing. Arnilene AM6001 GF (G) — the (G) stands for granulates — is said to stem from the same base material used in high volume production and is optimized for FGF 3D printing. It is ideally suited for direct printing of structural, lightweight applications for automotive, infrastructure and water management, as well as tooling. DSM says the product secures all of the desirable mechanical, thermal and chemical performance of glass filled PP with the flexibility of a proven 3D process.
According to the company, the material’s low carbon footprint, due to reduced energy consumption, and its low LCA (Life Cycle Assessment), inherent to the PP’s chemistry, make it a sustainable solution.
Related Content
-
CCG FRP panels rehabilitate historic Northamption Street Bridge
High-strength, composite molded, prefabricated panels solve weight problems for the heavily-trafficked bridge, providing cantilever sidewalks for wider shared use paths.
-
Gatorbar, NEG, ExxonMobil join forces for composite rebar
ExxonMobil’s Materia Proxima polyolefin thermoset resin systems and glass fiber from NEG-US is used to produce GatorBar, an industry-leading, glass fiber-reinforced composite rebar (GFRP).
-
Swedish parking garage to incorporate decommissioned wind blades
Architect Jonas Lloyd is working with Vattenfall to design the multistory building with a wind blade façade, targeting eco-friendly buildings and creative ways to remove blades from landfills.