Cloudy skies ahead for composites
In light of the uncertainty the composites industry faces, business travel, the supply chain and the inability to develop next-generation leaders are concerns to watch for leading into 2021.
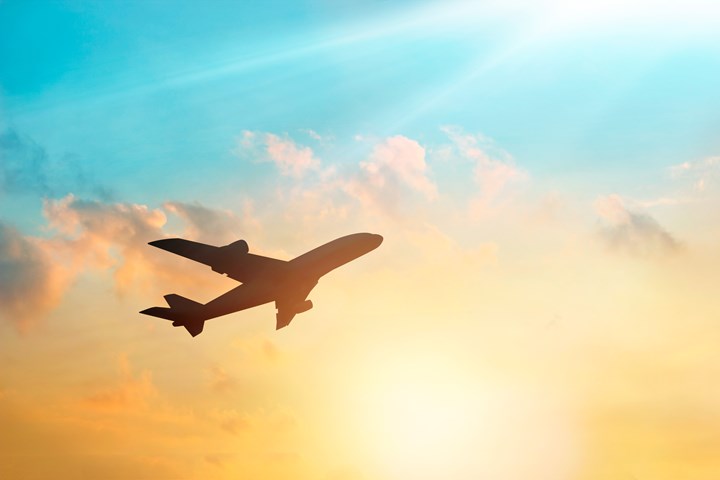
Photo Credit: Getty Images
As we conclude 2020, many will refer to it, across many facets in life and business, as “the year we lost” due to the COVID-19 pandemic. As I write this in November, there is no definitive date when life returns to “normal,” or at least how we remember it a year ago. Estimates range from April 2021 to the end of 2021, depending on a number of factors, including personal and government actions, and the widespread delivery of a vaccine. Countries in Europe are reimposing lockdowns, and it is yet to be seen what actions the U.S. will take going forward. We can all hope that we are not looking back on the “two years we lost” 12 months from now.
On several occasions these past years I have taken the opportunity in the December or January issue to prognosticate upon the year ahead, mostly in the form of outlining specific markets or technologies to watch, largely because I believed they had large potential upsides, or were poised to make significant breakthroughs. On some occasions, as I look back, I’ve even been correct — including the rise of 3D-printed tooling, increased automation, new recycling technologies and advances in Industry 4.0 for composites. As for others, including announcements of composite-intensive, single-aisle aircraft replacements and multiple OEMs following BMW’s 7-series lightweighting strategy, I missed entirely. Oh, well. Even Nostradamus didn’t have a perfect record.
Are there any bright spots shining through the pandemic? Is it all doom and gloom? Not necessarily.
This year, in light of the uncertainty we face, I’m highlighting some real concerns for 2021 and what effect a lingering pandemic could have on the composites industry. Most know me as very bullish on the composites industry, and I remain so for the long term. However, the current headwinds we face are already impacting short-term growth and may impact the medium term as well.
The first of my concerns is the uncertainty of the return of business travel in 2021. I am thinking in particular about air travel typical for trade shows and conferences, as well as discrete face-to-face selling and technical service associated with turning opportunities into sales. Will we see SAMPE in late May and JEC World in early June happen? It seems possible these events might occur right before — or at the very beginning — of a global emergence from the pandemic and the loosening of travel restrictions, including those imposed on employees of many corporations. The lack of industry trade events has hampered opportunity for suppliers to market new materials and processing solutions. As a result, users continue to favor the selection of incumbent materials and equipment. Further, until business travel returns, the aircraft manufacturing industry, a significant market for composites, will remain depressed and new opportunities for composites will be delayed.
My second concern is the duration of the pandemic and the toll it has taken on the entire value chain, resulting in decreased revenues, layoffs and delays in hiring staff. As an industry, we are well aware of the large proportion of older, experienced experts among the composites community. I personally have witnessed a number of these folks, used to executing their jobs face-to-face or side-by-side with others, finding the work-from-home experience less than fulfilling. As a result, they are taking advantage of incentives provided by employers that need to reduce headcount and riding off into the sunset or hanging out a consulting shingle. As the pandemic continues, this “talent drain” challenge will become more entrenched.
Associated with the above is a third concern: the risk of being unable to develop the next generation of composites researchers, engineers and technicians. While younger people are more adept and perhaps more comfortable with learning and working remotely, the loss of hands-on opportunities to acquire skills, especially on a manufacturing floor or in a university laboratory, is likely to impact the availability of a trained workforce when the pandemic is over and hiring picks back up. If we lose a lot of older workers, we also lose a lot of good mentors for these new leaders.
Are there any bright spots shining through the pandemic? Is it all doom and gloom? Not necessarily. Renewable energy — wind turbines in particular — appears to be relatively pandemic-resistant and still growing. Automakers are still planning to introduce electric vehicles at increasing rates, driven by falling battery costs and desire for greener transportation. Markets ideally suited for digital transformation, including development of software for modeling and simulation, and implementation of Industry 4.0 for composites, are better able to weather the current environment. In fact, with limits on shop floor access, simulating processes and part performance ahead of building prototypes is more important than ever. So is figuring out how to address my concerns.
Read Next
Composites in architecture: A hidden opportunity
Many applications in the aerospace and automotive industries apply equally to architecture, such as the use of FRP. Other opportunities for traditional composite materials may lie in seeking out creative applications.
Read MorePlant tour: Daher Shap’in TechCenter and composites production plant, Saint-Aignan-de-Grandlieu, France
Co-located R&D and production advance OOA thermosets, thermoplastics, welding, recycling and digital technologies for faster processing and certification of lighter, more sustainable composites.
Read MoreDeveloping bonded composite repair for ships, offshore units
Bureau Veritas and industry partners issue guidelines and pave the way for certification via StrengthBond Offshore project.
Read More