Plastic honeycomb goes large-scale
With RENOLIT GORCELL's broad commercialization, recent licensing by Toray, and “cooperation” with Lanxess, EconCore’s continuous thermoplastic honeycomb process gains more followers in pursuit of low-cost panels for mass markets.
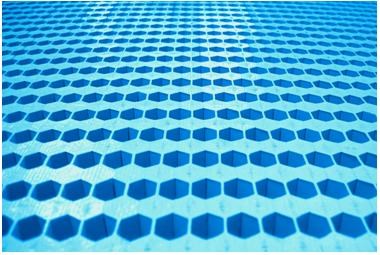
EconCore claims it provides the technology for the most economic
honeycomb sandwich panels and parts. SOURCE: EconCore
EconCore’s (Leuven, Belgium) continuous thermoplastic honeycomb production process called ThermHex has been around for more than a decade. Developed and patented by Belgium’s largest university, KU Leuven (Leuven, Belgium), ThermHex technology enables cost-efficient products using a wide range of polymers including polypropylene (PP), polyester (PET), polyvinyl chloride (PVC), polyamide (PA), acrylonitrile butadiene styrene (ABS), nylon, polyphenylene sulfide (PPS) and many others. The honeycombs can be made directly from an extruder or roll of material with a variety of cell sizes, densities and thicknesses. The resulting honeycombs have closed skin strips, creating more surface area for excellent bonding of skins onto the core. In fact, the process easily allows inline lamination of faceskins and panel post-processing, furthering potential cost reduction.
![]() ![]() |
Automotive door panel made of ThermHex honeycomb
with natural fiber / PP composite skins. SOURCE: EconCore
CW reported in April that Toray (Tokyo, Japan) and Itochu (Tokyo, Japan) have licensed the ThermHex technology from EconCore. Toray says it will combine ThermHex with its own core and sandwich panel materials technology called NANOALLOY to offer what is described as extraordinary impact absorption. (See April news item.)
EconCore and LANXESS (Cologne, Germany) have also announced a “cooperation” agreement to manufacture new honeycomb cores from various polymers including Durethan polyamides using the ThermHex continuous process and to combine these with Tepex continuous fiber-reinforced thermoplastic composites from LANXESS subsidiary Bond-Laminates for use in high-performance composites applications. Hartwig Meier, head of product and applications development in the LANXESS High Performance Materials business unit, detailed, “We expect the thermoplastic sandwich structures, with their high-quality mechanical properties, to be suitable for replacing metal in many areas and thus reducing weight, for instance in motor vehicles, but also in the building and transportation industries, boat and furniture building and motorhome manufacturing.”
![]() ![]() |
Lanxess PA core with TEPEX skins (left) and PP core with
natural fiber skins (right). SOURCE: EconCore.
Another licensee, Renolit GOR (Buriasco, Italy), exhibited its RENOLIT GORCELL honeycomb products at JEC 2014 (March 11-13, Paris, France) sold into building, furniture and automotive end-uses. According to Axel Kulke, sales director for Renolit Composites, the company has been selling wood plastic composite (WPC) sheets for more than 42 years. “Recently the automotive and building markets have requested development of a material/panel which has still the same characteristics as current WPC but with increased stability and stiffness without adding much weight.” Kulke says Renolit decided to invest in EconCore’s honeycomb technology because it enabled automated production of honeycomb “and then thermo-laminating our WPC sheets on both sides as skins for markets like automotive, furniture, flight cases, van superstructures and floors, marine, facades, booth equipment etc.” Kulke says the RENOLIT GORCELL process is very economical and gentle on energy and other resources. The product won the first prize WPC Innovation Award at the 5th German WPC-Conference (Dec. 10-11, 2013 Cologne, Germany).
Tomasz Czarnecki, technology manager at EconCore, says that Röplast (Eskişehir, Turkey) has also licensed the technology, is installing equipment now and will produce panel products under the “Hexapan” brand. “We are looking into creating similar license cases in the U.S.,” he says, “so the momentum is indeed increasing.”
EconCore supports licensees in their development of applications and integration of the ThermHex technology into their production. It continues to explore new material combinations such as thermoplastic cores with aluminum or steel faceskins targeted for interior and exterior cladding, visual communication boards and transportation applications, and PP honeycomb with natural fiber composite skins for automotive interiors. Additional licensees include: Coroplast (Chicago, Ill., USA), Gifu Plastics (Gifu, Japan), Karton (Pordenone, Italy) and ThermHex Waben (Halle, Germany). EconCore has also signed a license agreement with a world leading steel maker to enable continuous production of super strong honeycomb panels with steel facings. The name of the licensee will be announced soon.
Related Content
Park Aerospace launches aerospace, MRO structural film adhesive
Aeroadhere FAE-350-1 is a curing epoxy formulation designed for composite, metal, honeycomb and hybrid applications.
Read MoreResins, additives, adhesives and 3D printing solutions
CAMX 2023: Arkema’s broad portfolio of products for composites fabricators aim to enhance performance, durability and sustainability.
Read MorePittsburgh engineers receive $259K DARPA award for mussel-inspired underwater adhesion
The proposed META GLUE takes inspiration from hydrogels, liquid crystal elastomers and mussels’ natural bioadhesives to develop highly architected synthetic systems.
Read MoreHenkel receives Airbus qualification for European aerospace manufacturing facility
The adhesive company’s Montornès, Spain, plant has been approved as a standard and raw materials supplier for various Airbus platforms, adding to its work in lightweighting, fuel efficiency and automation.
Read MoreRead Next
All-recycled, needle-punched nonwoven CFRP slashes carbon footprint of Formula 2 seat
Dallara and Tenowo collaborate to produce a race-ready Formula 2 seat using recycled carbon fiber, reducing CO2 emissions by 97.5% compared to virgin materials.
Read MoreVIDEO: High-volume processing for fiberglass components
Cannon Ergos, a company specializing in high-ton presses and equipment for composites fabrication and plastics processing, displayed automotive and industrial components at CAMX 2024.
Read MoreDeveloping bonded composite repair for ships, offshore units
Bureau Veritas and industry partners issue guidelines and pave the way for certification via StrengthBond Offshore project.
Read More