Ready or not, here come flying taxis and hydrogen
Composites are ripe for entry into a variety of markets, but advanced air mobility and hydrogen storage are poised to put unprecedented pressure on the supply chain.
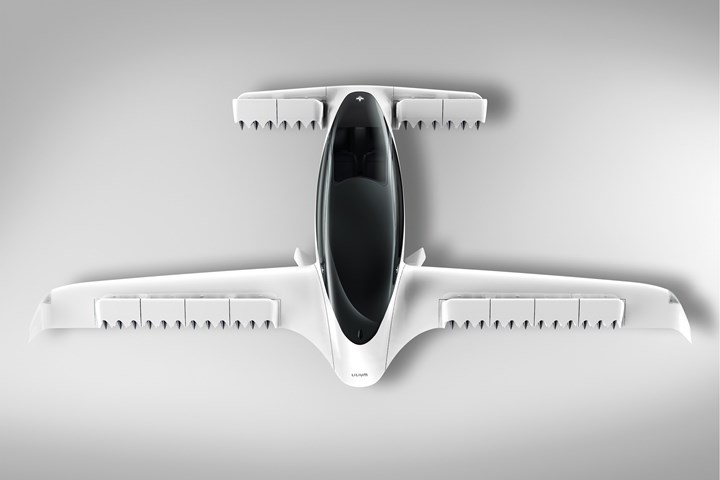
Lilium Jet. Photo Credit: Lilium
Material suppliers and fabricators in the composites industry, like most businesses, prefer the steady stream of long, consistent contracts that deliver dependable and reliable revenue. The global coronavirus pandemic notwithstanding, this steadiness of business is one of the great benefits conveyed to the composites industry by the commercial aerospace end market. Commercial aircraft, by virtue of the certification environment in which they operate, are supplied by material and manufacturing contracts that remain, for the most part, fixed for the life of the aircraft program, which can span decades.
Toray (Tokyo, Japan) and Hexcel (Stamford, Conn., U.S.), for example, are the primary carbon fiber suppliers to the Boeing 787 and the Airbus A350 respectively, and have enjoyed the steadiness of revenue that those aircraft programs have provided. Multiply the benefits of that relationship across all vendors in those aircraft supply chains and it’s not difficult to understand why the composites industry pays such close attention to the commercial aerospace market.
Commercial aerospace, however, is the exception that proves the rule in the composites industry. Most of the end markets that consume composite materials do not do so in the same high-performance/high-regulation environment. Automotive and wind come somewhat close, but the fixation in those markets on cost and efficiency do not favor long-term material and manufacturing contracts.
It’s not a matter of if but whether or not the composites supply chain is ready to meet the challenge.
So, if you are a composites fabricator, even if some of your business is in the aerospace industry, you likely have the dreaded revenue peaks and valleys that plague many operations. And, like many businesses, you probably have tried to diversify your customer base to fill in those valleys. One way to do this is to attempt to meet a need in an emerging market, or a market that has been underserved by the composites industry.
The easiest path to expanded composites use typically comes in two forms: new markets where there is minimal history of non-composites use, or established but relatively small markets where composites already have a presence. There are, right now, two markets that represent each model: advanced air mobility (AAM) and hydrogen storage.
AAM is the new market, and while in the very early stages of development as reported by CW, it’s definitely coming. AAM aircraft seat two to six people, including a pilot, are fully electric and designed to transport passengers taxi-like in and around major metropolitan areas, bypassing time-consuming ground traffic. AAM aircraft — manufactured by companies like Joby Aviation (Santa Cruz, Calif., U.S.), Lilium (Munich, Germany), Wisk (Mountain View, Calif., U.S.) and a host of others — are necessarily composites intensive to maximize range and cargo capacity, but will be manufactured at a rate (thousands of shipsets per year) and quality standard combination heretofore not seen in the composites industry. There is tremendous opportunity in AAM, but also significant challenge to ramp up composites manufacturing automation and efficiency to meet the rate/quality standards.
Alternately, hydrogen storage is the established market that is on the verge of major expansion. If you have paid even a modicum of attention during the last year, you know that hydrogen has vaulted near the top of the non-petroleum energy source list, joining the likes of wind, solar and hydro energy. Programs that use hydrogen to power long-haul trucks, buses, trains, cars and aircraft are advancing rapidly throughout the world. There is an all-of-the-above mentality governing material selection for hydrogen, and carbon fiber is a prime candidate for Type IV pressure vessels in this market.
There are, however, with any expanded use of composites, a fair number of be-careful-what-you-wish-for warnings. As eager as we are to see composite materials move into new markets and applications, the truth is that this industry is not yet so evolved that the supply chain can quickly and easily flex to new opportunities. And sometimes those opportunities, although promising, are fleeting. Indeed, it’s difficult to look at what’s happening with hydrogen today and not wonder if it’s a real and sustainable expansion. Carbon fiber lines alone take 24 months to build, and typically require substantial evidence that there is a market for the material. Is it fair to expect a carbon fiber manufacturer to eagerly expand its production in such an environment?
Probably not, but like it or not, the markets served by the composites industry increasingly expect such flexibility, and if we want composites to be a first choice material, that adaptability must be developed sooner than later. It’s not a matter of if AAM and hydrogen storage will evolve into full-blown and prosperous end markets, but whether or not the composites supply chain is ready to meet the challenge and take advantage of the opportunity.
Related Content
Combining multifunctional thermoplastic composites, additive manufacturing for next-gen airframe structures
The DOMMINIO project combines AFP with 3D printed gyroid cores, embedded SHM sensors and smart materials for induction-driven disassembly of parts at end of life.
Read MorePlant tour: Middle River Aerostructure Systems, Baltimore, Md., U.S.
The historic Martin Aircraft factory is advancing digitized automation for more sustainable production of composite aerostructures.
Read MoreComposites manufacturing for general aviation aircraft
General aviation, certified and experimental, has increasingly embraced composites over the decades, a path further driven by leveraged innovation in materials and processes and the evolving AAM market.
Read MorePlant tour: Spirit AeroSystems, Belfast, Northern Ireland, U.K.
Purpose-built facility employs resin transfer infusion (RTI) and assembly technology to manufacture today’s composite A220 wings, and prepares for future new programs and production ramp-ups.
Read MoreRead Next
The hydrogen economy: Hope or hype?
Green hydrogen technologies have become the forefront for the global zero-carbon energy landscape. Now, it may be cost that ultimately determines its expansion opportunities into the composites industry.
Read MorePlant tour: Daher Shap’in TechCenter and composites production plant, Saint-Aignan-de-Grandlieu, France
Co-located R&D and production advance OOA thermosets, thermoplastics, welding, recycling and digital technologies for faster processing and certification of lighter, more sustainable composites.
Read MoreAll-recycled, needle-punched nonwoven CFRP slashes carbon footprint of Formula 2 seat
Dallara and Tenowo collaborate to produce a race-ready Formula 2 seat using recycled carbon fiber, reducing CO2 emissions by 97.5% compared to virgin materials.
Read More