Antich and Sons develop composite yarn-spinning technique for 3D-woven preform production
Culmination of a three-year project with AMRC which focused on creating stabilized, near-net shape preforms of variable thickness with efficient material use for aerospace and automotive.
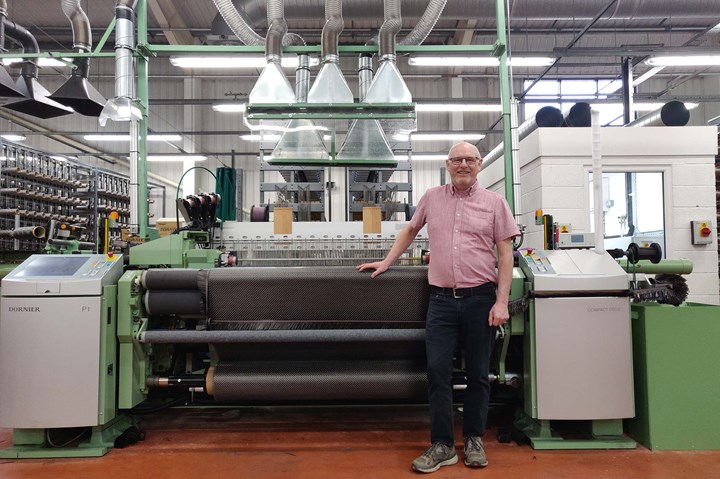
Martin Wood, weaving director at Antich and Sons, pictured with one of the single rapier weaving looms used to create 3D-woven multilayer textiles. Martin is arguably one of the most experienced weaving experts in the country having spent his entire career working on the technical side of weaving. All photo credit: Antich & Sons, AMRC.
Fabric producer Antich and Sons (Huddersfield, U.K.) has achieved a step change in its manufacturing capability to produce finished 3D multilayer woven preforms for advanced composites used in aerospace and automotive through a pioneering project with the University of Sheffield Advanced Manufacturing Research Centre (AMRC, Catcliffe, U.K.)
Antich and Sons’ advanced capability is the culmination of FABFORM, a three-year project undertaken with the AMRC and funded by Innovate UK, which focused on developing the additional methods needed to create stabilized, near-net shape preforms of variable thickness. These preforms will reportedly enable efficient use of material within a component, ensure the correct size and shape to drop into molds used for injection of composite matrix resin, as well as facilitate an easier and more robust handling and transport.
The company’s head of research and development, Andy Smith, says developments in the stabilizing and trimming of 3D-woven carbon fiber preforms with uniform and variable thicknesses is a significant achievement for the Huddersfield-based company, moving it beyond the current state-of-the-art manufacturing capabilities.

The demonstrator part produced by Antich and Sons which represents a step change in its manufacturing capability.
“The variable thickness, stabilization and trimming methods developed for 3D-woven materials in FABFORM allow a significant step up the value chain,” says Smith. “It takes Antich from a weaver of fabric to a manufacturer of advanced composite preforms ready for the next step in the manufacturing process.”
Smith notes that development of key processes necessary to transform 3D-woven fabrics into ‘mold ready’ preforms is still immature in the U.K. supply chain. He says the new developments by Antich and Sons bring great value to the market by advancing manufacturing technologies, improving product performance and streamlining production capabilities.
“In the past, 3D-woven preforms were hard work to prepare for molding operations and were also liable to deterioration when handled and cut,” says Smith. “Therefore, we felt it was crucial that, as a weaver, we developed the technology both during and post-weaving to supply finished, stable preforms which can be easily utilized by end users.
“The ability to access the world-class facilities at the University of Sheffield AMRC was a major help in taking a scientific approach to assessing, down-selecting and testing the right technologies as well as developing the processes on industrial scale, high-tech equipment.”
Chris McHugh, dry fiber development manager at the AMRC Composite Centre, says the developments achieved through FABFORM support the creation of more competitive products that are lighter, stiffer and stronger, as well as helping diversify income streams, creating new jobs and increasing the skills base in composites.
He adds: “The collaboration between the AMRC and Antich and Sons has utilized the combined advanced technologies and experience available to advance 3D weaving preforming capabilities for U.K. manufacturing. The outputs from the project have the potential to generate significant new business and strong exports for the U.K., in cross sector high-value manufacturing applications including the strong export markets in automotive and aerospace.”
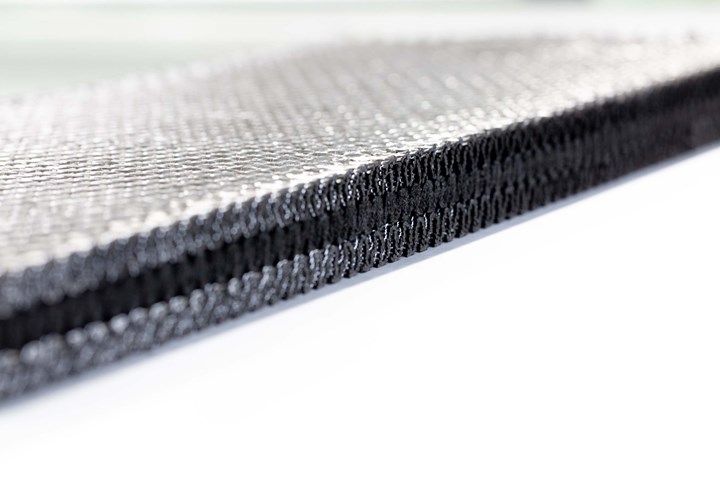
Smith says FABFORM has been “an excellent first step” in incorporating key technologies such as thickness tapering, stabilization and edge trimming that mechanically convert 3D fabric into a useable preform for a composite molding operation.
He says the know-how of this project has been developed by investigating various preform stabilization techniques and quantitatively assessing their performance through multiple test methods such as edge fraying tests and picture frame shear tests, to name a few. This was followed by the comparison of a wide range of trimming methods of the preforms including laser, water jet cutting and ultrasonic methods.
“The capability to supply advanced and ready-to-go preforms opens up new avenues for the development of alternative structural and complex materials on the U.K. market, enabling the creation of more competitive products,” Smith adds. “Future opportunities in markets such as renewables (wind turbine blades), rail (body structure), industrial processing and defense will provide long-term benefits for the wider U.K. composite sector.”
With more than ten years’ expertise in composite research and development, in areas like polymer matrix composites (PMC) and aluminium matrix composites (AMC), Antich and Sons says it continues to drive the business forward into new applications for its weaving technology.
The company has acquired a single rapier 3D-weaving machine from Lindauer Dornier GmbH (Lindau, Germany), including a Horizontal Take-Off (HTO) platform which is said to be the first of its kind in the U.K. This HTO platform enables a continuous draw of fabric off the machine in a straight horizontal configuration, instead of around a roller, which is key to avoid distortion with thick fabrics, and forms the basis for layer separation techniques that facilitate variable thickness, the company says. Capability for resin transfer molding (RTM) of prototypes has also been added to speed up development cycles.
Antich and Sons intend to exhibit at Advanced Engineering and JEC World when the conferences return.
Related Content
Carbon fiber, bionic design achieve peak performance in race-ready production vehicle
Porsche worked with Action Composites to design and manufacture an innovative carbon fiber safety cage option to lightweight one of its series race vehicles, built in a one-shot compression molding process.
Read MoreTU Munich develops cuboidal conformable tanks using carbon fiber composites for increased hydrogen storage
Flat tank enabling standard platform for BEV and FCEV uses thermoplastic and thermoset composites, overwrapped skeleton design in pursuit of 25% more H2 storage.
Read MorePlant tour: Joby Aviation, Marina, Calif., U.S.
As the advanced air mobility market begins to take shape, market leader Joby Aviation works to industrialize composites manufacturing for its first-generation, composites-intensive, all-electric air taxi.
Read MorePlant tour: Albany Engineered Composites, Rochester, N.H., U.S.
Efficient, high-quality, well-controlled composites manufacturing at volume is the mantra for this 3D weaving specialist.
Read MoreRead Next
All-recycled, needle-punched nonwoven CFRP slashes carbon footprint of Formula 2 seat
Dallara and Tenowo collaborate to produce a race-ready Formula 2 seat using recycled carbon fiber, reducing CO2 emissions by 97.5% compared to virgin materials.
Read MoreVIDEO: High-volume processing for fiberglass components
Cannon Ergos, a company specializing in high-ton presses and equipment for composites fabrication and plastics processing, displayed automotive and industrial components at CAMX 2024.
Read MoreDeveloping bonded composite repair for ships, offshore units
Bureau Veritas and industry partners issue guidelines and pave the way for certification via StrengthBond Offshore project.
Read More