BBG GmbH becomes international system partner for automated production and materials processing
Full-range supplier manufactures supplies for fully automated production modules, molds for composite processes and produces composite components for lightweight construction.
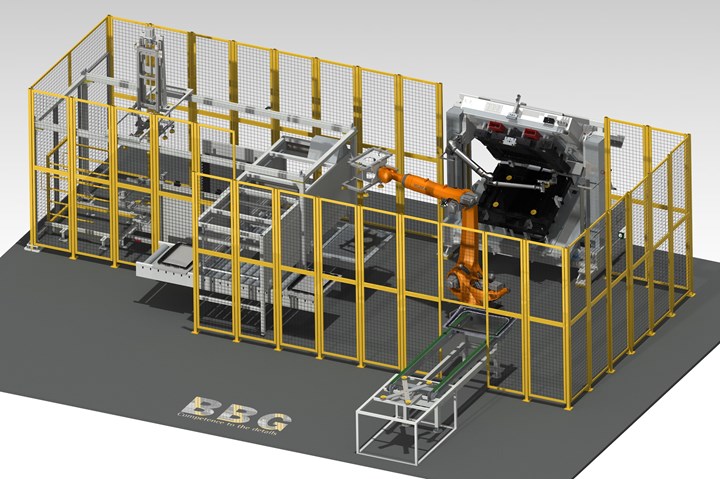
BBG Group is transforming itself from a mold, machinery and plant manufacturer to an international system partner. Photo Credit, all images: BBG.
BBG Gmbh & Co. KG (Mindelheim, Germany) announced on Oct. 28 that it is transforming itself from a mold, machinery and plant manufacturer to an international system partner for polyurethane processing, including glass encapsulation and the production of molded composite components. As a full-range supplier, the manufacturer supplies all components for fully automated, continuously documented production that can be tracked over the entire lifetime of the components. As a general contractor, BBG also retrofits components, or integrates existing equipment into end-to-end production lines. BBG and its subsidiaries target markets in Europe, all NAFTA countries and Asia, China in particular.
As a system partner, the family-owned company also offers to perform all required working steps from a single source. In addition to project planning and plant design, this covers the selection of coordinated modules, including interface coordination and their integration into a central control system. The installation of all components, their commissioning and operator training are also part of the service.
BBG says the modules used cover the work steps for fully automated production lines. They start at the provisioning of materials and the loading of the system, and include the actual manufacturing process and the removal of the produced components right through to visual inspection, post-processing and packaging.
In addition to various individual components — the molds in particular — the mold carrier and press systems are designed and manufactured in the company’s own production facilities. BBG sources other modules from long-standing partners, adapts them to customers’ requirements and integrates them into the production lines.
Further, BBG notes that the degree of automation of a production process can be freely determined, as can the scope of the documentation of material and process data. These are stored centrally and can be retrieved at any time.
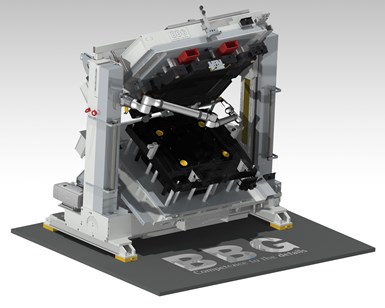
Two robot-equipped automation cells are new, which apply release agents to mold surfaces (pictured) and primer or paint to components in an unmanned process.
BBG’s novel solutions consist of two robot-equipped automation cells, which apply primer or paint to components and release agent to mold surfaces in an unmanned process. BBG presented the concept for automatic release agent application using a prototype at its Innovation Day in 2019.
The automation cells reliably improve the quality and process safety of the operations, according to the company. They also relieve employees of work that is physically demanding and sometimes hazardous to their health. The two modules were used for the first time by a North American supplier of passenger car and commercial vehicle parts.
BBG GmbH & Co. KG is an international system partner for the plastics processing industry. In addition to end-to-end production lines, BBG designs, develops and manufactures molds for processing polyurethane, PVC, TPE and other elastomers, as well as a wide range of composite materials. This includes production processes such as PUR composite spray molding (PUR-CSM, long fiber injection (LFI) and resin transfer molding (RTM) for materials such as sheet molding compound (SMC) or glass mat-reinforced thermoplastics (GMT). The company also focuses on solutions for lightweight construction, the processing of composites and the production of fiber-reinforced composite components in a large number of industries. Since 2020, the company has also been developing and manufacturing packaging machines for pharmaceutical products and food supplements.
Related Content
Broetje-Automation demonstrates rCF placement via AFP
Through the ScrapSeRO project, the system integrator and machine builder successfully processed recycled composites, in addition to more traditional materials, via its highly flexible Staxx One system.
Read MoreAirborne delivers composite upper stage tank for EU ENVOL project
Nine-member consortium targets development of low-cost, green vertical orbital launcher with manufacture of an ultra-lightweight composite tank design in an automated manufacturing environment.
Read MoreHow AI is improving composites operations and factory sustainability
Workforce pain points and various logistical challenges are putting operations resilience and flexibility to the test, but Industry 4.0 advancements could be the key to composites manufacturers’ transformation.
Read MoreManufacturing the MFFD thermoplastic composite fuselage
Demonstrator’s upper, lower shells and assembly prove materials and new processes for lighter, cheaper and more sustainable high-rate future aircraft.
Read MoreRead Next
HP-RTM as a means to reduce hydrogen tank packaging space and cost
BBG Gmbh & Co. KG has developed molds for producers of type IV CFRP tanks, integrating automation and sensors for faster, cheaper production of adjustable-length hydrogen storage cylinders.
Read MoreVIDEO: High-volume processing for fiberglass components
Cannon Ergos, a company specializing in high-ton presses and equipment for composites fabrication and plastics processing, displayed automotive and industrial components at CAMX 2024.
Read MoreAll-recycled, needle-punched nonwoven CFRP slashes carbon footprint of Formula 2 seat
Dallara and Tenowo collaborate to produce a race-ready Formula 2 seat using recycled carbon fiber, reducing CO2 emissions by 97.5% compared to virgin materials.
Read More