Boston Materials closes $8 million Series A funding to advance z-axis carbon fiber materials
Funds expect to fuel rapid expansion of the company’s z-axis products into market applications such as electric vehicles, aerospace and consumer electronics.
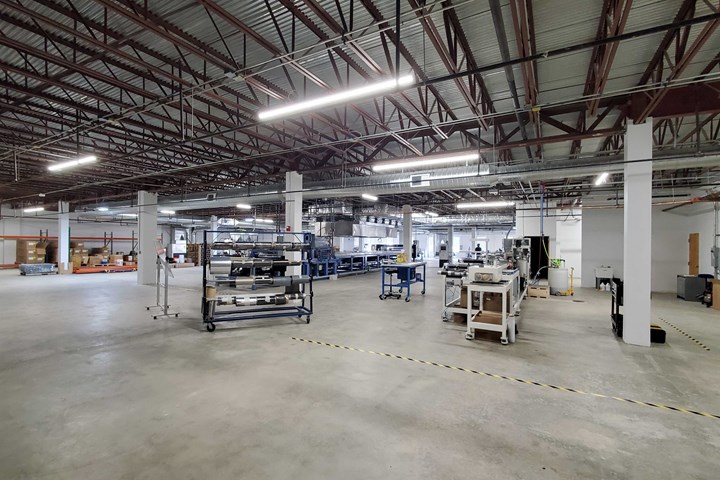
Boston Materials’ 37,000-square-foot manufacturing facility in Billerica, Massachusetts. Photo Credit: Boston Materials
Boston Materials (Billerica, Mass., U.S.) a manufacturer of advanced lightweight materials that deliver increased performance and circular solutions using z-axis carbon fiber technology, announced on May 20 the closing of an $8 million financing led by AccelR8 and Valo Ventures. This funding accelerates the company’s expansion into new electric vehicles (EVs), aerospace, electronics and consumer applications. Clean Energy Ventures, a previous backer, also participated in the round.
“Boston Materials is doing something others simply can’t. They’re improving the quality of advanced lightweight materials with a truly scalable z-axis carbon fiber technology that uses 100% reclaimed feedstocks,” says Dwight Poler, CEO of AccelR8. “Boston Materials is one of the only solutions we’ve seen that can integrate sustainable materials and actually improve performance and breadth of application simultaneously.”
Boston Materials uses a patented roll-to-roll magnetic alignment process that orients reclaimed carbon fibers vertically to manufacture composite film and sheet products, called ZRT. This process is said to introduce new z-axis thermal and electrical conductivity, stiffness and durability benefits to existing composite materials. Ultimately, the company says its products provide designers and manufacturers with multiple benefits over metals and nanomaterials, including lighter weight, lower embodied carbon footprint and lower production costs.
“Boston Materials creates a clear ROI for customers by delivering products with superior performance at a lower cost. The team has thoughtfully designed their products to augment existing supply chains, helping pave the way for their z-axis carbon fiber to become a breakthrough metal replacement in the next generation of high-volume consumer and industrial products,” says Subodh Gupta, principal at Valo Ventures. “At the same time, Boston Materials’ products deliver a strong return for the environment by reducing the reliance on virgin materials, advancing the circular economy and continuing the proliferation of composites to decarbonize industries."
Earlier in 2021, Boston Materials commissioned a 60-inch-wide commercial production line capable of producing 800,000 square meters of z-axis carbon fiber materials per year. The company plans to triple the production capacity over the next two years. The production capacity has been installed in a 37,000 square-foot manufacturing facility located in Billerica, Mass., along with fully-automated equipment for quality control and traceability. Boston Materials is dedicated to expanding its manufacturing operations in the Boston area by cultivating a robust team of manufacturing personnel from across all industries and training them as technicians for the production of advanced composite materials.
“The global supply chain creates nearly three billion dollars worth of carbon fiber scrap every year, even without the end-of-life [EOL] scrap from large structures like airplanes and wind turbine blades. This is a massive environmental problem and economic opportunity for the composites industry,” says Anvesh Gurijala, co-founder and CEO of Boston Materials. “Our z-axis carbon fiber products provide a high-performance outlet for the growing amount of available reclaimed carbon fiber, enabling an important shift in the composites and lightweight materials industries. We’ve now collected a thoughtful, influential group of investors who believe in us and we are eager to leverage their collective resources and expertise to quickly expand our presence in new markets.”
The new funds will be used to continue to expand the applications of z-axis carbon fiber products and hire additional technical sales, application development specialists and manufacturing technicians to rapidly accelerate the growth of the company.
Read Next
Developing bonded composite repair for ships, offshore units
Bureau Veritas and industry partners issue guidelines and pave the way for certification via StrengthBond Offshore project.
Read More“Structured air” TPS safeguards composite structures
Powered by an 85% air/15% pure polyimide aerogel, Blueshift’s novel material system protects structures during transient thermal events from -200°C to beyond 2400°C for rockets, battery boxes and more.
Read MorePlant tour: Daher Shap’in TechCenter and composites production plant, Saint-Aignan-de-Grandlieu, France
Co-located R&D and production advance OOA thermosets, thermoplastics, welding, recycling and digital technologies for faster processing and certification of lighter, more sustainable composites.
Read More