Clean Sky 2 DEFLECT project develops multifunctional composite panels for electronics enclosures
Four panels integrating mechanical and electrical elements such as connectors, wires and busbars into aerostructures offer solutions for greener aircraft.
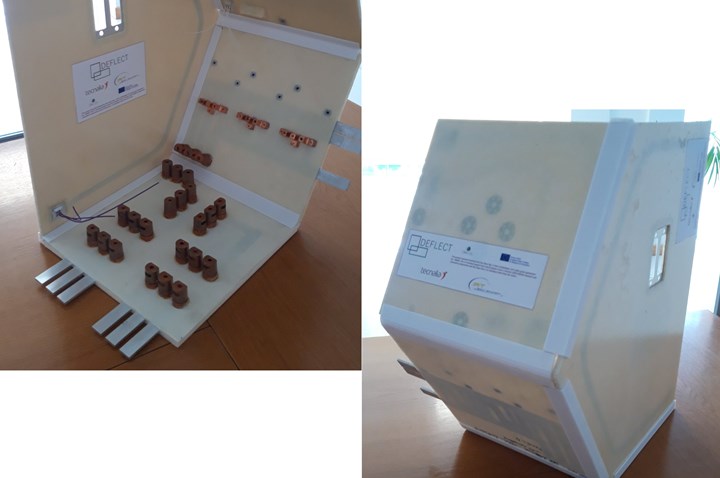
Photo Credit: Clean Sky 2 DEFLECT project
DEFLECT is a Clean Sky 2 project (2018-2020) with an EU budget of €599,600 aimed at developing multifunctional composites for electrical cabinets housing onboard electrical and avionics equipment. The goal is to produce technology that enables the efficient integration of mechanical and electrical elements such as connectors, wires and busbars into composite laminates, either internally or integrated into the surface.
DEFLECT will demonstrate that lightweight composite materials are an affordable alternative for the manufacturing of electrical cabinets. Studies performed in this area indicate a potential to replace current aluminum electronics housings with lightweight composites. Such structures built using modern composites technology are able to provide important weight savings. In addition, composites can be uniquely multifunctional, allowing additional materials/elements to be embedded inside the laminate during manufacture to provide functions beyond the structural role itself. This reduces mass and complexity of the overall system.
Using a simple process, the DEFLECT project developed four multifunctional fire-proof panels, which can be used for building aircraft electrical cabinets for power distribution. Two different alternatives with high embedding capabilities have been developed:
- A light, cost-effective and fire-proof laminate with high capability for embedding electric wires, fiber optics, electrical connectors and inserts.
- A one-shot sandwich panel with reinforced skins specifically for embedding busbars.
These panels will result in an overall mass saving of 5-10% (note the original goal was stated as 30%), in addition to reducing assembly costs and achieving a 10% saving in volume. Although these solutions are not lighter than current state-of-the-art Nomex honeycomb-cored panels, they are much more damage tolerant and have a higher embedding ability. Considering the mass of additional elements such as screws and attachments required in traditional solutions, the approaches developed in DEFLECT are very competitive. They also prevent the need for hazardous surface treatments such as chromic acid anodizing and alodine, which use the harmful element hexavalent chromium (Cr6+). In addition, these multifunctional composite solutions may reduce the length of wiring and its insulation required, reducing the mass of the electrical harnesses.
DEFLECT project partners comprise topic manager Safran Electrical and Power (Blagnac, France), TECNALIA (San Sebastián, Spain) and IRT Saint Exupéry (Toulouse, France). Their challenges have included optimizing manufacturing parameters to ensure that the initiative was in line with REACH and fire regulations. Next steps include the development and complete validation of a functional prototype. Meanwhile, the partners are investigating the possibility of patents for various developments.
Related Content
-
The potential for thermoplastic composite nacelles
Collins Aerospace draws on global team, decades of experience to demonstrate large, curved AFP and welded structures for the next generation of aircraft.
-
Plant tour: Albany Engineered Composites, Rochester, N.H., U.S.
Efficient, high-quality, well-controlled composites manufacturing at volume is the mantra for this 3D weaving specialist.
-
Infinite Composites: Type V tanks for space, hydrogen, automotive and more
After a decade of proving its linerless, weight-saving composite tanks with NASA and more than 30 aerospace companies, this CryoSphere pioneer is scaling for growth in commercial space and sustainable transportation on Earth.