Clean Sky 2’s PASSARO project targets one-shot OOA composite cockpit
Synergies with MOSHO project for NDT, repair and also developing cobots for 70% cut in cycle time.
The PASSARO (caPAbilities for innovative Structural and functional testing of AeROstructures) project aims to develop new multifunctional materials — integrating noise insulation and high energy impact resistance — and inspection solutions for new composite cockpit manufactured in one shot and complemented with out of autoclave (OOA) technologies such as thermoplastic composite in-situ consolidation and liquid resin infusion. This composite cockpit was developed by Airbus Defence and Space (Madrid, Spain) during Clean Sky 1, based on the C295 aircraft. The project is also targeting the automatization of manufacturing processes as well as new testing approaches based on Industry 4.0 concepts and developing ergonomic advanced concepts promoting the pilot comfort and improved human machine interface.
The PASSARO project, part of Clean Sky 2’s Airframe platform, started in July 2016 with a total duration of 48 months. It comprises eleven partners from Portugal and Spain working in close collaboration with Airbus Defence and Space.
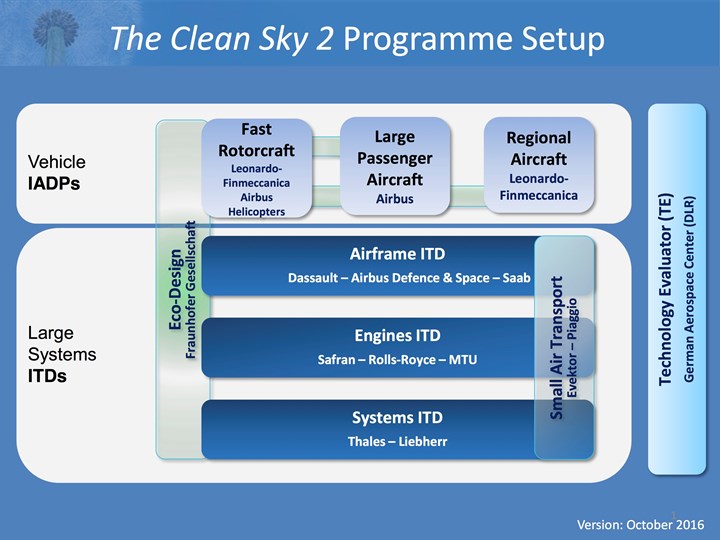
Synergies with Portugal regional MOSHO project
Many Clean Sky 2 (CS2) projects share synergies with regional EU member initiatives (e.g., CORAC in France). The PASSARO project has promoted complementary activities with Portuguese national R&D initiatives. The MOSHO project (Advanced solutions for impact materials, repair of composite aero-structures and their monitoring) complements PASSARO activities in which some of the partners are involved and is supported by ADS (Airbus Defence and Space) as the Clean Sky 2 coordinator for the Airframe ITD. The project will develop and integrate advanced solutions for the repair of composite aerostructures.
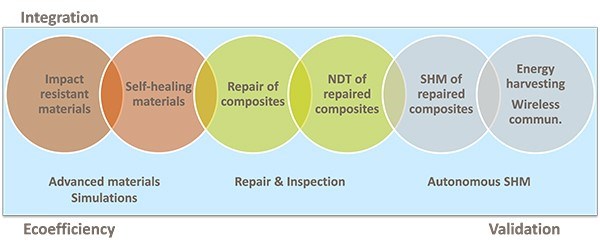
Figure 3: MOSHO project technical scope SOURCE: https://www.cleansky.eu/commissioner-moedas-meets-passaro-at-isq
PASSARO collaborative robots cut hand layup cycle time by up to 70%
As part of the PASSARO project’s objectives to research and develop how to employ collaborative robots in composites manufacturing, the OPTIMAL project developed a practical and cost-effective automated solution to replace traditional hand lay-up, using qualified materials.
Traditionally, the manufacture of composite components using prepreg is essentially a handmade activity, but steps are being taken towards automation. During the past decade, several automated lay-up solutions have emerged for relatively simple geometry parts. These solutions are often quite expensive, and commonly demand factories to be designed from scratch for their installation. They typically require special environments in the form of isolated cells with dedicated safety systems. As an alternative, collaborative robots (cobots) could be integrated into the existing manufacturing workflows to automate some tasks and improve productivity without drastically changing the surrounding environment.
Industrial robots are fast, strong and have exceptional accuracy and repeatability, but they are developed aiming only at optimization of the final result. In comparison, cobots are slower, less accurate and handle smaller payloads, but have what is needed to automate simple tasks, especially alongside with humans, at considerably less cost. Cobots have load sensors which detect the smallest impacts and stop safely.
OPTIMAL´s objective when developing cobot technologies is to improve its own capacity, and that of other companies, to offer more repeatable, higher-quality products in large quantities and at lower prices.
Within the PASSARO project’s Work Package 10, three main steps were developed using collaborative robots:
- Ply pick-up and sorting, directly from the automated ply cutter;
- Ply peeling using a dedicated cell;
- Ply positioning and stacking in a tool.
To implement these activities, a cell was developed which receives prepreg plies from the ply cutter and automatically peels and stacks them onto a mold.
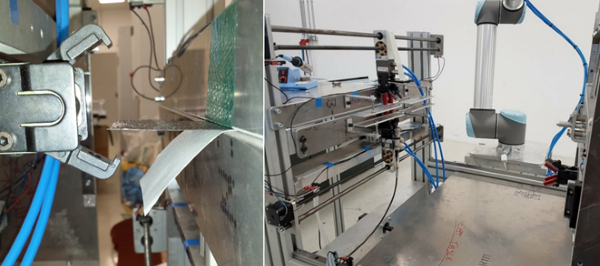
Collaborative robots used for composite manufacturing in the PASSARO project. SOURCE: ISQ Group
Positioning and stacking tasks are completed by the robot arm using special suctions cups for prepreg handling. The peeler is a more complex machine, utilizing compressed air to peel the prepreg, which is protected by two coatings — typically one plastic and one paper, or simply by two plastics. The peeling concept is based on the fact that different materials tend to vibrate at different frequencies when the same stimulus is applied. The different vibration frequencies produce air pockets between the prepreg and the covering layers. The plate resonator adjusts the vibration amplitude for different materials. This prototype could achieve peeling rates with near 100% success for specific materials and a stacking accuracy of ± 0.5 mm, in each of the two degrees of freedom in plane of the mold, and ± 0.1º in rotation.
The modular approach adopted for this system makes it independent of ply dimensions. The width is covered by adding more parallel peeling modules and the length by adjusting the peeler opening range. This technology, when compared with a human operator, offers a clear improvement in process accuracy, repeatability and especially cycle time, with reductions up to 70%.
Authors: António Reis, Nicole Cruz, Marco Neves (OPTIMAL) and Rúben Buelga Sanchez (ADS). For more information, contact:
INEGI
Campus da FEUP
Rua Dr. Roberto Frias, 400
4200-465, Porto, Portugal
Tel: (+351) 229 578 710
Email: passaro@inegi.up.pt
Related Content
Welding is not bonding
Discussion of the issues in our understanding of thermoplastic composite welded structures and certification of the latest materials and welding technologies for future airframes.
Read MorePlant tour: Joby Aviation, Marina, Calif., U.S.
As the advanced air mobility market begins to take shape, market leader Joby Aviation works to industrialize composites manufacturing for its first-generation, composites-intensive, all-electric air taxi.
Read MorePEEK vs. PEKK vs. PAEK and continuous compression molding
Suppliers of thermoplastics and carbon fiber chime in regarding PEEK vs. PEKK, and now PAEK, as well as in-situ consolidation — the supply chain for thermoplastic tape composites continues to evolve.
Read MoreMcLaren celebrates 10 years of the McLaren P1 hybrid hypercar
Lightweight carbon fiber construction, Formula 1-inspired aerodynamics and high-performance hybrid powertrain technologies hallmark this hybrid vehicle, serve as a springboard for new race cars.
Read MoreRead Next
“Structured air” TPS safeguards composite structures
Powered by an 85% air/15% pure polyimide aerogel, Blueshift’s novel material system protects structures during transient thermal events from -200°C to beyond 2400°C for rockets, battery boxes and more.
Read MoreVIDEO: High-volume processing for fiberglass components
Cannon Ergos, a company specializing in high-ton presses and equipment for composites fabrication and plastics processing, displayed automotive and industrial components at CAMX 2024.
Read MoreDeveloping bonded composite repair for ships, offshore units
Bureau Veritas and industry partners issue guidelines and pave the way for certification via StrengthBond Offshore project.
Read More