Covestro and ParaMatters develop anisotropic optimization software for composites
Designers and engineers can use the new optimization tool to obtain the most optimal part design based on material deposition and fiber orientation.
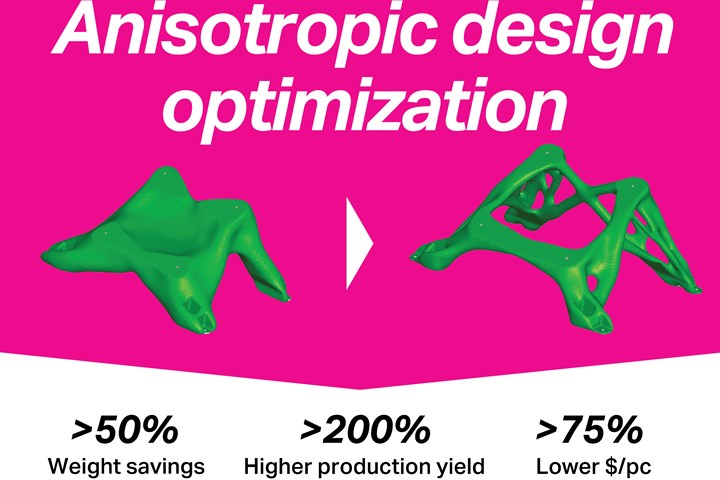
Photo Credit: Covestro
Materials company Covestro (Leverkusen, Germany) and ParaMatters (Ventura, Calif., U.S.), a multi-threaded generative design and manufacturing optimization software company, announced a jointly developed optimization software for anisotropic materials.
By combining ParaMatters’ expertise in design and manufacturing optimization technology and Covestro’s knowledge in engineered materials, the two companies are delivering a complete anisotropic design and workflow of filament extrusion 3D printing with fiber-reinforced materials.
According to the companies, by using the new optimization tool, designers and engineers can quickly obtain the most optimal part design based on material deposition and fiber orientation, and generate the most efficient printer toolpath. The result is materials, weight and cost savings — while maintaining part performance.
Following successful initial evaluation by leading aerospace users, including Composite Technology Center GmbH (Stade, Germany), on multiple filament extrusion printers, Covestro and ParaMatters are introducing the beta version so more users can try anisotropic materials. Users who want to join the expanding beta program, as well as providers of filament-based extrusion 3D printers that want to qualify and certify their systems, can contact ParaMatters to request more information.
Avi Reichental, ParaMatters’ co-founder and chairman, says, “We are proud to partner with Covestro and be the first to market with such a powerful design and manufacturing optimizer.”
Related Content
-
ATLAM combines composite tape laying, large-scale thermoplastic 3D printing in one printhead
CEAD, GKN Aerospace Deutschland and TU Munich enable additive manufacturing of large composite tools and parts with low CTE and high mechanical properties.
-
Optimized approach to predict delamination failure in CFRTP structures
ARRK Engineering and Mitsui Chemicals improved delamination prediction accuracy to help optimize absorbed energy/failure load for an overmolded TAFNEX CF/PP UD tape bumper beam.
-
Jeep all-composite roof receivers achieve steel performance at low mass
Ultrashort carbon fiber/PPA replaces steel on rooftop brackets to hold Jeep soft tops, hardtops.