FACC scholarship holders take off with self-constructed drone
Completed under the Lightweight Design and Composite Materials program, students successfully developed a lightweight camera drone with structural parts 40% lighter than comparable models.
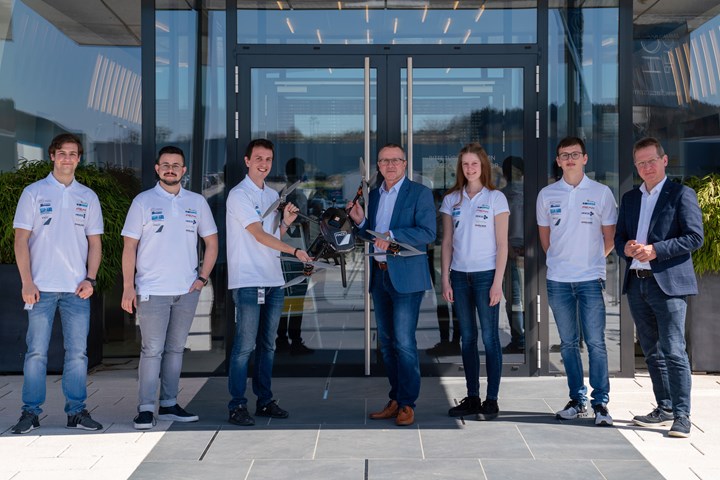
FACC scholarship holders and the self-constructed drone. Photo Credit: FACC AG
FACC AG (Ried im Innkreis, Austria) announces that students under its Lightweight Design and Composite Materials Bachelors degree program, jointly launched with the Upper Austrian University of Applied Sciences (Wels, U.K.) in 2018, have independently developed a lightweight camera drone, successfully completing the complex training and demonstration project on lightweight design. FACC says the students’ successes also demonstrate the future prospects and opportunities for further development offered by the program.
According to the company, innovative lightweight construction is a cross-sectional technology facilitating the implementation of key items, such as sustainability, efficiency and cost effectiveness. Further, it is a central theme for the mobility industry, leading to the high demand for composite in aircraft construction.
“Whereas 30 years ago, the share of composites used in aircraft was only 13%, state-of-the-art models now boast a composite share of more than 50%,” explains Robert Machtlinger, CEO of FACC AG.
“Anyone with an interest in lightweight construction and the natural sciences, such as chemistry or physics, and who wants to work in an outstanding future-oriented field is very welcome.”
In addition to making major contributions to technical progress in aerospace, and setting new standards for innovative air mobility solutions within urban agglomerations, FACC, alongside industrial partners, also focus on interacting with students. The current project, completed after a lengthy research and development phase, demonstrates a 40% weight reduction for the aircraft’s structural components compared to comparable models. FACC says the small flying object not only showcases the know-how of the students and their intensive cooperation with FACC, but will also encourage other young high potentials to deliver top performances.
FACC also notes that high-quality training programs are few and far between internationally, and lightweight construction experts are in high demand worldwide. “Knowledge and competence are crucial for the development and application of novel technologies — the demand for future specialists is high. In 2018, we took over the patronage of the new and innovative Bachelor’s degree program in Lightweight Construction and Composite Materials at the campus of the Upper Austrian University of Applied Sciences. There is no substitute for knowledge, and it becomes all the more valuable with a regional education that creates international opportunities,” says Machtlinger.
“Top-class and exclusive study content, excellent job prospects in a strong economic province, an attractive research environment and modern infrastructure at the Faculty of Engineering and Applied Natural Sciences at the Upper Austrian University of Applied Sciences in Wels — the unique Bachelor’s degree program in Lightweight Construction and Composite Materials speaks for itself,” emphasizes the head of the research group, FH Prof. DI Dr. Roland Hinterhölzl. The application period for admission to the program has already begun, and there are still a few sought-after places available for the program beginning in autumn. Dr. Hinterhölzl encourages students to join. “Anyone with an interest in lightweight construction and the natural sciences, such as chemistry or physics, and who wants to work in an outstanding future-oriented field is very welcome,” he says.
Applications are open to those who have successfully completed higher technical colleges (HTL), colleges for higher vocational education (BHS) and academic secondary schools (AHS), and to future students without a higher education entrance qualification (Matura) who are enrolled in a university entrance qualification course (Studienbefähigungslehrgang). Further information can be found at www.fh-ooe.at/lcw.
Related Content
Cryo-compressed hydrogen, the best solution for storage and refueling stations?
Cryomotive’s CRYOGAS solution claims the highest storage density, lowest refueling cost and widest operating range without H2 losses while using one-fifth the carbon fiber required in compressed gas tanks.
Read MoreComposites manufacturing for general aviation aircraft
General aviation, certified and experimental, has increasingly embraced composites over the decades, a path further driven by leveraged innovation in materials and processes and the evolving AAM market.
Read MoreWelding is not bonding
Discussion of the issues in our understanding of thermoplastic composite welded structures and certification of the latest materials and welding technologies for future airframes.
Read MoreCombining multifunctional thermoplastic composites, additive manufacturing for next-gen airframe structures
The DOMMINIO project combines AFP with 3D printed gyroid cores, embedded SHM sensors and smart materials for induction-driven disassembly of parts at end of life.
Read MoreRead Next
FACC successfully develops novel composite flap system for Wing of Tomorrow
RTM’d five-meter-long, complex multicell flap prototype constructed via a highly integral, cost-effective manufacturing process.
Read More“Structured air” TPS safeguards composite structures
Powered by an 85% air/15% pure polyimide aerogel, Blueshift’s novel material system protects structures during transient thermal events from -200°C to beyond 2400°C for rockets, battery boxes and more.
Read MoreAll-recycled, needle-punched nonwoven CFRP slashes carbon footprint of Formula 2 seat
Dallara and Tenowo collaborate to produce a race-ready Formula 2 seat using recycled carbon fiber, reducing CO2 emissions by 97.5% compared to virgin materials.
Read More