National Composites Centre leads dismantlable joints research
Adhesive additive technology is reported to make composite parts easier to dismantle, maintain and recycle.
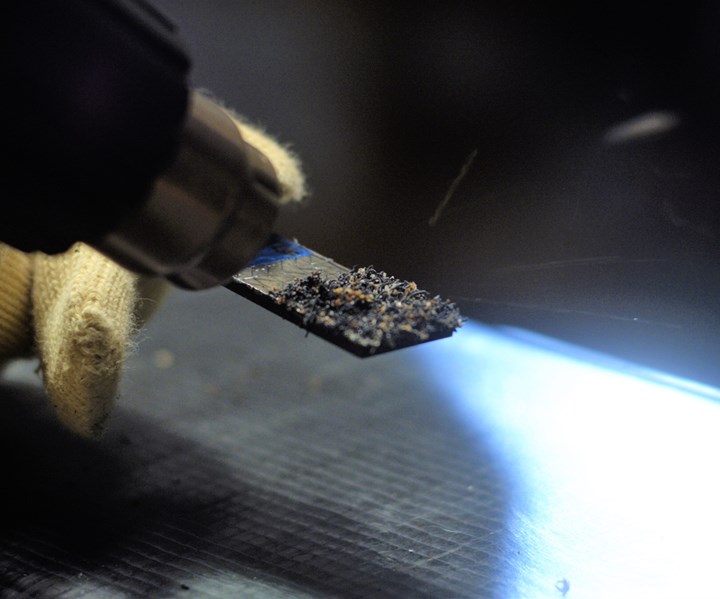
Source | National Composites Centre
The National Composites Centre (NCC, Bristol, U.K.) and Oxford Brookes University announce that they have developed a new technology that enables composite structures to be separated (or disbonded) quickly and cheaply using a simple heat source. With a goal of making it easy to work with, repair and disassemble composite parts, the researchers intend for this technology to significantly impact on the design, use and end-of life recycling of a wide range of products, including cars, aircraft and wind turbines.
Researchers at Oxford Brookes University demonstrated that by adding low-cost additives to off-the-shelf structural adhesives, composite parts could be separated in as little time as six seconds by raising the temperature of the joint to approximately 160°C. The National Composites Centre reports that it has now proved that the new approach works at an industrial scale as part of its Technology Pull-Through Programme, which exists to transition new ideas from the lab to the marketplace.
“With this technology, we can take [end-of-life composite] structures apart to be repaired, reconfigured, or used in different ways.”
Small quantities of expandable graphite (widely used for fire protection) or thermal expandable microspheres are added to adhesives routinely used to bond composite parts. According to the NCC, these additives have minimal impact on the performance of components in normal operation, but when heated to the required temperature exert a force causing components to “pop apart.” This means, NCC says, that in the near future, composite components may be easily repositioned and reused during manufacturing – reducing waste, repaired in operation and recycled more efficiently at the end of their working life.
“This is a really exciting development, especially with sustainability being an increasingly significant challenge for the industry,” says Lucy Eggleston, research engineer at the NCC. “Historically, when a part is damaged or reaches the end of its life, it would be classed as waste and discarded. With this technology, we can take these structures apart to be repaired, reconfigured, or used in different ways. This could increase available end-of-life strategies for components, ultimately reducing their impact on the environment.”
For example, the automotive sector, NCC says, is looking to increase its use of composites and bonded parts in order to reduce vehicle weight. Vehicles also have to be 85% recyclable to comply with end-of-life directives. The new technology would reportedly enable mechanics to swap damaged parts using a simple heat gun. Recyclers could put whole cars through low-temperature ovens and watch them dissemble themselves in seconds.
The researchers also hope to extend this technology to recycling of the large amounts of carbon fiber and glass fiber composites on scrapped aircraft and wind turbine blades.
“We’ve been looking at ways to disbond structural adhesives for about 10 years, and working with the NCC through the Technology Pull-Through programme has enabled us to prove the technology readiness of our research,” says Professor James Broughton, head of the Joining Technology Research Centre at Oxford Brookes University. “We can now work with industry to fully optimize the technology for specific applications and tailor it for them as required.”
Related Content
Recycling end-of-life composite parts: New methods, markets
From infrastructure solutions to consumer products, Polish recycler Anmet and Netherlands-based researchers are developing new methods for repurposing wind turbine blades and other composite parts.
Read MorePolar Technology develops innovative solutions for hydrogen storage
Conformable “Hydrogen in a Box” prototype for compressed gas storage has been tested to 350 and 700 bar, liquid hydrogen storage is being evaluated.
Read MoreComposites end markets: Energy (2024)
Composites are used widely in oil/gas, wind and other renewable energy applications. Despite market challenges, growth potential and innovation for composites continue.
Read MoreJEC World 2023 highlights: Recyclable resins, renewable energy solutions, award-winning automotive
CW technical editor Hannah Mason recaps some of the technology on display at JEC World, including natural, bio-based or recyclable materials solutions, innovative automotive and renewable energy components and more.
Read MoreRead Next
All-recycled, needle-punched nonwoven CFRP slashes carbon footprint of Formula 2 seat
Dallara and Tenowo collaborate to produce a race-ready Formula 2 seat using recycled carbon fiber, reducing CO2 emissions by 97.5% compared to virgin materials.
Read MoreDeveloping bonded composite repair for ships, offshore units
Bureau Veritas and industry partners issue guidelines and pave the way for certification via StrengthBond Offshore project.
Read MoreVIDEO: High-volume processing for fiberglass components
Cannon Ergos, a company specializing in high-ton presses and equipment for composites fabrication and plastics processing, displayed automotive and industrial components at CAMX 2024.
Read More