Plataine earns patent grant for manufacturing optimization using digital thread technology
Plataine’s newly patented, software-based technology creates a virtual replica of the factory floor in real time for a comprehensive searchable production record.
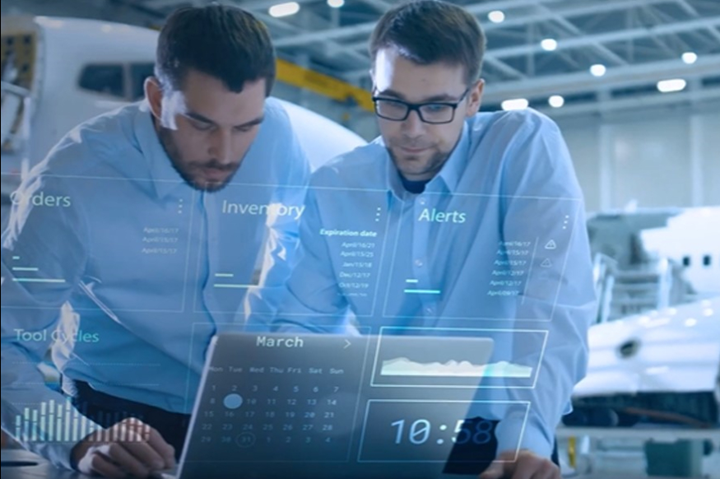
Photo Credit: Plataine
Plataine (Waltham, Mass., U.S.), announced on Jan. 20 that it has been granted U.S. Patent #10852712, titled “Tracking production processes in a manufacturing facility using searchable digital threads.” The solution that has been patented is a software-based method for tracking production across factory operations using digital twin and digital thread technology. Plataine uses cloud-based AI technology to create a virtual replica of the factory floor in real time, a digital twin, to track every element of production, from raw material to end product, creating a comprehensive searchable production record, the digital thread (see “Digital thread vs. digital twin).
According to Plataine, the newly patented method operates by tracking the location, status and operations of all key assets — such as machines, tools, raw materials, kits, work-in-progress and parts — in the production environment and monitors them throughout the factory. This establishes full, real-time connectivity, recording the status and location of every asset to weave a searchable database of digital threads that can report on each production line, at any time and place on the production floor. This ensures software and manufacturing managers are always aware of what is happening at every stage of the production line, allowing them to constantly prioritize and optimize operations and take any preemptive action to avoid future problems. Meanwhile, the digital thread offers full traceability for quality and quality control purposes, ensuring that highly regulated zero-error-tolerance industries such as aerospace, are always audit-ready.
“We are excited to add another substantial recognition from the U.S. Patent and Trademark Office (USPTO),” says Avner Ben-Bassat, president and CEO at Plataine. “The Industrial Internet of Things [IIot] is employing digital technology, driving a fourth industrial revolution, and we are rapidly moving into a future where all factories are able to track, trace and share all data in real-time. Our goal is to push the envelope of manufacturing with our artificial intelligence and IOT technologies, helping our customers at every step of their digital journey towards the transition into fully digitalized manufacturing. The new patent grant is yet another milestone in achieving this goal.”
Related Content
-
Next-gen composites manufacturing: Combining material, machine and mold cavity data with analytics
Using a sensor, an edge device and machine learning software, sensXPERT sees into processes and is improving quality and cutting scrap, cycle time and energy use for composites customers like ZF and Carbon Revolution.
-
Siemens Gamesa, Airborne develop automatic preforming robot system for offshore wind blades
Danish-funded ALMA project furthers collaboration, adds new functionality, advanced sensor systems and digital twinning for reduced man-hours, waste and cost per blade.
-
Schrödinger advances materials informatics for faster development of next-gen composites
Cutting time to market by multiple orders of magnitude, machine learning and physics-based approaches are combined to open new possibilities for innovations in biomaterials, fire-resistant composites, space applications, hydrogen tanks and more.