PRF Composite Materials opens fourth manufacturing facility
The completed £6 million investment and expansion program increases the company’s R&D, capacity expansion and sustainability.
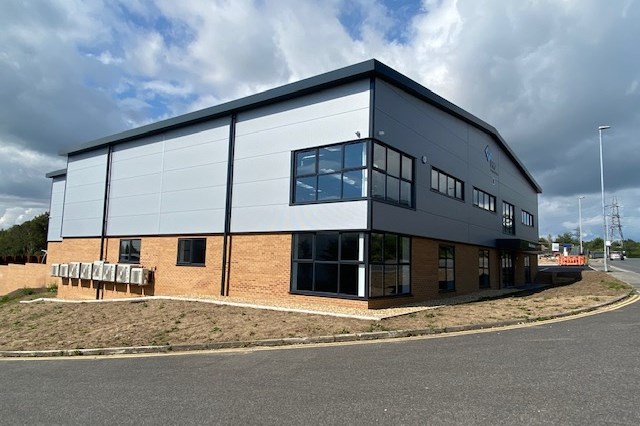
Photo Credit: PRF Composite Materials
PRF Composite Materials (Poole, U.K.) announces the opening of its fourth manufacturing facility, completing an investment and expansion program approaching £6 million, and significantly increasing manufacturing and R&D capacity and capability. This state-of-the-art, purpose-built 14,700-square-foot manufacturing site brings material processing for kitting into a single, controlled environment, the company notes, increasing manufacturing efficiency and helping PRF to minimize the impact of excessive price increases seen across the industry.
In total, this new facility increases PRF’s total factory space to 40,000 square feet, and will make space in its other sites for further R&D and manufacturing expansion. Throughout 2020 and 2021, the team have reportedly been busy investing and improving in R&D, with a complete upgrade of test equipment in both chemical and material testing laboratories, thereby opening the door for new product development and technologies. The team has also increased freezer storage space to 735 cubic meters and installed an additional CNC machine and a third impregnation line. With sustainability in mind, the new site has been built with eco-efficient fixtures and fittings, including a PV system which generates 29,965 kilowatts of electricity a year, saving 16,676 kilograms of carbon dioxide.
“Completing this significant expansion and investment into both capacity and technology will ensure that PRF can meet and exceed market and customer needs for the future, with industry-leading, innovative product development and efficient manufacturing,” says Head of Operations, Dave Ellson. “PRF will continue to invest in R&D, capacity expansion and sustainability; working with our customers and supply chain with environmental needs in mind to contribute to a better future.”
Related Content
-
Novel composite technology replaces welded joints in tubular structures
The Tree Composites TC-joint replaces traditional welding in jacket foundations for offshore wind turbine generator applications, advancing the world’s quest for fast, sustainable energy deployment.
-
JEC World 2023 highlights: Recyclable resins, renewable energy solutions, award-winning automotive
CW technical editor Hannah Mason recaps some of the technology on display at JEC World, including natural, bio-based or recyclable materials solutions, innovative automotive and renewable energy components and more.
-
Plant tour: Arris Composites, Berkeley, Calif., U.S.
The creator of Additive Molding is leveraging automation and thermoplastics to provide high-volume, high-quality, sustainable composites manufacturing services.