Strohm thermoplastic composite pipes receive DNV certification, reported to have low carbon footprint
Strohm and Evonik’s carbon fiber/PA12 pipes are now fit to use for hydrocarbons transport. A lifecycle report also found the TCP pipes to have a 60% lower carbon footprint than an equivalent carbon steel pipeline.
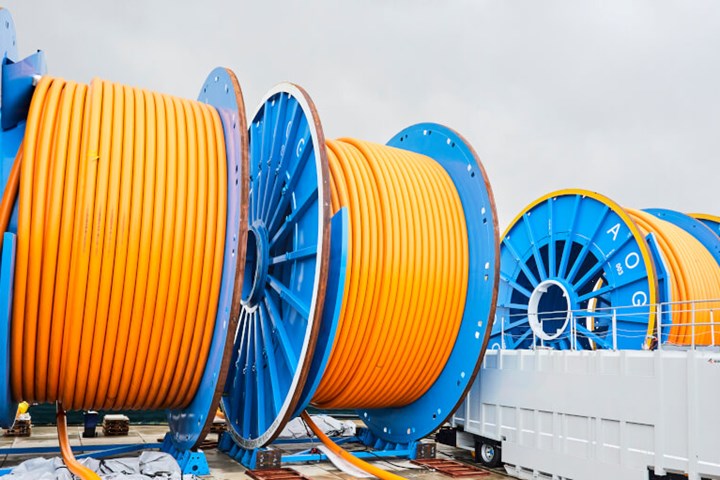
Photo Credit: Strohm
Strohm (IJmuiden, Netherlands) and Evonik (Essen, Germany) have been awarded the full certification from DNV (Høvik, Norway), attesting that the unidirectional (UD) carbon fiber PA12 tape “Vestape PA12-CF” (PA12) used for Strohm’s 100% recyclable thermoplastic composite pipes (TCP) is fit to use for dynamic sweet and sour hydrocarbons, water and gas injection applications according to DNV-ST-F119.
The two companies, in partnership with the Netherlands Aerospace Centre (NLR, Amsterdam, Netherlands), have reportedly led the way in the development, qualification and supply of PA12 for TCP applications following an intensive investment and testing program over the past five years, in which the NLR provided the main composite testing facilities. The program served to develop a fundamental understanding of the material to demonstrate the lifetime performance of a product operating in a challenging chemical, thermal and mechanical environment.
During the program, Rens Ubels, principal project engineer at NLR points to one test, where the carbon fiber-reinforced PA12 specimens were tested in-situ in Norsok fluid at elevated temperatures, something that proved challenging. “We successfully designed and built dedicated fatigue and stress rupture setups to be able to meet the test specifications and the safety and health regulations,” Ubels adds.
PA12 is a fully non-metallic, corrosion-resistant solution. Reinforced with carbon fibers, it is said to be exceptionally resistant to fatigue-based failures, marking it for any dynamic application, from jumpers to flowlines and risers, including sweet and sour hydrocarbon, water and gas service. Moreover, the carbon fiber’s high stiffness, paired with the load transfer capability of PA12 as a matrix, also enables it for deepwater service and operating pressures up to 700 bar and temperatures up to 80°C. The material has been qualified for a lifetime of up to 30 years. Further expansion of the scope will include hydrogen and carbon capture use and storage.
“Developing a material class for disruptive technologies is always challenging. PA12 for Strohm’s TCP applications was no exception,” notes Carsten Schuett, industrial and energy technology leader at Evonik. “The full application of the DNV’s standard’s approach to qualify the material has only added to the complexity but, with the help of our partners, we finally succeeded in characterizing the material in unprecedented detail and unlocked its full potential. The resulting dataset can be used generically, removing the need for material qualification in further projects which further enables us to use it for energy transition applications.”
A whitepaper discussing the qualification can be found here.
Eco-friendly thermoplastic pipes
DNV, Strohm and the Non-Metallic Innovation Centre (NIC, Cambridge, U.K.) have also launched a report comparing the lifecycle carbon footprint of externally coated carbon steel pipe and TCP, finding that the latter has a significantly lower carbon footprint — between 30-60% — than an equivalent carbon steel pipeline solution.
The report outlines the results from a joint industry project (JIP) between the three companies focusing on the lifecycle of a 22-kilometer (14-mile) pipeline transporting produced water for injection in a field outside Angola in western Africa, with an operating lifetime of 20 years.
The companies considered all steps of the lifecycle carbon footprint which is a measure of the direct and indirect greenhouse gas (GHG) emissions associated with all activities in the product's life cycle, from material extraction and production to the end-of-life (EOL) stage of the pipelines.
According to Caroline Justet, business growth executive for energy in transition at Strohm, the study takes a significant step towards establishing TCP as a suitable alternative to steel in offshore applications.
Related Content
Infinite Composites: Type V tanks for space, hydrogen, automotive and more
After a decade of proving its linerless, weight-saving composite tanks with NASA and more than 30 aerospace companies, this CryoSphere pioneer is scaling for growth in commercial space and sustainable transportation on Earth.
Read MoreSulapac introduces Sulapac Flow 1.7 to replace PLA, ABS and PP in FDM, FGF
Available as filament and granules for extrusion, new wood composite matches properties yet is compostable, eliminates microplastics and reduces carbon footprint.
Read MoreTU Munich develops cuboidal conformable tanks using carbon fiber composites for increased hydrogen storage
Flat tank enabling standard platform for BEV and FCEV uses thermoplastic and thermoset composites, overwrapped skeleton design in pursuit of 25% more H2 storage.
Read MoreThe lessons behind OceanGate
Carbon fiber composites faced much criticism in the wake of the OceanGate submersible accident. CW’s publisher Jeff Sloan explains that it’s not that simple.
Read MoreRead Next
Developing bonded composite repair for ships, offshore units
Bureau Veritas and industry partners issue guidelines and pave the way for certification via StrengthBond Offshore project.
Read MoreAll-recycled, needle-punched nonwoven CFRP slashes carbon footprint of Formula 2 seat
Dallara and Tenowo collaborate to produce a race-ready Formula 2 seat using recycled carbon fiber, reducing CO2 emissions by 97.5% compared to virgin materials.
Read MorePlant tour: Daher Shap’in TechCenter and composites production plant, Saint-Aignan-de-Grandlieu, France
Co-located R&D and production advance OOA thermosets, thermoplastics, welding, recycling and digital technologies for faster processing and certification of lighter, more sustainable composites.
Read More