CGTech releases Vericut version 9.3 for smarter machining
This latest Vericut release offers added and improved featured for highly optimized, yet safe NC program running for CNC machines.
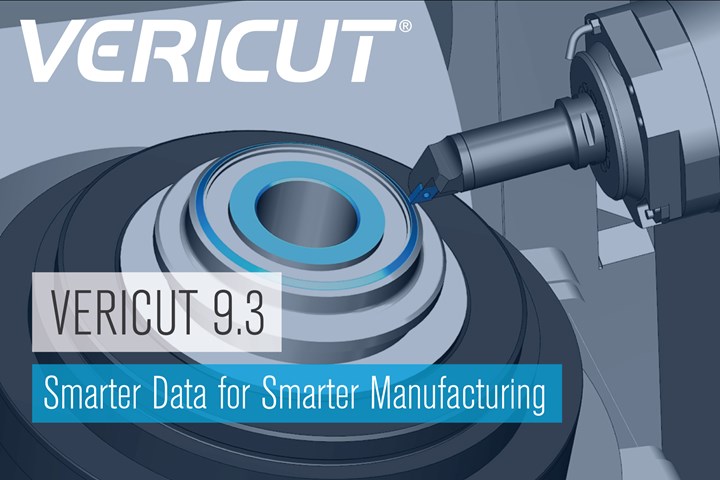
Photo Credit: CGTech
CGTech (Irvine, Calif., U.S.) announces the latest release of Vericut version 9.3, a software program used for simulating CNC machining, additive and hybrid manufacturing processes — in addition to targeting composites machining. The software operates independently, but also integrates with all leading CAM systems.
Vericut 9.3 focuses on creating “smarter,” more efficient manufacturing processes with features that bring in data around the machine, the tools and the stock to improve simulation and the overall manufacturing workflow, according to the company. Improvements have been made to strengthen the software’s core, including improved collision checking, increasing the limit on axes per subsystem and more. Cutting tool data in the Tool Performance Database and machine monitoring are only a few of the notable changes in this version. Hundreds of customer-driven changes and improvements have also been addressed in this latest release.
In 9.3 Tool Manager connects users with online tooling sources and tool databases to import “smart” cutting tools with corresponding data for proper use. In addition, a new Tool Performance Database enables even non-machinists to choose appropriate feeds and speeds for cutting a variety of common stock materials. Ultimately, this intelligence is said to help programmers use and optimize cutting tools as they were intended, avoiding broken cutters and potential damage to parts or CNC machines.
Vericut’s integrated optimization module, Vericut Force, has also received additional features and enhancements in 9.3. Alongside improvements to core features and functionality, deflection calculations have changed to account for the entire rotating tool assembly, where previous versions only accounted for solid round tools with holders. This change in deflection along with cutting tool data and information about stock material, improves part surface finish, ensures the part meets the appropriate dimensions and extends cutter life. Jason Mills, engineering manager at Advanced Manufacturing Ltd. (AML, Kerikeri, New Zealand), notes that AML has been up to 40% more tool life and 30-40% savings in machining cycle time.
Vericut’s Assembly Manager can be used to create and manage portions of NC machines such as rotary table configurations, angle heads for machining, robot end effectors or various workholding setups with fixtures and workpieces to be machined. The library of assemblies reportedly saves programmer time since they are easily accessed by others, and for repeated use in new Vericut projects.
Machining and information seen in the Status Window and Head Up Display (HUD) is more streamlined. CGTech says the HUD can automatically update to match visible Status information, or use “Field Visibility Edit Mode” to concurrently edit Status and HUD configurations. Users can lock and unlock the visibility of status groups to retain the same layout for every Vericut project opened.
Better machined part quality and longer tool and spindle bearing life are additional improvements made to Force. Deflection calculations have been updated to account for the entire rotating tool assembly, including indexable insert mills and model file cutters. Users can also add volume removal rate (VRR) limits to all cutters. Analysis and optimization for solid round tools and complex cutters has also been added.
Vericut’s Tool Manager now includes a Tool Performance Database (TPD) that suggests starting spindle speed and feed rates values to use with cutters in a wide range of stock materials. This data works with Machining Optimization Data (MOD) in the software’s Tool Manager. MOD displays a table of spindle speeds and feed rates that helps programmers choose appropriate cutting speeds and chip thickness values based on the cutting tool used, and stock material being machined.
Finally, data can be received directly from CNC machines on the shop floor for use in Vericut. The first connective ability being released with Vericut 9.3 is Pre-Check, which obtains data from machines to ensure the software’s virtual machine is the best possible “twin,” and validate the job setup information on the machine matches what was verified in Vericut.
Read Next
All-recycled, needle-punched nonwoven CFRP slashes carbon footprint of Formula 2 seat
Dallara and Tenowo collaborate to produce a race-ready Formula 2 seat using recycled carbon fiber, reducing CO2 emissions by 97.5% compared to virgin materials.
Read MoreVIDEO: High-volume processing for fiberglass components
Cannon Ergos, a company specializing in high-ton presses and equipment for composites fabrication and plastics processing, displayed automotive and industrial components at CAMX 2024.
Read More“Structured air” TPS safeguards composite structures
Powered by an 85% air/15% pure polyimide aerogel, Blueshift’s novel material system protects structures during transient thermal events from -200°C to beyond 2400°C for rockets, battery boxes and more.
Read More