Comprehensive group portfolio targets holistic engineering, tooling and epoxy resins
JEC World 2024: The RAMPF Group is bringing together three of its divisions — RAMPF Composite Solutions, RAMPF Tooling Solutions, and RAMPF Group Inc. — delivering a variety of materials and services to the composites industry.
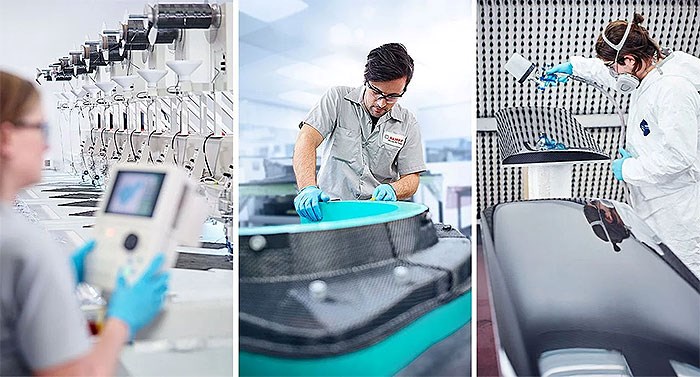
RAMPF Composite Solutions is presenting holistic engineered solutions for technologically advanced composite design in the aerospace, defense, transportation, medical and green technology industries. Source (All Images) | RAMPF Group
The RAMPF Group (Grafenberg, Germany), highlighting three out of its six core competencies — RAMPF Composite Solutions, RAMPF Tooling Solutions, and RAMPF Group Inc. — is presenting its comprehensive product and service portfolio for the cost-effective production of high-performance composite parts.
RAMPF Composite Solutions is showcasing holistic engineered solutions for technologically advanced composite design in the aerospace, defense, transportation, medical and green technology industries. The company’s experts automate composites manufacturing and reduce cost through the use of tailored fiber placement (TFP), tooling materials with optimized mechanical properties and high-performance liquid resin systems. Through material qualification and built-in quality assurance, RAMPF Composites Solutions says it is able to manufacture subsystems and fully scalable prototypes within days or weeks of design stage via an innovative one-shot solution.
RAMPF Tooling Solutions is displaying high-performance epoxy boards for the production of prepreg layup tools and vacuum forming molds. This division presents four high-tech board materials — Raku Tool WB-0691, WB-0700 and WB-0890 — for applications in racing sports, marine, aerospace and medical technology. Benefits include:
- Wide temperature application range (HDT 110-140°C)
- Optimized surfaces — reduced finishing efforts, less sealer required, high edge strength
- Fast and easy to process via milling with minimal dust
- Compatible with all paints, release agents and epoxy prepregs in line with industry standards
- Adhesives that match temperature resistance and hardness of boards.
RAMPF Tooling Solutions’ product portfolio for composites manufacturing also encompasses liquid systems based on epoxy (infusion resins, laminating resins, gelcoats) and close contour materials (close contour paste, castings and blocks).
The RAMPF Group Inc. presents its comprehensive range of epoxy liquid systems for composites production. These are used, amongst others, in special mission aircraft for surveillance, firefighting and air refueling, as well as in helicopters and individual and regional air mobility.
In particular, products highlighted at JEC include:
- Raku EI-2510: A high-temperature, toughened epoxy system that exhibits improved hot-wet properties (dry Tg 210°C, wet Tg 174°C), high fracture toughness and is used for a wide range of structural applications in high-temperature environments; the low-temperature processing two-component resin requires less investment in tooling and infrastructure and no special storage.
- Raku EI-2511: High-performance, flame-retardant structural resin with a high Tg (dry 165°C, wet 137°C). The epoxy system exhibits low viscosity at low processing temperature (200 mPas at 40°C) and fulfills 12- and 60-sec vertical burn as well as the oil burner test for firewalls, engine nacelle components and cargo liners.
- The combination of Raku EI-2510 and Raku EI-2511 with close contour castings and high-performance tooling boards enables the cost-effective production of qualification-compliant components within days to weeks, according to the company.
- Raku EI-2518: Flame-retardant product for 12- and 60-sec vertical burn requirements as well as application-dependent UL94 requirements.
- Raku EI-2524: Epoxy resin infusion system with optimized processing characteristics and a wide range of hardener options. Suited for a wide range of applications ranging from structural components in aerospace, marine and various industries.
Visit the RAMPF Group at Booth 5G117 in Hall 5.
Related Content
-
Welding is not bonding
Discussion of the issues in our understanding of thermoplastic composite welded structures and certification of the latest materials and welding technologies for future airframes.
-
The state of recycled carbon fiber
As the need for carbon fiber rises, can recycling fill the gap?
-
PEEK vs. PEKK vs. PAEK and continuous compression molding
Suppliers of thermoplastics and carbon fiber chime in regarding PEEK vs. PEKK, and now PAEK, as well as in-situ consolidation — the supply chain for thermoplastic tape composites continues to evolve.