SABIC debuts EN45545 rail-compliant, fiber-reinforced compound
LNP Thermocomp AM DC0041XA51 offers the rail industry a solution that can be used for on-demand printing of large, complex exterior and interior parts in relatively small build numbers.
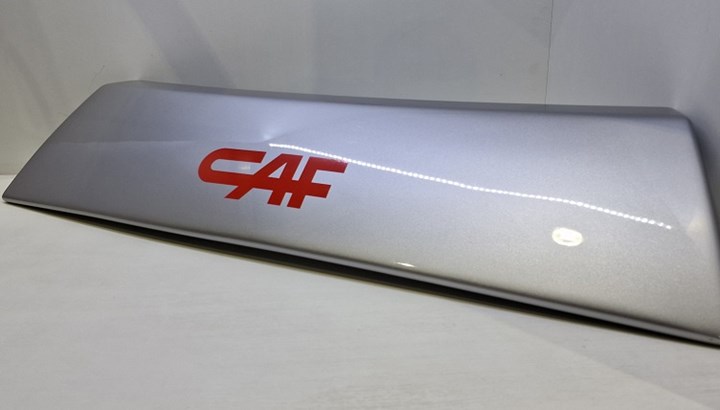
Large front hatch developed using LNP Thermocomp AM DC0041XA51. Photo Credit: SABIC
SABIC (Riyadh, Saudi Arabia, and Houston, Texas, U.S.) introduces an LNP Thermocomp AM DC0041XA51 compound, a novel carbon fiber-reinforced, flame-retardant (FR) compound well-suited for pellet-fed additive manufacturing (PFAM) that complies with EU and U.S. rail fire safety standards. According to the company, the new compound will enable the rail industry to advance from building traditional tools for part production from thermosets to using on-demand 3D printing which can potentially lower system costs by reducing inventory levels of large tools and replacement parts.
The image above features a large front-hatch part printed by CAF (Beasain, Spain), a multinational supplier of comprehensive transit solutions for major railway networks, using the LNP Thermcomp AM DC0041XA51 compound.
“With our increased focus on 3D printing, we were looking for a material that complies with the stringent safety requirements set forth in international standards like NFPA 130 or EN45545,” Lucas Esteban, operational manager from digital manufacturing, CAF, explains. “SABIC’s compound has unique features that fit well with industry requirements, including the appropriate railway certificates. Its non-halogenated flame-retardant system addresses current sustainability trends, and its carbon fiber reinforcement and favorable processing allow us to make larger part geometries with sufficient stiffness and limited warpage.”
LNP Thermocomp AM DC0041XA51 is well-suited for printing large- or medium-size rail components using PFAM. It is said to be one of the first PFAM-capable materials to comply with requirements of the harmonized European EN45545 standard (R1 Hazard Level 3) and the U.S. NFPA-130 standard for interior and exterior parts, standards of which place strict limits on smoke density and toxicity, heat release and flame spread. The product has been certified compliant with both standards by an independent laboratory.
The new material offers important performance advantages for printing large parts using PFAM, SABIC adds. First, the compound maintains its structural integrity during printing and delivers good dimensional stability with low warpage for the finished part. From a processing standpoint, LNP Thermocomp AM DC0041XA51 compound may eliminate the need for additional investment since the product facilitates high printing speeds at relatively moderate temperatures. Potential applications include exterior parts such as bumpers as well as interior cladding components such as side panels, partition walls and ducts, and seating backs and shells
Compared to thermosets formulated with halogen-based FR additives, SABIC’s new LNP Thermocomp AM DC0041XA51 compound provides expanded design flexibility, facilitates recycling and offers a non-halogenated FR solution. It is available globally.
Related Content
-
Longtime partner New Flyer selects Hexagon Purus to outfit hydrogen transit bus
Hexagon Purus will continue to supply Type IV hydrogen tanks for the Xcelsior Charge H2 fuel cell electric bus, the tanks of which will be produced out of Hexagon’s new Maryland facility.
-
Composite sidewall cover expands options for fire-safe rail components
R&D project by CG Rail explores use of carbon fiber-reinforced thermoplastics and recycled manufacturing scrap to meet fire safety, weight and volume targets.
-
Composites reinvent transportation
Celebrating National Composites Week, CW shares ways in which composites continue to evolve mass transit.