Composite in Netherlands tunnel firewater system
The A2 motorway used to run through Maastricht. Now it runs under it. Composite piping helps make sure the tunnel’s firewater system is always ready.
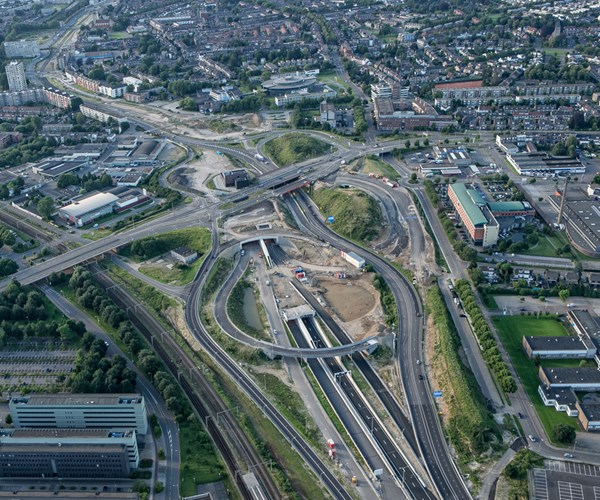
A2 tunnel entrance, aerial view, Maastricht, the Netherlands.
The A2 motorway is the most important North-South road connection in the Netherlands, carrying a very heavy traffic load. In Maastricht, the A2 motorway originally passed the town above ground, cutting the city in half. Because of the limited space available and the need to have local traffic cross the motorway, speed limits were only 50 kph, causing major traffic delays in rush hours. Consequently, noise and exhaust gases were of great annoyance to the residents living nearby, and were having a negative effect on the environment.
In 2008, the Dutch government decided to construct a completely new tunnel (King Willem- Alexander Tunnel) at the location of the existing motorway. This is the first two-layer tunnel in the Netherlands with the top level designated for local traffic, and the lower level used for transit traffic.

King Willem-Alexander Tunnel, rendering.
On top of the tunnel a new green corridor was created, improving the quality of life for the residents of Maastricht. The new 2.3-km tunnel safely processes a large amount of traffic on both levels, and consequently reduces the impact of the traffic on the environment.
The tunnel was commissioned by the Dutch National Body of Roads and Waterways (Rijkswaterstaat), and constructed by Ballast Nedam and Strukton. Tunnel construction was completed in 2015 and traffic has been going through since December 2016.
In the unlikely event of a tunnel fire or a major traffic incident, a reliable firewater system had to be installed as safety precaution. Tunnel fire regulations require the firewater system be operational at all times. If not, traffic has to be stopped immediately. It was clear from the beginning of project engineering that conventional steel pipes would not be acceptable, because of the risk of corrosion inside the pipes and, as a result, potential output limitations.
For that reason, originally, the firewater system was envisioned to be constructed in stainless steel. However, after project kick-off, it was found that total system cost was going to be unacceptably high (special steel alloys and thick pipe walls were required for continued corrosion resistance), there was a high risk of corrosion-pitting of the welds, and there were major issues with steel pipe raw material availability potentially delaying the entire A2 tunnel project timeline.
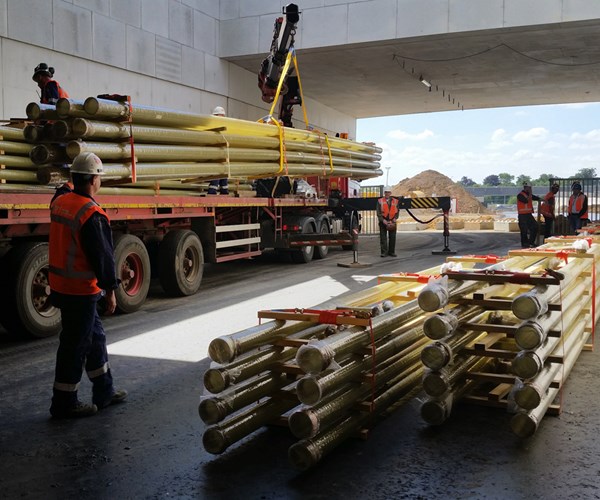
Composite pipe for the tunnel’s firewater system, manufactured by
Netherlands-based Versteden.
Composite pipe manufacturer Versteden, based in Bergen op Zoom, the Netherlands, developed an integrated solution for this tough challenge. “We could provide system design, manufacturing and installation all in one hand, with easy and direct communication between the parties,” comments Peter Bogers, managing director of Versteden. “Besides being able to deliver fast and at competitive price, we helped to keep overall project timeline on track. For project owner Rijkswaterstaat, this was obviously a major benefit.”
The heart of the new firewater system is a 125-mm-diameter composite pipe network (conforming to ISO 14692 standard), installed inside the tunnel emergency tubes, located between the main traffic tubes. In total, Versteden supplied 4.2 km of piping. The resin system used in this project was a novel Atlac resin supplied by Aliancys AG through its Distributor Euroresins.
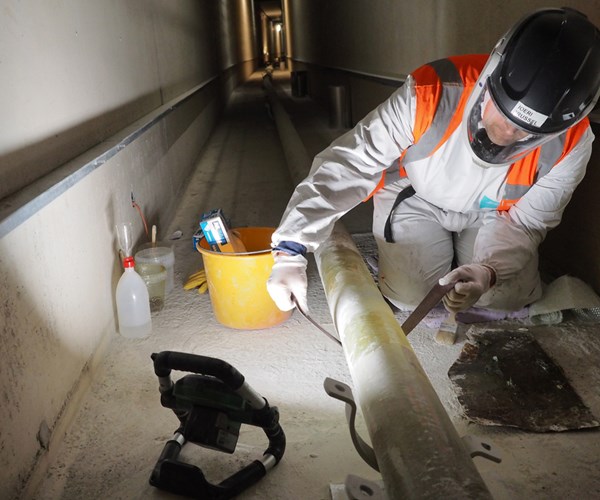
Pipe installation in the tunnel. The firewater system must be fully operational 24/7. Failure to do so forces closure of the tunnel.
“Aliancys and Euroresins have helped us to fine-tune resin formulation and provide support in promoting our GRE piping systems,” adds Peter Bogers. “With the support of both companies we can much better promote the benefits of composites solutions, and convince key stakeholders about the attractive economics and long term reliability of firewater systems in these materials.” As a positive spin-off, Versteden has been involved in several new projects since the completion of the project in Maastricht.
Related Content
Mighty Buildings opens new factory in Monterrey, Mexico
Company takes next step in strategy to scale rapid development and construction of 3D-printed, climate-resilient, carbon-neutral homes leveraged by patented composite materials.
Read MoreRenco USA brings Lego-style composite building system to construction
After more than a decade dedicated to R&D, evaluation and testing, the company has proven its MCFR building system in a Lakewood Village project in Florida.
Read MoreComposites end markets: Infrastructure and construction (2024)
Composites are increasingly used in applications like building facades, bridges, utility poles, wastewater treatment pipes, repair solutions and more.
Read MoreCirculinQ: Glass fiber, recycled plastic turn paving into climate solutions
Durable, modular paving system from recycled composite filters, collects, infiltrates stormwater to reduce flooding and recharge local aquifers.
Read MoreRead Next
“Structured air” TPS safeguards composite structures
Powered by an 85% air/15% pure polyimide aerogel, Blueshift’s novel material system protects structures during transient thermal events from -200°C to beyond 2400°C for rockets, battery boxes and more.
Read MorePlant tour: Daher Shap’in TechCenter and composites production plant, Saint-Aignan-de-Grandlieu, France
Co-located R&D and production advance OOA thermosets, thermoplastics, welding, recycling and digital technologies for faster processing and certification of lighter, more sustainable composites.
Read MoreDeveloping bonded composite repair for ships, offshore units
Bureau Veritas and industry partners issue guidelines and pave the way for certification via StrengthBond Offshore project.
Read More