Filament winding, compression molding combine on BMW M4 GTS
Cytec Solvay is debuting today a novel all-carbon fiber composite hood that it helped develop for the BMW M4 GTS, in cooperation with fabricator C-CON GmbH and automotive metals specialist Läpple AG.
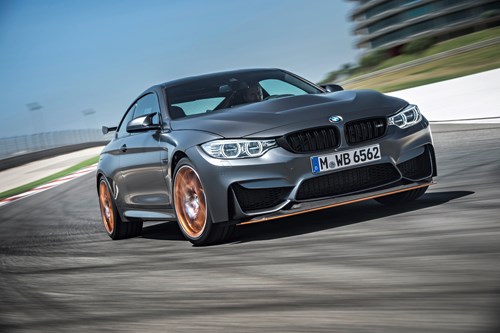
BMW's newest M4 GTS features an all-carbon fiber hood developed in just nine months and manufactured with filament winding and compression molding.
Cytec Solvay (Heanor, UK) is debuting today at the JEC 2016 trade show in Paris, France, a novel all-carbon fiber composite hood that it helped develop for the BMW M4 GTS, in cooperation with fabricator C-CON GmbH (Munich, Germany) and automotive metals specialist Läpple AG (Heilbronn, Germany).
Developed and prototyped in just nine months, the hood represents a substantial step-change in automotive parts fabrication and shows how composites fabrication can be adapted to fit within the established automotive manufacturing supply chain.
BMW, which has already made a name for itself with the liberal use of composite materials in the i3 and i8 vehicles, approached C-CON with the idea of converting the M4 GTS hood from aluminum to carbon fiber composites. C-CON, in turn, turned to Cytec (at the time not yet acquired by Solvay) for help developing the materials and processes required.
Alex Aucken, global automotive director Industrial Materials at Cytec Solvay, says short development window put tremendous pressure on all of the companies involved, but in the end, the materials and process developed produced a hood not only 40% lighter than its aluminum predecessor, but one that is also cost-effective and viable in other applications.
The 8-kg hood consists of a 1.2-mm thick Class-A outer panel bonded to a 1.2-mm thick inner structure, with additional carbon fiber composite reinforcements near two corners to support hinge components.
The novelty of the hood is in its resin matrix and its layup. The former is an epoxy developed by Cytec for the application, called MTR 760. Layup, atypically, is provided by filament winding.
Aucken and Tim Wybrow, application research and engineering manager at Cytec Solvay, say that the process developed involves in-situ application of MTR 760 resin on a 24k tow carbon fiber just prior to filament winding around a 1m diameter mandrel, in an optimized angle and layer configuration. After winding, this prepregged layup is removed from the mandrel and then slit to create a flat blank, which is then cut to shape, either for the outer or inner panel. One filament-wound layup is large enough to provide material for up to three tailored blanks.
For consolidation and cure, a tailored blank is placed flat between two layers of thermoplastic film, which are clamped in place, under tension, by a metallic frame. Cytec Solvay calls this the double-diaphragm forming process that, says Aucken, obviates the need for preforming and allows the carbon fiber blank to take the shapes required — some very complex — with minimal wrinkling.
The entire frame is then placed in a metallic mold in a compression press and cured in less than 5 minutes. Finished parts are cut and trimmed in preparation for assembly and bonding. C-CON does all of the filament winding and blank preparation. Läpple does the compression molding, trimming, cutting, and assembly.
Although technically the compression process is relatively straightforward, it is symbolic of a larger problem that the automotive and composites industries face: How to integrate composites molding processes with the metals-based legacy processes that the automotive industry employs?
In the case of the BMW M4 GTS hood, the task was to develop a composites fabrication process that could be adaptable to Läpple’s metal-forming machinery. This would allow Läpple, which has experience as a BMW supplier, to easily convert to composites fabrication without the capital equipment investment that might otherwise be required. For this reason, the M4 GTS hood is molded on a metal-forming press. “Optimizing the logistics of a metal pressing line was paramount for this project,” says Aucken. “We have to fit into the existing infrastructure,” says Wybrow.
The result is a hood that meets all of BMW’s requirements for cost, strength, stiffness and pedestrian safety. It has, says Wybrow, a void content of 1.2%, and its Class A surface is easily paintable. BMW is making only a low volume of M4 GTS models with the carbon fiber hood, but the aftermarket for the part is considerable given the hood’s compatibility with other M3 and M4 models. Further, the hood proves the viability of using filament winding as a layup process combined with standard compression molding.
The M4 GTS hood will be on display at the Cytec Solvay stand during JEC 2016, Hall 5A, K46.
Related Content
Sulapac introduces Sulapac Flow 1.7 to replace PLA, ABS and PP in FDM, FGF
Available as filament and granules for extrusion, new wood composite matches properties yet is compostable, eliminates microplastics and reduces carbon footprint.
Read MorePlant tour: Spirit AeroSystems, Belfast, Northern Ireland, U.K.
Purpose-built facility employs resin transfer infusion (RTI) and assembly technology to manufacture today’s composite A220 wings, and prepares for future new programs and production ramp-ups.
Read MoreCarbon fiber, bionic design achieve peak performance in race-ready production vehicle
Porsche worked with Action Composites to design and manufacture an innovative carbon fiber safety cage option to lightweight one of its series race vehicles, built in a one-shot compression molding process.
Read More3D-printed CFRP tools for serial production of composite landing flaps
GKN Aerospace Munich and CEAD develop printed tooling with short and continuous fiber that reduces cost and increases sustainability for composites production.
Read MoreRead Next
VIDEO: High-volume processing for fiberglass components
Cannon Ergos, a company specializing in high-ton presses and equipment for composites fabrication and plastics processing, displayed automotive and industrial components at CAMX 2024.
Read MorePlant tour: Daher Shap’in TechCenter and composites production plant, Saint-Aignan-de-Grandlieu, France
Co-located R&D and production advance OOA thermosets, thermoplastics, welding, recycling and digital technologies for faster processing and certification of lighter, more sustainable composites.
Read MoreDeveloping bonded composite repair for ships, offshore units
Bureau Veritas and industry partners issue guidelines and pave the way for certification via StrengthBond Offshore project.
Read More