HyFiVE research gains insight into metal-composite joining
HyFiVE project came to a close in 2023, providing new insight for adhesive-free joining of metal and fiber-reinforced technologies for maritime construction.
Share
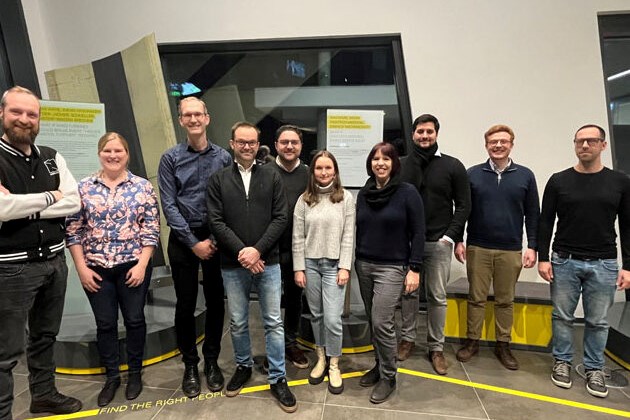
The project team at the final meeting for the HyFiVE project (from left to right): Dr. Lars Molter (Hyconnect), Mareike Woestmann (FIBRE), Dr. Patrick Schiebel (FIBRE), Jörg Bünker (Saertex), Moris Adam (Saertex), Isabel Wiedmann (Fritz Moll), Dr. Jana Fiedler (SKZ), Fabian Nowacki (ar engineers), Luiz Lise (ar engineers), Bernhard Teichmann (SKZ). Source: Moritz Adam, Saertex GmbH & Co. KG
The research project “Hybrid Joining Technology for Joints in Maritime Applications” (HyFiVE), in which composites companies like Saertex (Saerbeck, Germany) played a key role, came to an end in December 2023. The project contributed to the industrial use of materials in shipbuilding, providing insight into the adhesive-free joining of metal and fiber-reinforced plastic components.
Lightweight construction, a key element of sustainable transportation, has been slow to catch on in shipbuilding, the key reason being inadequate joining technologies for fiber composites and steel. Funded by the German Federal Ministry of Economics and Climate Protection (BMWK), HyFiVE enabled five industrial companies and three scientific institutions to develop and evaluate new technologies for maritime applications. The project ran from May 2020 to December 2023.
Under the leadership of Saertex, project partners — including SKZ Plastics Center engineers, Fritz Moll Textilwerke GmbH & Co. KG, Faserinstitut Bremen e.V., Hyconnect GmbH, Schweißtechnische Lehr- und Versuchsanstalt Halle GmbH and Eikboom GmbH — were able to gain new, extensive knowledge about surface processes and how to improve adhesion. The researchers were also able to integrate metallic connectors directly into various fiber-reinforced composite manufacturing processes and demonstrate the applicability of nondestructive testing methods already used in the field of conventional joints. The applicability of established fire protection systems to lightweight composite parts was also demonstrated. Thanks to the involvement of many companies along the entire value chain, the development results have already been tested for practicability and scalability — in other words, practical research that can provide direct added value to the industry.
“The results of the HyFiVE project are very promising and we are pleased to be able to contribute to the use of these composite materials,” says Jana Fieder, group leader in the Composites Research Department at SKZ. SKZ has an established knowledge cluster for fiber-reinforced plastics, and expertise in bonding and testing technology. “The functionality, in combination with metal components as a potential alternative to bonding, has been clearly demonstrated.”
Related Content
-
Orbital Composites installs robotic AM system at University of Rhode Island
The 12-axis Orbital S system designed to print continuous fiber-reinforced parts will be used to advance research in composites for underwater unmanned vehicles.
-
Large-format 3D printing enables toolless, rapid production for AUVs
Dive Technologies started by 3D printing prototypes of its composite autonomous underwater vehicles, but AM became the solution for customizable, toolless production.
-
Plant tour: BeSpline/Addcomp, Sherbrooke, QC, Canada
Composites automation specialist increases access to next-gen technologies, including novel AFP systems and unique 3D parts using adaptive molds.