ATC Manufacturing selected for NASA's HiCAM project
ATC will provide expertise in thermoplastic composites manufacturing to NASA’s Hi-Rate Composite Aircraft Manufacturing (HiCAM) project.
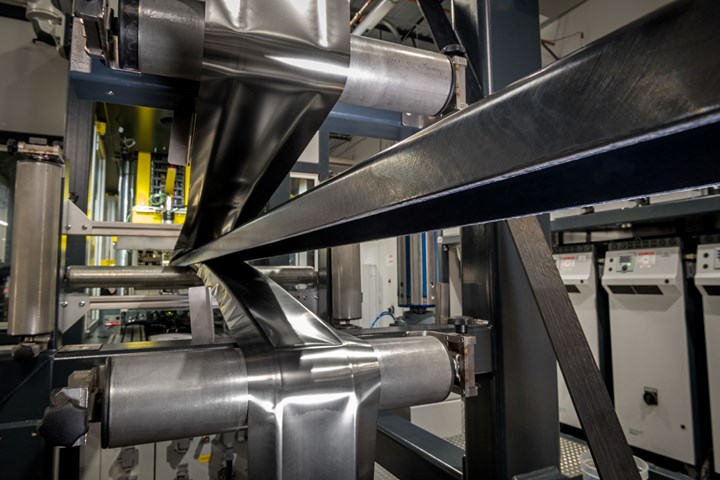
ATC Manufacturing continuous compression molding (CCM) process. Photo Credit: ATC Manufacturing
NASA recently announced awardees for the Hi-Rate Composite Aircraft Manufacturing (HiCAM) project aimed at increasing the rate of composite aircraft manufacturing, reducing costs, and improving performance for lightweight aircraft and other vehicles. ATC Manufacturing (Post Falls, Idaho, U.S.) has been selected as a key partner on the project.
The goal of the HiCAM project is to speed up the development of affordable, high-rate composite manufacturing technologies that reduce costs for labor, equipment and tooling. It will also focus on developing model-based engineering tools for high-rate manufacturing concepts. The objectives of HiCAM are key to meeting the US Aviation Climate Action Plan.
As a key member of both the HiCAM project and the Advanced Composites Consortium, ATC Manufacturing says its expertise in high-volume thermoplastic composites manufacturing will contribute to the mission to accelerate the manufacturing of large composite aircraft components. Since 2004, ATC has been among the leaders in the adoption of thermoplastic composites technology to produce tougher, lighter, and stronger parts.
“We are extremely honored to be a part of this project and we recognize that it is vital to the future of aerospace, lightweight aircraft, drones, and other vehicles. Low-cost, high-rate production of thermoplastic composite components are the key to lightweight, high-strength structures and will help industries take huge leaps in sustainability, durability, and performance. We look forward to working with and learning from the other project partners and NASA,” says David Leach, business development director at ATC.
Related Content
-
Combining multifunctional thermoplastic composites, additive manufacturing for next-gen airframe structures
The DOMMINIO project combines AFP with 3D printed gyroid cores, embedded SHM sensors and smart materials for induction-driven disassembly of parts at end of life.
-
Plant tour: Joby Aviation, Marina, Calif., U.S.
As the advanced air mobility market begins to take shape, market leader Joby Aviation works to industrialize composites manufacturing for its first-generation, composites-intensive, all-electric air taxi.
-
JEC World 2024 highlights: Thermoplastic composites, CMC and novel processes
CW senior technical editor Ginger Gardiner discusses some of the developments and demonstrators shown at the industry’s largest composites exhibition and conference.