Bcomp, KTM Technologies brake cover listed as finalist for JEC Innovation Awards 2022
Flax fibers were used to reduce the CO2 emission of the motocross brake cover by 82%, with KTM’s Conexus for effective bonding between thermoset and thermoplastic parts.
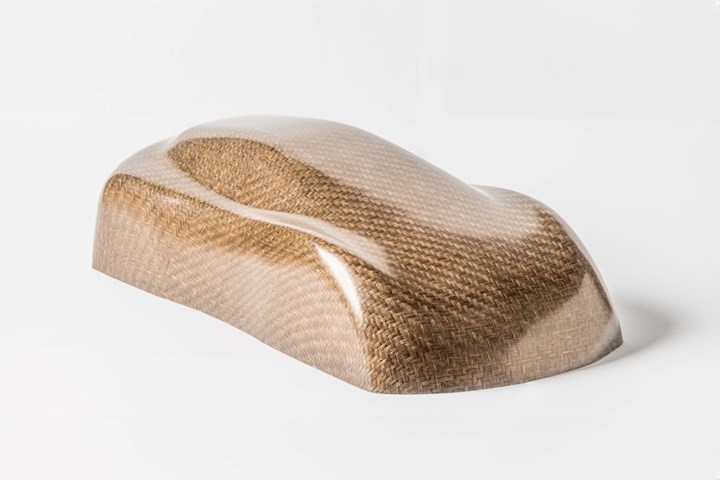
Natural fiber-reinforced motocross brake cover. Photo Credit, all images: Bcomp
A motocross brake cover developed by sustainable lightweighting company, Bcomp (Fribourg, Switzerland), and collaborator KTM Technologies (Niederalm, Austria), has been listed as a finalist in the JEC Innovation Awards 2022. Combining what is said to be the best traits from thermoset and thermoplastic polymers, the part also cuts thermoset-related CO2 emissions by 82%.
The cover uses a pre-impregnated version of Bcomp’s technical fabric ampliTex to form the basis of a lightweight and stiff structure. Once cured, the flax fiber composite part uses KTM Technologies’ Conexus coupling layer to bond reinforcement ribs, fasteners and edge protection in the form of polyamide 6 (PA6), a thermoplastic. Conexus’ chemical composition provides a direct bond between the natural fibers’ thermoset resin and the PA6 thermoplastic components.
The PA6 is then overmolded for complete edge coverage of the flax fiber part, as well as protecting against interlaminar damage caused by impacts or flying debris — a regular occurrence during motocross — and providing an aesthetic surface finish. Compared to a traditional injection molded part, the Bcomp and KTM Technologies brake cover reportedly saves weight, has increased stiffness and reduced vibrations, all while significantly reducing the part’s overall CO2 footprint. After product life, the coupling layer allows a separation of the parts, the result of a lower melting temperature than that of the thermoplastic material.
In addition to reducing the CO2 footprint of the thermoset components by around 82%, the use of ampliTex — which features a ductile fracture behavior — makes parts that are safer for riders, Bcomp says.
With ongoing advancement in the development of fully bio-based epoxy resin and bio-based PA6 already available, KTM Technologies plans to develop a completely bio-based brake cover in the near future that can be completely recovered and recycled at its end of life.
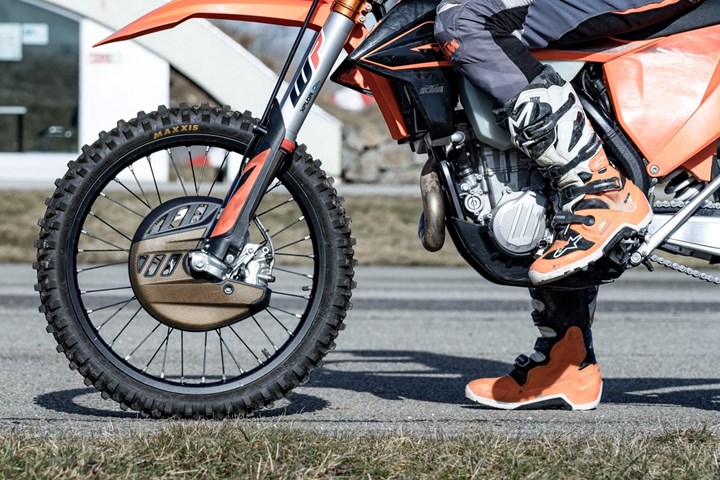
Motocross bike using the composite brake cover.
“With this demonstrator component, we have succeeded in proving the series production capability of this technology,” notes Hans Lochner, team leader material & application at KTM Technologies. “This is an important milestone for our efforts in the field of sustainable engineering and the use of bio-based composites. This is a testament that with bio-based plastics and fibers, it is possible to produce performance components in series. The reduction of the CO2 footprint in the production of motorbikes and scooters will play an even more important role in the future. Particularly two-wheelers powered by electricity or e-fuels are an alternative to cars in daily individual transport due to their low weight and small footprint with a good range. This segment is going to prove a large applicability for numerous components to use this technology.”
The JEC Innovation Awards 2022 will be presented at JEC World 2022 from May 3-5 in Paris, France.
Related Content
-
TU Munich develops cuboidal conformable tanks using carbon fiber composites for increased hydrogen storage
Flat tank enabling standard platform for BEV and FCEV uses thermoplastic and thermoset composites, overwrapped skeleton design in pursuit of 25% more H2 storage.
-
The potential for thermoplastic composite nacelles
Collins Aerospace draws on global team, decades of experience to demonstrate large, curved AFP and welded structures for the next generation of aircraft.
-
Jeep all-composite roof receivers achieve steel performance at low mass
Ultrashort carbon fiber/PPA replaces steel on rooftop brackets to hold Jeep soft tops, hardtops.