Bindatex adopts 4.0 digital technology, increases productivity by 20%
Installation of a cloud-based production data capture system significantly improved the company’s productivity and reduced leadtimes by a quarter.
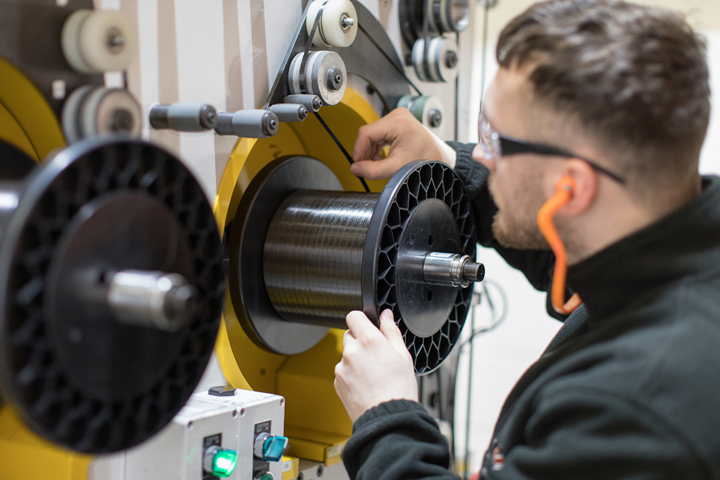
Bindatex (Bolton, U.K.) a provider of specialty process and cutting services, reported on Oct. 29 that it has taken a transformative step and increased productivity by 20% after adopting 4.0 digital technology (see “Composites 4.0: Digital transformation, adaptive production, new paradigms”) to capture, analyze and manage production data per its Made Smarter strategy.
Using Made Smarter’s digital transformation workshop to identify its challenges and potential solutions, Bindatex installed the Total Control Pro (TCP), a cloud-based production data capture system that enables the business to track products throughout the manufacturing process.
In order to enhance productivity, Bindatex says the new system was introduced after the company reconfigured its business in March in the wake of a government call for manufacturers to contribute to the fight against COVID-19. Accordingly, the company was able to change its production systems to die cut disks for filters for the manufacture of ventilators for the U.K. National Health Services (NHS).
“After installing the TCP system and applying it to the critical narrow slitting line, Bindatex eliminated unplanned overtime and reduced our lead times,” says Chris Lever, managing director of Bindatex. “Before we introduced this system, our lead time from order to delivery was half the time of other larger companies in the sector. Now it can be just over four weeks. Overall, the system improved productivity by 20%.”
According to the company, Bindatex has been cutting composites for more 15 years and contends that it is only company in the U.K. which can undertake precision slitting to widths as low as one millimeter, which usually poses a challenge for composites cutting. The company is an approved supplier to global thermoplastic and thermoset composite manufacturers across the world, and specializes in the precision cutting of “difficult-to-cut” materials. Bindatex adds that it constantly re-invests in machinery and processes to provide market-leading composite formatting services.
Related Content
-
Siemens Gamesa, Airborne develop automatic preforming robot system for offshore wind blades
Danish-funded ALMA project furthers collaboration, adds new functionality, advanced sensor systems and digital twinning for reduced man-hours, waste and cost per blade.
-
Aitiip concludes HELACS project with waterjet cutting demonstration
Novel platform involving digital twin and human-robot collaboration succeeded in cutting a component from the 19th section of an A350 wing, highlighting its ability to enable composite structure recycling.
-
DLR develops safe, flexible workspaces for robot-assisted manual draping
The EU project Drapebot works on new ways of collaborating with industrial robots for manual CFRP preforming for large aircraft structural parts.