Broetje-Automation delivers EcoPositioners for automated built-in stress-compliant joining in aircraft fuselages
Modularized and highly precise positioning system increases assembly accuracy and speed, enables digitization of CFRP aircraft components assembly for factory of the future.
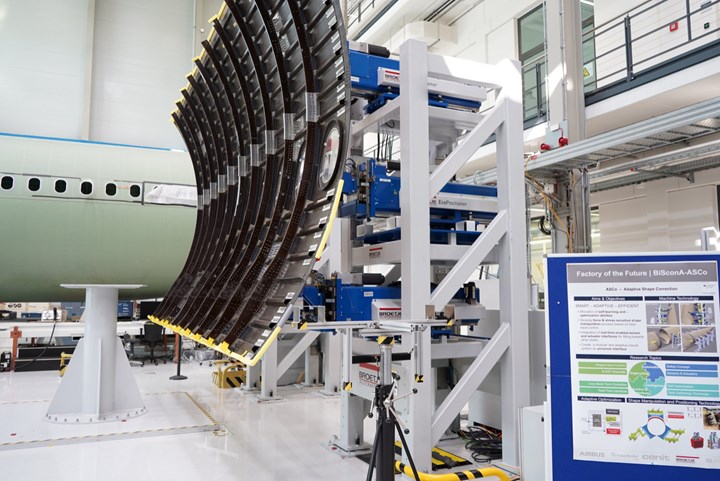
Photo Credit: Broetje Automation
A team of leading companies in the aviation industry in Hamburg, Germany is developing nothing less than the future of aircraft construction. As part of the Built-in Stress Conformal Assembly, or BiSconA project, Broetje-Automation (Rastede, Germany) celebrates the 250th delivery of the “EcoPositioner”— a modularized and highly precise positioning system specially developed for improved aircraft assembly —to the ZAL Center for Applied Aviation Research.
Together with ZAL and other partners, Broetje-Automation is working on the “BiSconA” project funded by Germany’s Federal Ministry for Economic Affairs and Energy as part of the aviation research program to develop an automated “built-in stress” -compliant joining process for aircraft fuselages that sets standards in terms of accuracy. In addition, the speed of the assembly process is improved and the stress-free state of the fuselage shell is guaranteed over the entire assembly process.
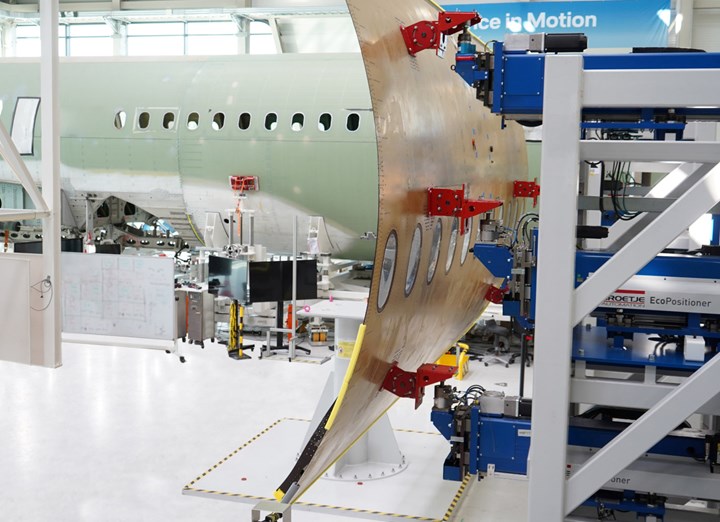
Photo Credit: Broetje Automation
Broetje-Automation explains that 250 EcoPositioners are already in use around the world. In addition, there are more than 150 other positioning systems from Broetje-Automation being used globally to ensure efficient production in the aviation industry.
The EcoPositioners have been part of Broetje-Automation’s portfolio since 2010, after a publicly funded research project kicked off the development in 2009. In the same year, the positioners were already able to impress with their first customer project in Europe. In 2011, EcoPositioners were launched on the Russian and Chinese markets. Since then, the technology has been firmly established within Broetje-Automation’s innovative solutions.
In addition to the delivery of positioning technology, Broetje-Automation is developing in the BiSconA project a modular adaptive gripper system as well as a digital image of the production environment. Broetje implements self-learning algorithms for continuous process optimization with a standardized control architecture and the integration of real-time capable measurement interfaces. This optimization and simultaneous digitization of the assembly of carbon fiber-reinforced polymer (CFRP) aircraft components significantly increase the performance and efficiency of the production processes. The BiSconA project thus represents an important milestone on the way to the digitized factory of the future.
With the EcoPositioner, Broetje-Automation offers a modular and reconfigurable positioning technology that guarantees maximum flexibility and product quality for aircraft assembly. Thanks to intelligent algorithms, the technology enables the compensation of mechanical and thermal influences and thus fast positioning cycles. The holistic mechatronic system combines mechanics, control and measurement technology from a single source, which further optimizes system availability.
The positioning technology can be used for a variety of manufacturing processes, such as the assembly of fuselage sections, the joining of sections to the fuselage or the connection of wings and tail units to the fuselage as part of final assembly.
Since 1979, Broetje-Automation has been developing innovative solutions for the automation of processes in the aerospace industry together with an entire ecosystem of partners. In the BiSconA project, Broetje-Automation is working on the factory of the future under the leadership of the ZAL Center for Applied Aviation Research together with its partners 3D Aero, Airbus, cenit and Fraunhofer IFAM.
Related Content
-
Cryo-compressed hydrogen, the best solution for storage and refueling stations?
Cryomotive’s CRYOGAS solution claims the highest storage density, lowest refueling cost and widest operating range without H2 losses while using one-fifth the carbon fiber required in compressed gas tanks.
-
Manufacturing the MFFD thermoplastic composite fuselage
Demonstrator’s upper, lower shells and assembly prove materials and new processes for lighter, cheaper and more sustainable high-rate future aircraft.
-
Plant tour: Spirit AeroSystems, Belfast, Northern Ireland, U.K.
Purpose-built facility employs resin transfer infusion (RTI) and assembly technology to manufacture today’s composite A220 wings, and prepares for future new programs and production ramp-ups.