Curve Works licenses 3D Core Kits to BeSpline startup
Thermoformed structural foam core kits leveraging reconfigurable mold technology are more readily available to North American manufacturers.
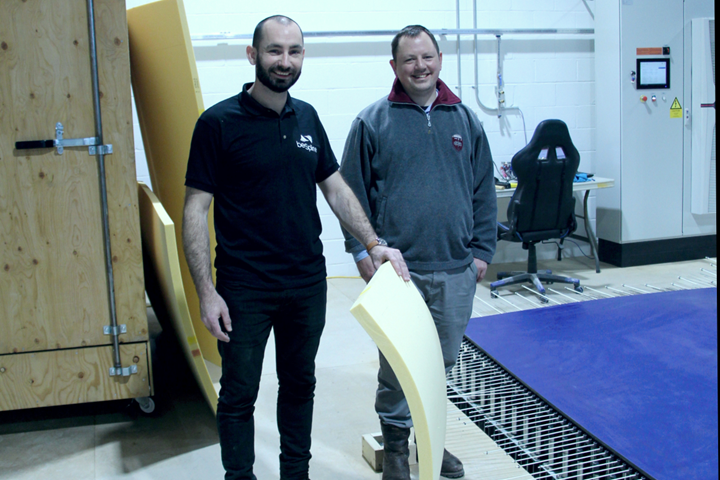
Photo Credit, all images: IND Group
Curve Works (Alphen aan den Rijn, Netherlands) is a specialist in structural foam core, sandwich panels and special composite layups with a vision to provide curved composite solutions using Adapa A/S’ (Aalborg, Denmark) reconfigurable mold technology. To better serve North American customers, the company has licensed its 3D Core Kits product to BeSpline (Sherbrooke, Quebec, Canada), a startup company launched in Oct. 2021.
BeSpline is the newest member of the IND Group (Quebec, Canada). Through its engineering branch, Effman, IND Group is already active in the composites industry, mainly in projection domes for flight simulators. IND Group has purchased an adaptive mold from Curve Works to further revolutionize the manufacture of these simulators.
The mix of BeSpline and Curve Works’ know-how — between BeSpline’s line of potential U.S.-based customers located on the East coast, and Curve Works’ success in the marine industry — are “a quality match,” says Tahira Ahmed, co-founder of Curve Works. “They [the BeSpline team] share our vision and we are pleased that those in North America can now be offered the same product and services as our European customers.”
Curve Works’ 3D Core Kit is the first product BeSpline has licensed and launched, with discussions over next product additions. 3D Core Kits are thermoformed structural foam core kits, with little to no spring-back and cut to size for the mold. They replace traditional kerf-cut or scrimmed cores and are said to drastically reduces the uptake of resin, resulting in a lighter structure, as well as improved structural performance. Since the launch, Curve Works says it has seen a rapid uptake of the product, primarily in yacht builds where lightweighting is essential.
“Just as we introduced an automated fiber placement [AFP] cell in 2021, we are bringing to North America a technology that will revolutionize composite manufacturing,” says Yoann Bonnefon, president of IND Group. “Adaptive molding is a technology that just doesn’t exist here in North America and we wanted to be the first to offer it.”
Related Content
-
Plant tour: Joby Aviation, Marina, Calif., U.S.
As the advanced air mobility market begins to take shape, market leader Joby Aviation works to industrialize composites manufacturing for its first-generation, composites-intensive, all-electric air taxi.
-
Natural fiber composites: Growing to fit sustainability needs
Led by global and industry-wide sustainability goals, commercial interest in flax and hemp fiber-reinforced composites grows into higher-performance, higher-volume applications.
-
Recycling end-of-life composite parts: New methods, markets
From infrastructure solutions to consumer products, Polish recycler Anmet and Netherlands-based researchers are developing new methods for repurposing wind turbine blades and other composite parts.