DITF develops textile sensors for composites
German Institutes of Textile and Fiber Research are advancing large-area sensors that can detect deformations and stress using printing onto textiles which are then incorporated into composite structures.
Share
Read Next
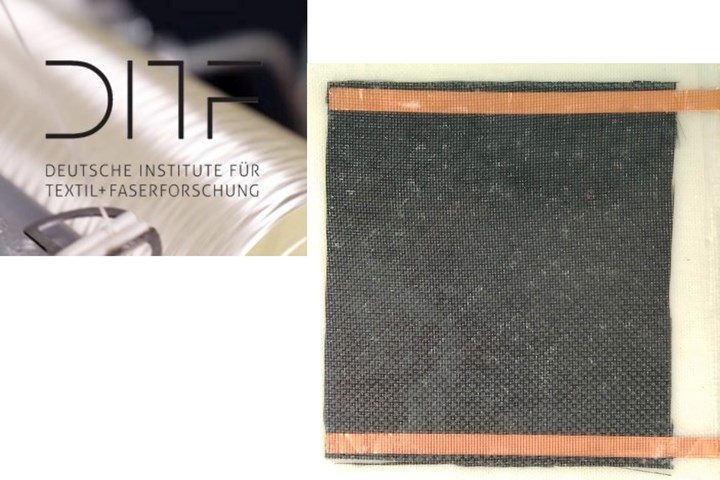
New sensor technology offers multidirectional and large-area sensing in fiber-reinforced composites for monitoring mechanical deformation and damage. Photo Credit: The German Institutes of Textile and Fiber Research (DITF)
The growth of composites technology for large-scale structures such as wind turbine blades, aircraft and automotive parts has created a need to monitor for damage and mechanical deformation. Current options are not fully satisfactory — small sensors cannot cover sufficient area, while fiber optic and piezoelectric sensors reportedly still require significant investment and expertise. The German Institutes of Textile and Fiber Research (DITF, Denkendorf) is looking to address this with its development of a large-area sensor produced by printing onto a reinforcing textile.
This DITF fabric sensor enables mechanical deformation to be detected over a large area as it responds with a measurable electrical resistance to external tension or pressure. By detecting and measuring mechanical stress parameters — such as the degree of deformation and bending speed on the shape of the sensor signal — even the smallest of deformations can be detected.
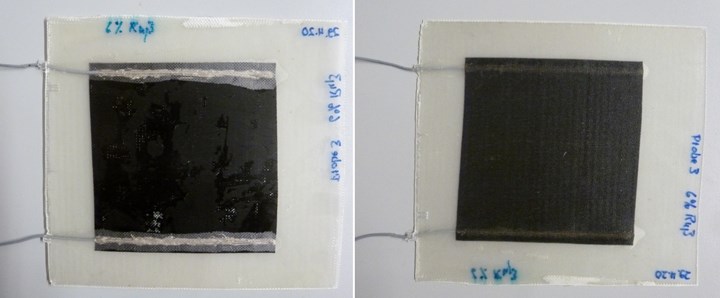
This sample of DITF’s sensing composite — front (left) and back (right) — is made by first printing a pattern of electrodes onto a glass fiber fabric and then coating with a 6% carbon black-filled polymer film before being infused with a matrix resin such as epoxy. Photo Credit: DITF
DITF researcher Dr. Reinhold Schneider, in his presentation at the Industrial Fabrics Association International (IFAI) EXPO 2021, described how the utilization of the reinforcing textile effectively allows for the creation of a textile-based sensor.
The process begins with screen or inkjet printing of an electroconductive interdigital pattern of electrodes onto the textile, which are used to record and measure the electrical resistance signal of the structure. This is followed by a coating or printing using sensor materials such as an electroconductive polymer or some form of carbon (e.g., powdered carbon black, milled carbon fiber, nanocarbon, etc.). Finally, the composite is manufactured, for example, using vacuum infusion processing with an epoxy matrix resin.
Once produced, the textile-based composite sensor can be tested for ohmic resistivity using a three-point bending method with mechanical load applied and released over a period of time. This is compared with the sensor data which correlate perfectly. In tests, it was revealed that the resistance change is dependent on the coating thickness and the percentage of carbon content in the printing paste. Specifically, a thin layer of sensing coating or printing produces a low amount of carbon, which results in a high resistance change.
“Effective large-scale composites monitoring is essential for health and safety as well as cost,” says Dr. Marie O’Mahony, an industry consultant, visiting professor at the Royal College of Art (RCA, London, U.K.) and author of several books on advanced and smart textiles. Beyond that, it is also an important way of reducing risk into the future as large scale composites become ever more ubiquitous.”
Related Content
-
21st century concrete: composite metamaterial with super compressability, energy harvesting
Material comprising 3D-printed, auxetic, reinforced polymer lattices in conductive cement matrix can compress up to 15% and generate electricity for lightweight, mechanically tunable structures with energy harvesting and sensing.
-
EOLIAN kicks off bio-based wind blade development
EU project will develop bio-based, repairable and recyclable vitrimer composites and advanced sensors for highly reliable, sustainable wind blades.
-
Acellent SHM 4.0 software supports real-time composites monitoring
Integrity and condition of a variety of metal and composite parts and structures is made possible through end-to-end software suites.