Fortify, polySpectra awarded $3 million by DOE to advance 3D-printed tooling
Fortify is to develop inexpensive, durable solutions for lightweighting automotive components using polymers, composites and metals, advancing vehicle part commercialization.
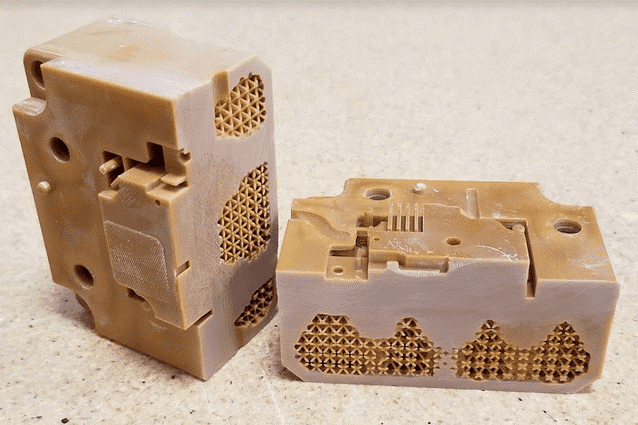
A 3D-printed mold tool printed on the Flux Core in DT resin designed with lattice design for lightweighting. Photo Credit: Fortify.
Fortify (Boston, Mass., U.S.), a provider of 3D printers for advanced photopolymer composites, and polySpectra (Berkeley, Calif., U.S.), a supplier of highly durable photopolymer resins, have announced strategic funding from the U.S. Department of Energy (DOE) aimed at decarbonizing the U.S. industrial sector, advancing clean energy manufacturing and improving the United States’ economic competitiveness and workforce diversity.
The DOE announced a selection of 30 projects that will receive $57.9 million in funding from the Advanced Manufacturing Office (AMO), awarding $3 million to polySpectra and Fortify, along with National Renewable Energy Laboratory (NREL, Golden, Colo., U.S.), MPI Systems (Poughkeepsie, N.Y., U.S.), RePliForm Inc. (Halethorpe, Md., U.S.) and Oak Ridge National Laboratory (ORNL, Knoxville, Tenn., U.S.) to develop durable direct additive tooling for automotive lightweighting via cyclic olefin resin-based composites.
“More than $8 billion is spent domestically each year on low-volume injection molding. The work addressed by this DOE award will pave the way for printed injection molding to unlock production applications,” Josh Martin, CEO and co-founder at Fortify, says. “By combining advanced materials and postprocessing with lightweight design principles, there is a significant opportunity to make a dent in the time to market, cost and performance of part production within the automotive industry and beyond.”
The goal of the project is to develop additively manufactured (AM) tooling with orders of magnitude improvements on cost and durability versus traditional CNC tooling with cycle times on par with CNC tooling. Through this collaboration, Fortify will be developing a next-generation solution capable of producing long-lasting inserts for the molding of production volumes of lightweight automotive components from engineering-grade materials, including polymers, composites and metals. With a focus on automotive, the proposed work will address the critical need to develop improved methods for commercial vehicle part production. This advanced manufacturing technology will reportedly accelerate improvements in transportation vehicle fuel efficiency and realize the corresponding energy savings and emissions reduction.
The project also features significant efforts to amplify underrepresented groups in the automotive manufacturing sector by building skills in additive manufacturing and rapid tooling. Through training and recruitment programs, the team hopes to create a diverse pool of candidates with the necessary additive tooling skills to enter the automotive workforce. Along the way, the project team will be mentoring and providing in-kind support to underrepresented innovators, including students and entrepreneurs.
“Olefin-based thermoset composites have been used for many decades in demanding applications such as wind turbine blades and fuel cell components, because they are among the most durable materials on the planet,” Raymond Weitekamp, polySpectra founder and principal investigator for the award, shares. “Under this research grant, we will leverage Nobel-winning chemistry to directly 3D print these robust composite cyclic olefin resins. The goal of the DOE project is to bring unprecedented materials durability to additive manufacturing, which will provide the industry with leverage for the decarbonization and reshoring of the U.S. manufacturing sector.”
The joint project will begin later this year.
Related Content
-
Active core molding: A new way to make composite parts
Koridion expandable material is combined with induction-heated molds to make high-quality, complex-shaped parts in minutes with 40% less material and 90% less energy, unlocking new possibilities in design and production.
-
ATLAM combines composite tape laying, large-scale thermoplastic 3D printing in one printhead
CEAD, GKN Aerospace Deutschland and TU Munich enable additive manufacturing of large composite tools and parts with low CTE and high mechanical properties.
-
The basics of composite drawing interpretation
Knowing the fundamentals for reading drawings — including master ply tables, ply definition diagrams and more — lays a foundation for proper composite design evaluation.