Henkel, Carbon partnership offers additive manufacturing solutions
The combination of Loctite materials and 3D-printing expertise opens doors for the adoption of high-performance additive manufacturing at scale for industrial customers.
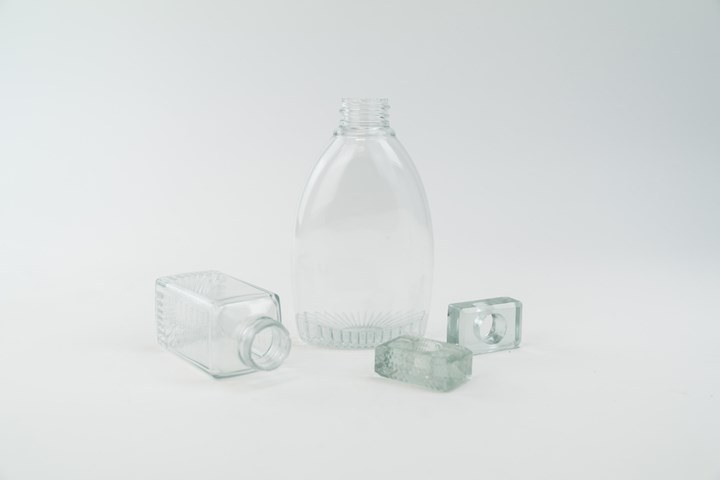
Loctite 3D IND405 Clear parts printed with the Carbon DLS process. Photo Credit: ProtoCAM
Henkel (Düsseldorf, Germany) and digital manufacturing solutions company Carbon (Redwood, Calif., U.S.) announced on Oct. 19 a partnership agreement to collaborate on Henkel’s Loctite-branded formulations validated for use with Carbon’s additive manufacturing process. As part of the collaboration the new Loctite 3D IND405 Clear material is immediately available to Carbon customers. The partnership agreement opens the door for industrial customers to access Henkel’s patented single-component technologies (1K) for use with the Carbon Digital Light Synthesis (Carbon DLS) 3D-printing process. It has not been indicated that the technology accommodates any type of reinforcement.
Loctite 3D IND405 Clear, a clear, tough, semirigid, 3D-printable material. Produced as a one-part resin, Henkel says the polymer is certified for Carbon printers, and is easily printed using the fast, reliable and consistent Carbon DLS process. With potential applications for enclosures and housings, light pipe prototypes, bottle prototypes, jigs and fixtures for production floors and more, Loctite 3D IND405 Clear offers engineers and designers a clear and durable material solution.
“Henkel is a leading provider of single-component technologies for additive manufacturing,” says Dr. Simon Mawson, senior vice president and head of 3D Printing at Henkel. “Our expanded partnership with Carbon allows us to deliver Loctite solutions to customers in the aerospace, automotive, industrial and medical markets. Together we offer an efficient additive manufacturing workflow that facilitates the production of durable end-use parts.”
Henkel adds that it is a longstanding trusted partner for providing industrial solutions to a broad variety of industries. Under its leading Loctite brand, the company offers a growing portfolio of resins for photopolymer 3D printing. By combining the Carbon DLS printing process with Henkel´s materials expertise and coupled with highly-vetted workflow print settings, the partners aim to drive more adoption of additive manufacturing at scale.
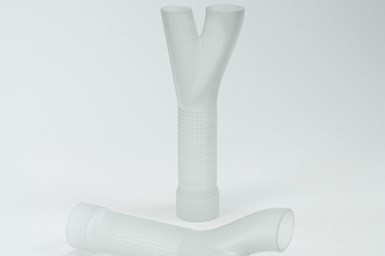
“We are excited to be partnering with Henkel to add this material to our portfolio of resins,” says Dr. Jason Rolland, senior vice president of Materials at Carbon. “Our customers have asked us for a clear material that is tough, durable and high-impact resistant. Loctite 3D IND405 meets those needs, and we’re committed to continuing to provide product developers the widest range of best-in-class materials.”
The partnership opens the door for Carbon customers to access Henkel's patented single-component materials, building on Carbon’s broad portfolio of resins that offer customers best-in-class polymer materials for a wide range of applications. With the Carbon DLS process and a growing portfolio of resins that deliver end-use performance, product developers and manufacturers can bring better products to market in less time.
“We are excited to partner with Carbon and combine our innovative, cutting-edge technologies to bring the Loctite 3D IND405 Clear material to market,” Mawson adds. “We believe that the single-component technologies from Loctite, coupled with the Carbon DLS process, provide a best-in-class solution that enables higher precision, better functionality and outstanding economics. Together that puts us in a great position to deliver on additive manufacturing’s promise to transform industrial manufacturing.”
Related Content
Carbon fiber, bionic design achieve peak performance in race-ready production vehicle
Porsche worked with Action Composites to design and manufacture an innovative carbon fiber safety cage option to lightweight one of its series race vehicles, built in a one-shot compression molding process.
Read MorePultrusion: The basics
A primer describing what pultrusion is, its advantages and disadvantages, and typical applications.
Read MorePlant tour: Spirit AeroSystems, Belfast, Northern Ireland, U.K.
Purpose-built facility employs resin transfer infusion (RTI) and assembly technology to manufacture today’s composite A220 wings, and prepares for future new programs and production ramp-ups.
Read MorePlant tour: Albany Engineered Composites, Rochester, N.H., U.S.
Efficient, high-quality, well-controlled composites manufacturing at volume is the mantra for this 3D weaving specialist.
Read MoreRead Next
Henkel strengthens 3D printing portfolio
Henkel acquires US-based additive manufacturing and industrial inkjet company.
Read MoreVIDEO: High-volume processing for fiberglass components
Cannon Ergos, a company specializing in high-ton presses and equipment for composites fabrication and plastics processing, displayed automotive and industrial components at CAMX 2024.
Read More“Structured air” TPS safeguards composite structures
Powered by an 85% air/15% pure polyimide aerogel, Blueshift’s novel material system protects structures during transient thermal events from -200°C to beyond 2400°C for rockets, battery boxes and more.
Read More