Hexcel signs long-term manufacturing contract with Boeing
Hexcel will produce HexPEKK-100 manufactured-to-print aerospace structures, including various air flow ducting applications and other supporting elements, for the Boeing 777X.
Share
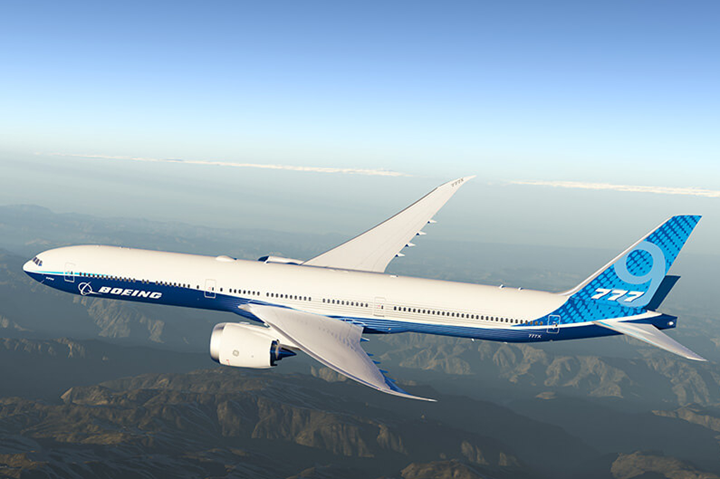
Photo Credit: Boeing
Hexcel Corp (Stamford, Conn., U.S.) has been awarded a multi-year contract to produce aerospace structures made with HexPEKK-100 for the Boeing (Chicago, Ill., U.S.) 777X. The parts will be manufactured at the company’s additive manufacturing site near Hartford, Conn., U.S.
According to Hexcel, HexPEKK components can be manufactured-to-print for commercial aerospace, defense and space applications where complexity, lightweight and strong mechanical performance are critical. These 3D-printed parts reportedly meet interior aircraft smoke and toxicity requirements. HexPEKK end-use components — as well as the company’s HexAM additive manufacturing process — were added to Boeing’s Qualified Provider List (QPL) in 2019.
“We are pleased that Boeing has selected our additive manufacturing technology for these parts, and we appreciate their confidence in HexPEKK solutions for commercial aerospace applications,” says Colleen Pritchett, Hexcel’s president of aerospace, Americas and fibers.
HexPEKK parts selected by Boeing for the 777X family include various air flow ducting applications, as well as other supporting elements on the aircraft. Production of these parts is expected to begin later this year.
Related Content
-
PEEK vs. PEKK vs. PAEK and continuous compression molding
Suppliers of thermoplastics and carbon fiber chime in regarding PEEK vs. PEKK, and now PAEK, as well as in-situ consolidation — the supply chain for thermoplastic tape composites continues to evolve.
-
Manufacturing the MFFD thermoplastic composite fuselage
Demonstrator’s upper, lower shells and assembly prove materials and new processes for lighter, cheaper and more sustainable high-rate future aircraft.
-
Developing repairs for thermoplastic composite aerostructures
HyPatchRepair project proves feasibility of automated process chain for welded thermoplastic composite patch repairs.