LMAT software reduces complex aerospace mold tool lead time
By incorporating this mathematical modeling software, Kaman UK has reduced lead time by up to 30%.
Share
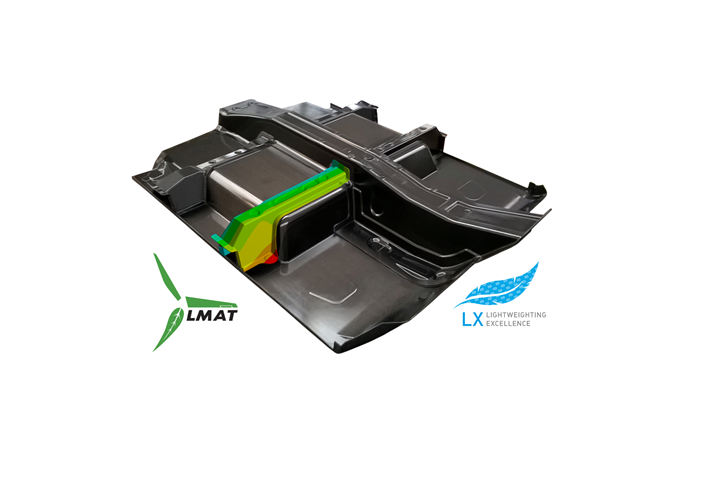
Source | Kaman UK
Aerospace supplier Kaman UK (Darwen, U.K.) reported on July 27 that it has significantly reduced development lead times for the design and manufacture of complex aerospace mold tools for composite part manufacture using “springback” modeling techniques. This has resulted in reduced time needed for manufacturing refinement of the composite mold tools, which in turn has decreased entry into service times and costs for the end user. A typical development phase that usually takes about 12 months, says Kaman, can be reduced by up to 30%.
The company says it has incorporated Lean Manufacturing and Assembly Technologies’ (LMAT, Darwen, England) mathematical modeling software to accurately predict and analyze the spring and twist of a carbon fiber composite parts during manufacture, and accordingly compensate mold tool surfaces to ensure design parameters are met. It is said that this removes the risk of manufacturing molds which have to be subsequently modified once initial parts have been manufactured and foreshortens project development times.
Kaman UK notes that when a composite mold tool is manufactured, its surface features don’t always define the composite part characteristics required due to certain factors. Acute angles and curvature and part characteristics such as cross-sectional thickness, the fiber architecture of the composite materials and thermal stresses inherent in the composite curing process all contribute to this variation.
Historically, says Kaman UK, this has necessitated that the mold tool is re-cut, adjusted or even remade based on data acquired during the part manufacturing development stage, a costly and time-consuming aspect of new part introduction.
According to the company, initial springback values of 4 degrees away from nominal are not uncommon with traditional “trial and error” manufacturing techniques for complex parts. The use of LMAT modeling enables these values to be predicted on a part by part basis, says Kaman, thus ensuring that the company can design and manufacture the required composite mold by accurately configuring the tool surface during the initial manufacturing process, without the need for subsequent modification.
“We are capable of enabling the use of new mold tools in weeks rather than months, which is removing a lot of risk and cost for us and making new product introduction much simpler and shorter for our customers. This is a huge step forward in composite manufacture development and greatly increases the ability of Kaman to assure the mold tool and therefore the part is right first time,” says James Scholfied, Kaman UK’s business development director.
Additionally, Kaman UK says it has also made long-term investments in its in-house metallic and composites capabilities along with a £1 million investment in a surface treatment line that achieved Nadcap (formerly NADCAP, the National Aerospace and Defense Contractors Accreditation Program) approval status last year, enabling the company to offer a full service “one-stop-shop” for fully integrated structures.
Related Content
-
Plant tour: Spirit AeroSystems, Belfast, Northern Ireland, U.K.
Purpose-built facility employs resin transfer infusion (RTI) and assembly technology to manufacture today’s composite A220 wings, and prepares for future new programs and production ramp-ups.
-
The potential for thermoplastic composite nacelles
Collins Aerospace draws on global team, decades of experience to demonstrate large, curved AFP and welded structures for the next generation of aircraft.
-
Plant tour: Joby Aviation, Marina, Calif., U.S.
As the advanced air mobility market begins to take shape, market leader Joby Aviation works to industrialize composites manufacturing for its first-generation, composites-intensive, all-electric air taxi.