Shape Machining increases workforce for F1 car projects
The company says its increased workforce will result in reduced lead times and quicker reactivity to tight deadlines.
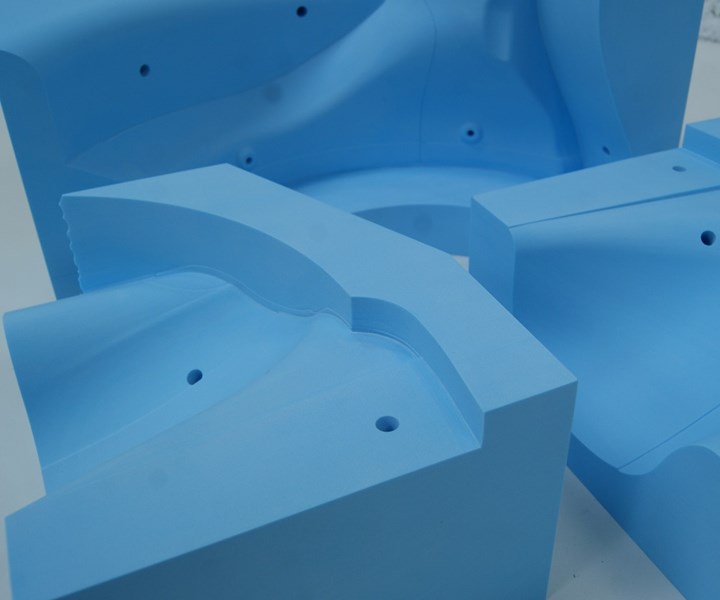
Patterns machined from epoxy tooling board. Source | Shape Group
Shape Machining Ltd. (Whitney, U.K.) has increased its workforce by employing additional pattern makers, which the company says will result in reduced lead times and quicker reactivity to tight deadlines for its F1 car projects.
“Having additional highly skilled people with experience within the F1 industry, has allowed increased capacity for car build and we hope to continue adding to this in 2020,” says Ryan Muller, managing director.
Since its founding in 2014, Shape says it has been steadily increasing its workforce and reviewing skill gaps, ensuring there are training plans in place and to guarantee cross-functional teams within the business.
“As well as additional direct staff, we now also have a dedicated scheduling team liaising with shop floor management, guaranteeing increased workflow in the business as well as better communication and ensuring the customers’ requirements are relayed from the office to the shop floor with zero errors,” Muller says.
Related Content
-
Carbon fiber, bionic design achieve peak performance in race-ready production vehicle
Porsche worked with Action Composites to design and manufacture an innovative carbon fiber safety cage option to lightweight one of its series race vehicles, built in a one-shot compression molding process.
-
Thermoplastic composites: Cracking the horizontal body panel nut
Versatile sandwich panel technology solves decades-long exterior automotive challenge.
-
Composites end markets: Automotive (2024)
Recent trends in automotive composites include new materials and developments for battery electric vehicles, hydrogen fuel cell technologies, and recycled and bio-based materials.