Spirit AeroSystems opens National Defense Prototype Center
The joint project with WSU-NIAR will spur the development of new high-temperature materials and ultra-competitive composites and attract new aviation, defense and space programs.
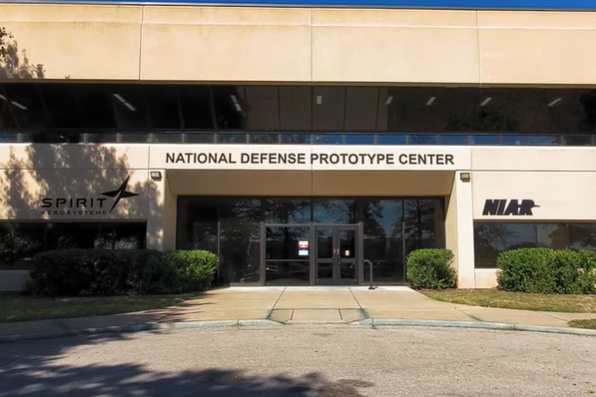
Photo Credit: Spirit AeroSystems
On Oct. 15, Spirit AeroSystems Holdings Inc. (Wichita, Kan., U.S.) held a grand opening event and ribbon cutting ceremony for its National Defense Prototype Center (NDPC), a joint project with Wichita State University’s (WSU) National Institute for Aviation Research (NIAR). This new research center will significantly expand Spirit’s capabilities and production efficiencies in the defense and space market.
“NIAR has been a tremendous partner in the development of the National Defense Prototype Center and enabling Wichita as a center for defense growth,” says Duane Hawkins, Spirit AeroSystems executive vice president; president, Defense and Space. “The NDPC provides a secure space for high-temperature materials testing, as well as development, prototyping and industrialization capabilities to support Spirit’s growth strategy targeting $1 billion of defense revenue by the mid-2020s.”
The research center comes soon after Kansas earned its designation as one of 11 Defense Manufacturing Communities by the Department of Defense (DoD). The Defense Manufacturing Community Support Program encourages long-term community investments to strengthen national security innovation and expand the capabilities of the defense manufacturing industrial ecosystem.
“The National Defense Prototype Center will improve research and development efforts of advanced materials and place Wichita at the center of future defense and space programs,” adds Senator Jerry Moran (R-Kan). “These programs, especially the advancement of hypersonic missiles, will rely on National Defense Prototype Center as the U.S. competes with foreign powers to defend our homeland.”
The National Defense Prototype Center encompasses more than 125,000 square feet of manufacturing and lab space with processing and characterization capabilities, including high-temperature testing, furnaces for fabricating and processing materials, multi-method non-destructive inspection (NDI), robotic automated fiber placement technology and a large autoclave. The center promotes the capacity to sustain broader and maximum throughput capabilities to support a high-priority national defense program.
“The more knowledge that can be generated and disseminated about high-temperature materials, the more these materials can be used, optimized and designed for specific objectives,” says John Tomblin, Wichita State’s senior vice president for Industry and Defense Programs and NIAR executive director. “This leads to reliable and safe products that enable the industry to go further, push faster and break through current design limitations. Not only is this a first for the state of Kansas, but for the nation in terms of testing capacity at these temperatures.”
The research center is reported to be the first of its kind with the ability to attract new aviation, defense and space programs with a focus on high-temperature materials, such as hypersonic missiles, that can withstand temperatures of 2,500-5,000°F. The NDPC offers distinctive capabilities and research technology that will spur the development of new high-temperature materials and ultra-competitive composites.
Related Content
-
Cryo-compressed hydrogen, the best solution for storage and refueling stations?
Cryomotive’s CRYOGAS solution claims the highest storage density, lowest refueling cost and widest operating range without H2 losses while using one-fifth the carbon fiber required in compressed gas tanks.
-
Syensqo becomes new Solvay specialty materials company
Syensqo represents what was Solvay Composite Materials, focused on delivering disruptive material technologies and supporting growing customer needs.
-
TPI manufactures all-composite Kenworth SuperTruck 2 cab
Class 8 diesel truck, now with a 20% lighter cab, achieves 136% freight efficiency improvement.