Trelleborg launches high-temperature tooling material for direct-to-part manufacture
The tooling material has operating temperature of up to +180ºC, low CTE, offers an alternative to aluminum, prepreg and steel for high-volume part production.
Share
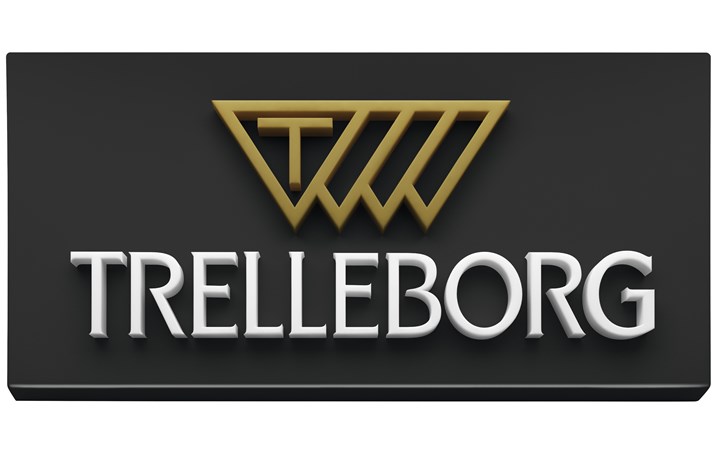
Photo Credit: Trelleborg
Trelleborg’s (Rochdale, U.K.) Applied Technologies operation has launched its new high-temperature, low coefficient of thermal expansion (CTE) tooling material, as part of a recent agreement with CFP Composites (Solihull, U.K.) to make TD1200 tooling available in Europe. According to Trelleborg, the material has an operating temperature of up to +180ºC, providing customers across Europe with a wider material choice.
According to Kerry Lyons, Business Development Manager for Trelleborg’s applied technologies operation, the tooling material will compliment Trelleborg’s existing range of tooling solutions and ensures the company can meet individual application requirements.
Trelleborg’s TD1200 tooling material also offers direct-to-part manufacturing as an alternative to aluminum, prepreg and steel for high-volume part production. Boards can be built into blocks and machined to a specified shape using traditional cutting tools, says the company. Further, the material is said to be easily processed to achieve either a matt or high-gloss finish, with minimal sealing required.
“We look forward to working closely with the [Trelleborg] team to provide TD1200 on short lead times, making it the perfect choice for thermally stable, high-volume part production in the aerospace, automotive and other industries,” says Simon Price, managing director of CFP Composites.
Related Content
-
Plant tour: Airtech International, Springfield, Tenn., U.S.
Fifty years of supplying materials for composites manufacturing includes custom fabrication and now aims to advance 3D-printed tooling, parts and new resins.
-
Optimized rib-reinforced hollow composites via printed molds
Addyx topology optimization and water-soluble mandrel enables simultaneous rib and skin layup for one-shot, high-strength, lightweight structures.
-
Plant tour: BeSpline/Addcomp, Sherbrooke, QC, Canada
Composites automation specialist increases access to next-gen technologies, including novel AFP systems and unique 3D parts using adaptive molds.