UMaine Composites Center 3D prints logistics vessel for U.S. Department of Defense
Two 3D-printed vessels capable of transporting two shipping containers and a Marine rifle squad with three days of supplies mark groundbreaking composite manufacturing milestone.
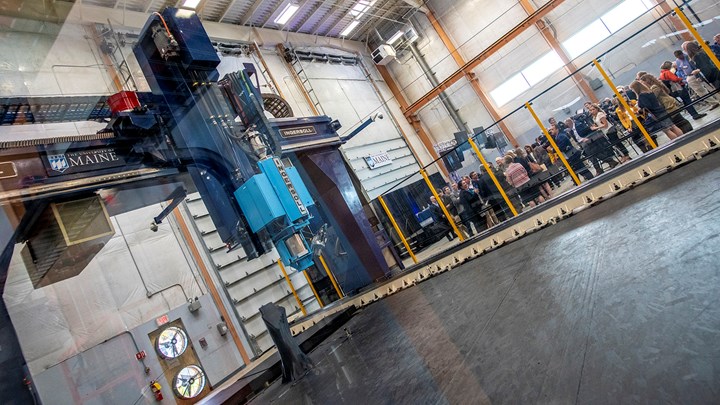
Photo Credit, all images: UMaine ASCC
In February 2022, the University of Maine Advanced Structures and Composites Center (UMaine ASCC, Orono, Maine, U.S.) reported that it had achieved a groundbreaking milestone in composite manufacturing with the production of two 3D-printed prototype logistics vessels for the U.S. Department of Defense (DOD).
Marine Corps Systems Command’s Advanced Manufacturing Operations Cell (AMOC), in collaboration with the UMaine ASCC, used advanced manufacturing techniques to successfully develop the expendable polymeric composite ship-to-shore vessels. The longer of the two vessels — the largest ever 3D-printed, UMaine contends — simulates ship-to-shore movement of 20-foot containers representing equipment and supplies. The second vessel can transport a Marine rifle-squad with organic equipment and three days of supplies. The prototypes can be connected, maximizing the transport capability of a single-tow vehicle.
The ship-to-shore logistics vessels align with the 38th Commandant of Marine Corps Gen. David Berger’s vision to “seek the affordable and plentiful at the expense of the exquisite and few when conceiving of the future amphibious portion of the fleet,” due to relatively low-cost, speed and ease of production.
“Our national security and economic security depend on an innovative and robust American manufacturing base,” Barbara K. McQuiston, director of defense research and engineering for Research and Technology, Office of the Secretary of Defense, says. “I applaud the University of Maine’s Advanced Structures and Composites Center for their pioneering work in the field of additive manufacturing [AM]. The advancements made here will bolster domestic manufacturing and ultimately support our warfighters in the field.”
Using traditional materials and methods, landing craft utility vessels can take over one year to produce. The UMaine Composites Center printed and assembled one of the two vessels in a month. The vessels were produced using the world’s largest polymer 3D printer, which the center commissioned on Oct. 10, 2019, earning three Guinness World Records.
To demonstrate the printer’s capabilities, the Composites Center 3D-printed a 5,000-pound boat, 3Dirigo, in 72 hours, and printed a U.S. Army communications shelter in 48 hours. The printer, with both additive and precise subtractive manufacturing capabilities, enables rapid prototyping for both defense and civilian applications.
“As the Marine Corps seeks to modernize logistics to better respond to current and future conflicts, advancements in AM will ensure we remain agile, lethal and expeditionary,” William Williford, executive director of Marine Corps Systems Command, notes.
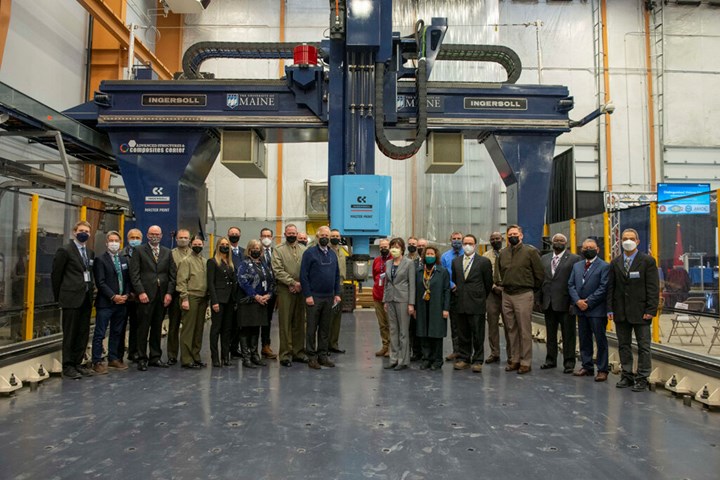
UMaine ASCC group.
The latest project to create the two 3D-printed logistics vessels is a significant milestone toward demonstrating advanced manufacturing techniques, UMaine notes, to rapidly constitute critical DOD assets closer to the point of need. The previously successful prototype was 3D printed in 2020, made from 25% aluminum. The vessels manufactured by the UMaine Composites Center are multimaterial composites with engineering polymer and fiber reinforcement.
“Two years ago, we demonstrated that it was possible to 3D print a 25-foot patrol vessel in three days. Since then, partnering with the DOD, we have been improving material properties, speeding up the printing process and connecting our printer with high-performance computers that can monitor the print,” Habib Dagher, executive director of the UMaine Composites Center says. “We thank our partners at the DOD, USMC, U.S. Army Engineer Research and Development Center [ERDC] and our Congressional delegation for their continued support. This groundbreaking achievement couldn’t have been possible if not for the tremendous effort of our dedicated team of 260 ASCC faculty researchers, staff and students.”
Related Content
Milliken & Co. partners with MMI Textiles to offer Tegris thermoplastic
The commercial market partnership enables easier access to the Tegris thermoplastic composite fabric for defense customers in the quantities that they require.
Read MoreFarnborough Airshow 2024 brings together aerospace innovation, collaboration
The week-long international airshow provided a hub for new announcements made by Boom Supersonic, Airbus, Boeing, GKN, GE, ZeroAvia, Eve, Bell, VoltAero, Eve and Lilium. CW has compiled several below.
Read MoreIndustrializing additive manufacturing in the defense/aerospace sector
GA-ASI demonstrates a path forward for the use of additive technologies for composite tooling, flight-qualified parts.
Read MoreMATECH C/ZrOC composite is deployed in hypersonic aeroshells
Ultra high-temperature insulating CMC targets hypersonics, space heat shields and other demanding applications, tested up to 2760°C under extreme stagnation pressures.
Read MoreRead Next
UMaine awarded $2.8 million to accelerate AM wind blade development
Additive manufacturing with bio-based, 100% recyclable feedstocks reinforced with wood can reduce construction time by six months and cut costs by 25-50%
Read MoreAll-recycled, needle-punched nonwoven CFRP slashes carbon footprint of Formula 2 seat
Dallara and Tenowo collaborate to produce a race-ready Formula 2 seat using recycled carbon fiber, reducing CO2 emissions by 97.5% compared to virgin materials.
Read MoreVIDEO: High-volume processing for fiberglass components
Cannon Ergos, a company specializing in high-ton presses and equipment for composites fabrication and plastics processing, displayed automotive and industrial components at CAMX 2024.
Read More